Today is the 40th anniversary of the LEGO Minifigure, so of course I have to make a
video about it, no matter HOW late it is.
Minifigures are my favorite thing about LEGO, and The LEGO Group released some cool promotional
historic artifacts about the minifigure to celebrate.
Brickset did some good articles highlighting these facts, which I've linked in the description.
But there was one segement included in the press kit that I wanted to highlight.
The prototype minifigures.
No, not the ones with no arms I recently highlighted in the top 10, THESE, which you saw a bit
of in the thumbnail - I saw them in some book a couple years back.
But as somebody who loves cancelled and prototype stuff, these are interesting because they're
so UGLY.
Like oh my gosh, thank GOD LEGO didn't go this direction for minifigures.
The moulded ears, nose, ears, eyes - yuck.
NO - NOT LIKE LEGO SIMPSONS.
These have square heads....
Like imagine a HAN SOLO or HARRY POTTER in this style.
Oof.
They also had some other prototypes, which just look bad just because they were made
with prototype materials - if finalized, they would've looked better, albeit bigger than
regular minifigures.
The brick built ones were weird too, not terrible, just odd.
Anyways, again, read those great Brickset articles, and if you like this kinda stuff
too, check out my cancelled LEGO set videos which should be up on the screen now.
Happy birthday LEGO minifigures!
I'll see you guys later, peace out, bye.
For more infomation >> The LEGO Minifigure Protoypes were UGLY. - Duration: 1:19.-------------------------------------------
Helsinki Tram System in Helsinki, Finland - Duration: 6:11.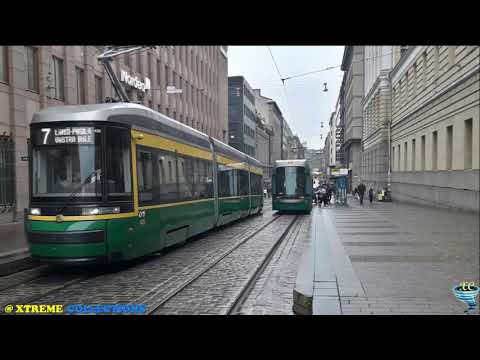
-------------------------------------------
Gorgeous Stunning 24' Kerbey MODERN, LUXURY Austin - Duration: 4:30.
Gorgeous Stunning 24' Kerbey MODERN, LUXURY Austin
-------------------------------------------
Сливные катки в WoT Blitz 5.2 - Duration: 2:25.
-------------------------------------------
Depois de alinhar o carro, ele continua puxando para o lado - Duration: 1:00.
-------------------------------------------
Atriz da Globo é acusada de intolerância religiosa no Encontro e pede perdão - Duration: 5:08.
-------------------------------------------
Grazi Massafera choca, recebe proposta de emissora e deve deixar a Globo - Duration: 4:32.
-------------------------------------------
Débora Falabella surpreende, faz publicação contra Bolsonaro e é atacada na internet - Duration: 4:46.
-------------------------------------------
Simaria faz grave denúncia, entrega novos detalhes de doença e expõe toda a verdade - Duration: 3:46.
-------------------------------------------
Separada de Xuxa, Sheila Mello fala a verdade, faz desabafo e manda recado para críticos - Duration: 5:09.
-------------------------------------------
Imitação de Marchetaria Losango | DIY | Mauro Tavares - Duration: 10:49.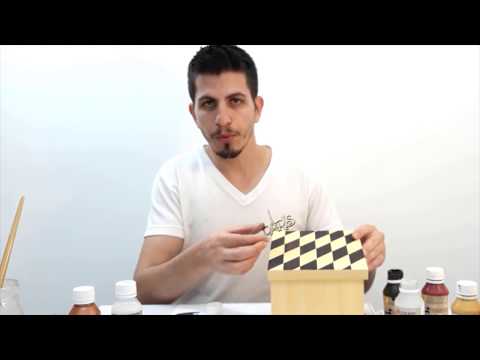
-------------------------------------------
Dental Veneers Makeover - That NO Cosmetic Dentist will tell you about! - Duration: 1:29.
you don't have to sit and suffer you can
be smiley and happy just like everybody else
you can just click these in and it works perfectly
I think that even if you have just a slight embarrassment with
your smile this is the way to go
it's just so much better than spending
thousands of dollars and having to ruin
your teeth
you deserve a good smile too
I think everyone deserves a smile and
everyone deserves to be happy
the only thing that we can do to spread
happiness is to smile at each other so
that's what I'm going to be doing for a long time
Learn More at Brighter Image Lab.com
-------------------------------------------
BNCC - 10 Competências: 3. Repertório Cultural - Duration: 13:42.
-------------------------------------------
Levi - My Love (Vídeo Oficial) - Duration: 3:24.
-------------------------------------------
Streets of Los Angeles, the good and the bad - Duration: 10:07.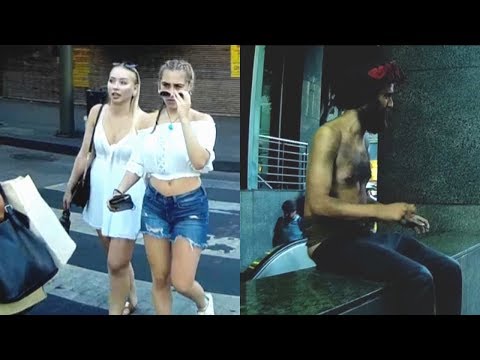
Activate subtitles for your language
How are you friends? again here Raul.
Once again, we will go through the streets of Los Angeles.
Where?
The Downtown Los Angeles.
What can I tell you about that?
And what about this?
A combination of the good and the bad of the city of Los Angeles.
Or rather, the county of Los Angeles.
Although, in this case.
As I was saying.
Here is the Downtown Los Angeles, what we are talking about.
What is this street? This is Hope Street.
I can not see the name of the other street.
It's the 7th street.
As you can see.
This is another one of those simple videos without editions.
This is the simple reality.
Everyone looks at what they want to see.
What do you want to look at?
Look at the good or the bad, that's your decision.
Within the bad that there is here.
What to say?
Here there are many homeless people.
You can see them in the streets.
What is inside good things?
Among the good things, this city is multicultural.
I'm going to cut the video, I'm going to continue recording from the other side of the street.
As I was saying.
It is a multicultural city where you can see people of all races.
Sometimes when you see blond people.
Suddenly you hear them speaking Russian or French.
And when you look at an Asian person, they are not always Chinese.
I said that they are not always Chinese, because that is what many people always say.
The reality is that they are often Japanese or sometimes Korean.
While we walk, you can see people around.
Maybe we're lucky and you can listen when they talk.
Today is a normal day like any other day on the streets of Los Angeles.
You can see the reality of the streets.
Wow friend, the bus ran away.
Inside the good things and the bad things.
Within what is good and what is bad, you will see what you want to see.
Here are some buildings.
At this moment it is late.
You can no longer see the sunlight, you only look at it above the small buildings.
Earlier there are many people around here.
What to say of the night?
In the night here it is dark and lonely.
But that's how all cities are.
We have to tell the truth.
All cities are dark and lonely at night.
Although some cities are more special.
For many people this video will look like very simple and without reason.
Especially for those people who live here in Los Angeles.
But you must understand.
There are people in other states or in another country.
They would like to know what the streets of downtown Los Angeles really are like.
Most people who make a video of this city only show you the beautiful and tourist places.
Maybe that's his style, on his YouTube channel.
I do not look for likes.
I just wanted to show you the reality.
These videos are simple and without much editing.
Sometimes I cut the video.
This is because I see someone who turns around or gets upset because he watches me recording with the camera.
I prefer to cut out that part of the video.
I do not like to show you a bad face in the video.
The noise of an ambulance is heard.
I think it's the firefigthers;
What can we do?
This is how the streets are always, here in Downtown Los Angeles.
The fire truck has already passed.
It's like some people say.
Here the siren of some vehicle always listening.
What do you want to see, the bad or the beautiful?
That is what I want to see.
Another pinch that my girlfriend is going to give me.
Or do you want to see that?
{Man shouting alone on the other sidewalk}
Everyone looks at what they want to see.
Again that noise comes.
Welcome to the streets of Los Angeles.
This is how the streets of Downtown Los Angeles always be.
The street where I am walking is the 7th.
If I keep walking straight, I'll enter Skid Row.
I really do not want to go into that place.
I'm just going to walk the limits of Skid Row.
I do not want to go where it is very ugly.
Let me continue here.
Here is a dark alley.
That smells really bad.
As I had told you before.
I know many people do not find the purpose of this video.
It's okay, everyone looks at what they want to see.
Nobody forces you to look at it.
But, you also have to understand.
There are people in other parts of the world.
They want to know what the streets of Los Angeles really are like.
Here is a simple video without edits.
This is 7th street and Los Angeles street.
Over there is Skid Row.
But, I do not want to enter that place.
I'd better go straight down this street.
Hello man.
Would you like a cold water?
Let me give you something.
Water
I do not have money
Chocolate
I do not have cigarettes
This is for you.
God bless you.
Not cigars, not money.
Poor people.
See you in the next video friend.
Here, at the limits of Skid Row.
I invite you to watch the following video.
I took a wrong turn in the streets of Los Angeles.
I took a turn in the wrong street.
{Get back}
Thanks for watching the video.
First person videos, around Los Angeles.
Exploring Los Angeles, with subtitles in Many languages.
-------------------------------------------
setting up for failure, What Would Jeff Do? Dog Training Tip of the Day #169 - Duration: 1:28.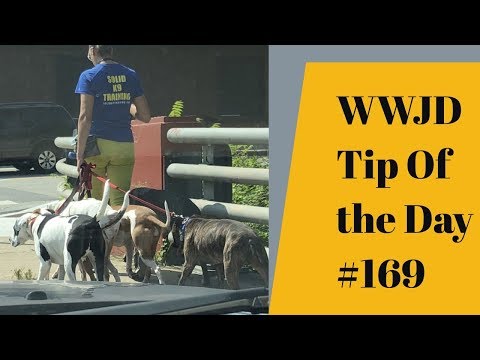
- Hey everybody, how are you?
It's Jeff Gellman of Solid K9 Training
with my What Would Jeff Do? Dog Training Tip of the Day.
Tip number 169.
Listen, whenever we're training a new behavior with a dog,
we're always setting the dog up for success.
You'll hear that a lot.
Always set the dog up for success so you can reward it.
I agree 100%.
But if you really wanna proof that dog.
If you really wanna make sure
that you push that dog to its limits,
you actually have to set that dog up for failure
because the world happens, life happens,
environmentals happen out there.
So what you wanna do is teach your dog what you want,
then, in order to proof your dog
that it will make the right decisions
in all different situations,
you actually have to set your dog up to fail
so then you can correct it for failing.
So you teach it, then, what you want.
That way it learns how to do what you want
and what it's supposed to do
in low environmental situations,
high environmental situations, heavy distractions.
It's very, very important.
So many people, they only want their dogs to succeed.
Just like everything in life.
Just like everything in life.
No, make it really difficult for your dog.
Once they understand the behavior,
that's how they learn.
That's how you proof things.
Jeff Gellman, Solid K9 Training.
Madly in love with you.
And I'll talk to you soon, bye.
-------------------------------------------
Depois de se separar de Xuxa, Sheila Mello está andando de cadeira de rodas - Duration: 4:47.
-------------------------------------------
Adorável Clichê - Traços {Letra - Legendado} - Duration: 3:35.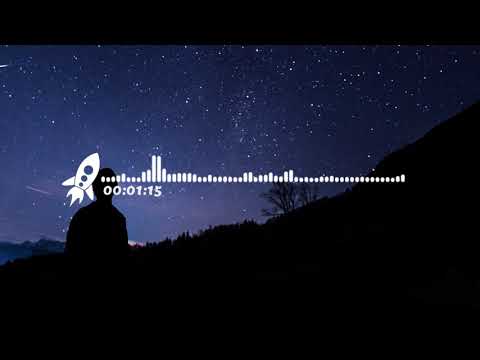
-------------------------------------------
OldBot for Tibia 11 - Everything about Marketbot [English subtitles) - Duration: 15:28.
There will be added english subtitles soon!
-------------------------------------------
詩眼倦天涯上映時間是什麼時候 電影詩眼倦天涯演員表 - Duration: 9:03.
-------------------------------------------
STAI SERENA! - PARIGI METTE AL BANDO LA TUTINA DA BLACK PANTHER INDOSSATA DALLA WILLIAMS, POLEMICHE - Duration: 5:54.
In difesa della tutina da catwoman sfoggiata da Serena Williams all' ultimo Roland Garros, e poi censurata dall' organizzazione, si è scomodato pure l' ex presidente dell' Iran Mahmoud Ahmadinejad, uno che nel suo Paese aveva riformato ma non abolito l' hijab, l' abbigliamento islamico
Due giorni fa, ha fatto un tweet chiedendo: «Perché #FrenchOpen non rispetta @serenawilliams? Sfortunatamente alcune persone in tutti i Paesi, incluso il mio, non hanno mai capito il vero significato della libertà»
La tutina che fa discutere è una specie di costume da supereroe nero e aderente
L' ex numero uno del tennis l' ha indossata, facendo storcere il naso al presidente della Federtennis transalpina Bernard Giudicelli, che poi, in un' intervista a Tennis Magazine, ha detto: «Dobbiamo rispettare il luogo e il gioco
Credo che si sia andati troppo oltre: certe tenute come l' ultima della Williams non saranno più consentite»
Parigi non è Wimbledon, dove ancora si è ammessi in campo solo in completino bianco, ma nessuno ha capito cosa avesse di inappropriato la tuta stile Black Panther in cui si è infilata Serena
La quale, da parte sua, non è stata neanche a polemizzare. Alla conferenza degli Us Open iniziati il 21 agosto, si è anzi giustificata, adducendo motivi di salute: la tutina servirebbe a favorire la circolazione e ridurre il rischio di embolie aumentato dopo la gravidanza e la nascita di Alexis Olympia Ohanian Jr
un anno fa. Di più, l' atleta ha fatto sapere che la prossima volta userà la gonna con sotto le calze elastiche
L' occasione, però, era troppo ghiotta per non essere cavalcata dallo sponsor dell' atleta
Quattro giorni fa, la Nike ha postato un bianco e nero di Serena in campo con la tutina incriminata, la racchetta alzata, dopo uno dei suoi colpi
La tuta scolpisce ogni muscolo e la potenza di Serena guizza anche nella fissità della fotografia
La scritta recita: «You can take the superhero out of her costume, but you can never take away her superpowers» (puoi togliere a un supereroe la sua tuta, ma non puoi portargli via i superpoteri)
È stato sufficiente a riaprire il caso, fin lì passato quasi in sordina. Mentre Serena scendeva in campo agli Us Open in tutù nero con gonna di tulle, i social si sono scatenati
C' è chi ha lanciato l' hasthag #BoycottFrenchOpen, con tanto di elenco dei corporate partners, così, tanto per invitarli a tagliare le sponsorizzazioni
C' è chi ha pubblicato l' indirizzo email di Giudicelli auspicando un' operazione mondiale di mail bombing
C' è chi ha accusato il censore di prendersela con Serena perché è nera (lei, non la tutina) e chi lo ha accusato di sessismo, perché vietare quella mise significa favorire gonne che scoprono le gambe e il Lato B
C' è chi si è ricordato di Anne White sul campo di Wimbledon, anno 1985, inguainata in una tutina assai simile, ma bianca
Allora, però, almeno s' era lamentata l' avversaria, Pam Shriver, che perse il match, accusò White d' averla distratta con l' abbigliamento eccentrico e chiese ai responsabili del torneo di vietare la tenuta
Al Roland Garros, invece, s' è lamentato solo Giudicelli. Insomma, molto rumore per poco
E, in fondo, forse, la vera notizia è che Ahmadinejad ha ufficialmente avviato un' operazione simpatia, magari in vista delle elezioni del 2020
Al momento in cui scriviamo, il suo ultimo tweet contro Donald Trump ha collezionato 229 like: niente al confronto dei 6
318 cuoricini tributati a quello pro Serena Williams.
-------------------------------------------
Le Donne della Notte (1948) Kenji Mizoguchi FILM COMPLETO [sub ita] - Duration: 1:10:41.
-------------------------------------------
1 Dead, 16 Sickened From Salmonella Outbreak Linked To Kosher Chicken: CDC - Duration: 0:25.
-------------------------------------------
Rehab Resolutions unveils anti-gravity treadmill - Duration: 0:54.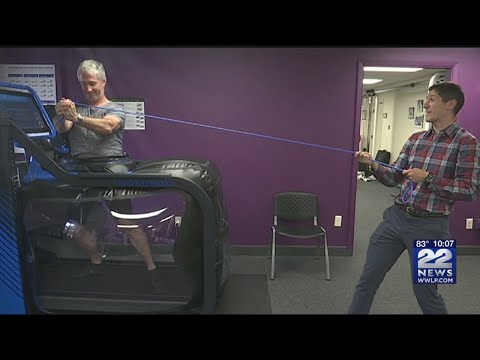
-------------------------------------------
The LEGO Minifigure Protoypes were UGLY. - Duration: 1:19.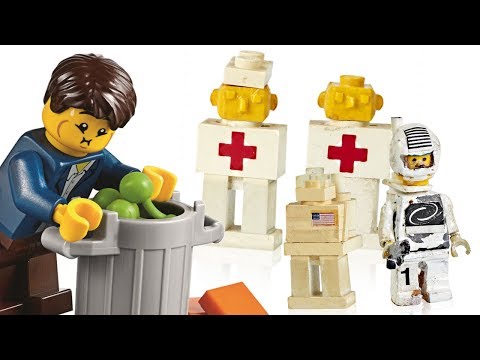
Today is the 40th anniversary of the LEGO Minifigure, so of course I have to make a
video about it, no matter HOW late it is.
Minifigures are my favorite thing about LEGO, and The LEGO Group released some cool promotional
historic artifacts about the minifigure to celebrate.
Brickset did some good articles highlighting these facts, which I've linked in the description.
But there was one segement included in the press kit that I wanted to highlight.
The prototype minifigures.
No, not the ones with no arms I recently highlighted in the top 10, THESE, which you saw a bit
of in the thumbnail - I saw them in some book a couple years back.
But as somebody who loves cancelled and prototype stuff, these are interesting because they're
so UGLY.
Like oh my gosh, thank GOD LEGO didn't go this direction for minifigures.
The moulded ears, nose, ears, eyes - yuck.
NO - NOT LIKE LEGO SIMPSONS.
These have square heads....
Like imagine a HAN SOLO or HARRY POTTER in this style.
Oof.
They also had some other prototypes, which just look bad just because they were made
with prototype materials - if finalized, they would've looked better, albeit bigger than
regular minifigures.
The brick built ones were weird too, not terrible, just odd.
Anyways, again, read those great Brickset articles, and if you like this kinda stuff
too, check out my cancelled LEGO set videos which should be up on the screen now.
Happy birthday LEGO minifigures!
I'll see you guys later, peace out, bye.
-------------------------------------------
Helsinki Tram System in Helsinki, Finland - Duration: 6:11.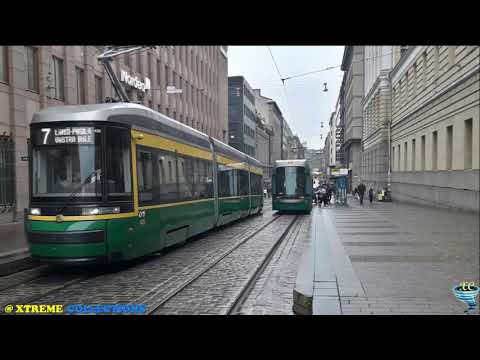
-------------------------------------------
Сливные катки в WoT Blitz 5.2 - Duration: 2:25.
-------------------------------------------
Gorgeous Stunning 24' Kerbey MODERN, LUXURY Austin - Duration: 4:30.
Gorgeous Stunning 24' Kerbey MODERN, LUXURY Austin
-------------------------------------------
Next On #RHOD: LeeAnne Locken Is In Tears Over Her Engagement (Season 3, Episode 3) | Bravo - Duration: 0:59.
-------------------------------------------
Survey Shows Most Construction Companies Can't Fill Positions - Duration: 2:44.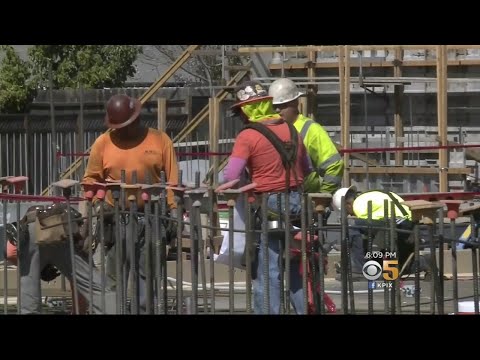
-------------------------------------------
setting up for failure, What Would Jeff Do? Dog Training Tip of the Day #169 - Duration: 1:28.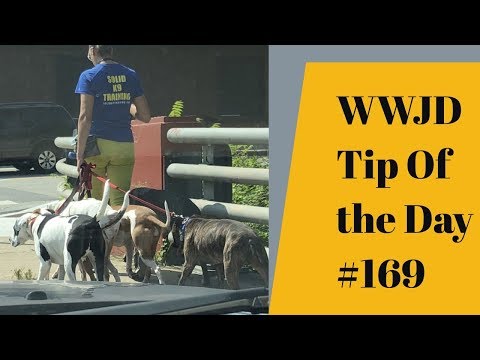
- Hey everybody, how are you?
It's Jeff Gellman of Solid K9 Training
with my What Would Jeff Do? Dog Training Tip of the Day.
Tip number 169.
Listen, whenever we're training a new behavior with a dog,
we're always setting the dog up for success.
You'll hear that a lot.
Always set the dog up for success so you can reward it.
I agree 100%.
But if you really wanna proof that dog.
If you really wanna make sure
that you push that dog to its limits,
you actually have to set that dog up for failure
because the world happens, life happens,
environmentals happen out there.
So what you wanna do is teach your dog what you want,
then, in order to proof your dog
that it will make the right decisions
in all different situations,
you actually have to set your dog up to fail
so then you can correct it for failing.
So you teach it, then, what you want.
That way it learns how to do what you want
and what it's supposed to do
in low environmental situations,
high environmental situations, heavy distractions.
It's very, very important.
So many people, they only want their dogs to succeed.
Just like everything in life.
Just like everything in life.
No, make it really difficult for your dog.
Once they understand the behavior,
that's how they learn.
That's how you proof things.
Jeff Gellman, Solid K9 Training.
Madly in love with you.
And I'll talk to you soon, bye.
-------------------------------------------
Ruling party, gov't, presidential office agree to work hand in hand to boost people's livelihoods - Duration: 0:39.
The South Korean government will keep close tabs on the country's real estate market,...
and vowed stronger action against any signs of speculation.
The government agreed this in a high level meeting with the presidential office and members
of the ruling Democratic Party of Korea on Thursday ahead of next week's regular parliamentary
session.
The groups also agreed to take preemptive measures to curb consumer prices ahead of
the Chuseok holiday next month,... and provide financial support for the self-employed and
small business owners during that period.
They also plan to hold such high level meetings once a month,... and hold closed door meetings
every week.
-------------------------------------------
The LEGO Minifigure Protoypes were UGLY. - Duration: 1:19.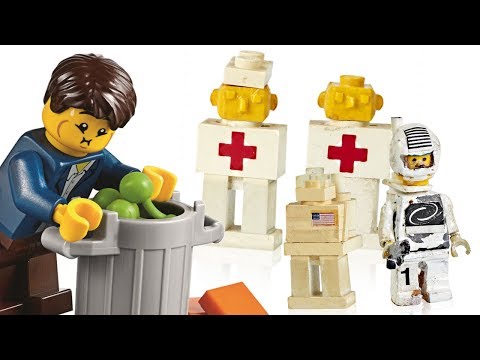
Today is the 40th anniversary of the LEGO Minifigure, so of course I have to make a
video about it, no matter HOW late it is.
Minifigures are my favorite thing about LEGO, and The LEGO Group released some cool promotional
historic artifacts about the minifigure to celebrate.
Brickset did some good articles highlighting these facts, which I've linked in the description.
But there was one segement included in the press kit that I wanted to highlight.
The prototype minifigures.
No, not the ones with no arms I recently highlighted in the top 10, THESE, which you saw a bit
of in the thumbnail - I saw them in some book a couple years back.
But as somebody who loves cancelled and prototype stuff, these are interesting because they're
so UGLY.
Like oh my gosh, thank GOD LEGO didn't go this direction for minifigures.
The moulded ears, nose, ears, eyes - yuck.
NO - NOT LIKE LEGO SIMPSONS.
These have square heads....
Like imagine a HAN SOLO or HARRY POTTER in this style.
Oof.
They also had some other prototypes, which just look bad just because they were made
with prototype materials - if finalized, they would've looked better, albeit bigger than
regular minifigures.
The brick built ones were weird too, not terrible, just odd.
Anyways, again, read those great Brickset articles, and if you like this kinda stuff
too, check out my cancelled LEGO set videos which should be up on the screen now.
Happy birthday LEGO minifigures!
I'll see you guys later, peace out, bye.
-------------------------------------------
Madison & Shea's Southeast Ride Home - Part 2 | Harley-Davidson - Duration: 1:01.
The biggest thing that we've been blown away from is just the community itself.
We get there and it's pretty intimidating all these guys have known each other for
years and years and here we are these young kids who are just learning to ride.
They could not have been kinder, they could not have welcomed us more
excitedly and I think it brought back memories probably from when they first
started.
I was born in Milwaukee and my dad went to work for Harley-Davidson when
he was 16 years old in 1922.
We've done most this trip by ourselves but it
is exponentially better when you have people riding alongside us.
You know that
feeling that that you had when you first left Ft. Lauderdale with a big
group?
That never goes away you feel that same feeling year after year after year after year after year.
-------------------------------------------
Dental Veneers Makeover - That NO Cosmetic Dentist will tell you about! - Duration: 1:29.
you don't have to sit and suffer you can
be smiley and happy just like everybody else
you can just click these in and it works perfectly
I think that even if you have just a slight embarrassment with
your smile this is the way to go
it's just so much better than spending
thousands of dollars and having to ruin
your teeth
you deserve a good smile too
I think everyone deserves a smile and
everyone deserves to be happy
the only thing that we can do to spread
happiness is to smile at each other so
that's what I'm going to be doing for a long time
Learn More at Brighter Image Lab.com
-------------------------------------------
Polson athlete navigates evolving world of concussion treatments - Duration: 3:38.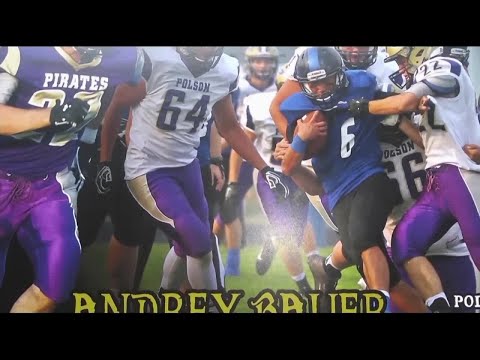
-------------------------------------------
3 Reasons Why I Left Social Media & How That Changed My Life - Duration: 5:28.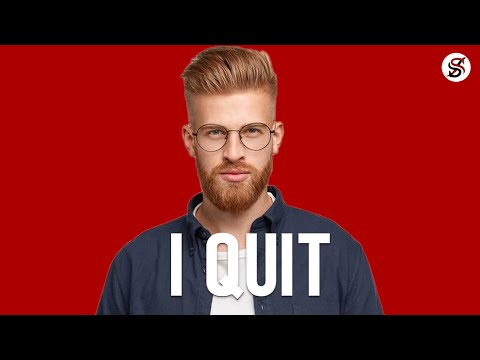
3 Reasons Why I Left Social Media & How That Changed My Life
I woke up one day in November, 2017 to announce to my digital friends that I'm divorcing
social media.
As expected, that surprised few people and some people even pleaded with me not to go,
just as if I'm disowning them.
Hahahaha.
Now, 9 months after that decision, I want to tell you the reasons why I left social
media, how that single decision has changed my life and what you can do if you're a
social media addict.
Let's get started with the 3 reasons why I forshook social media
First and the most important…
My Time.
Earl Nightingale once said; "If you spend an extra hour each day of
study in your chosen field, you will be a national expert in that field in five years
or less."
Unfortunately, I, like most other people found myself spending more than an hour every day
on social media.
What this simply means is that, if I invest the hours I was spending on social media to
study in my field, I will become a national expert in few years.
As if that's not bad enough, I had been addicted to making noise to people who never
care about what I had to say.
Most of us think our social media friends are our friends.
Maybe we're wrong!
Our 3,000 Facebook friends don't really care that much as we may want to believe.
The best we get from our "friends" on social media is envy and jealousy, then, hatred.
The picture of your new car, home or wristwatches will not make anyone like you more than they
did yesterday, instead, it makes them envy you and a better word is, you get it, hatred.
The third reason why I left social media; My Self-Esteem.
You ever posted a photo to Instagram and check it 20 times within 24 hours?
You ever wrote a post on Facebook and check the likes and comment the very first thing
when you wake up next day?
That's what I'm talking about.
I suddenly discovered that my precious life has been reduced to a mere baggage.
I had become an attention seeker who measured his success by other people's likes, shares
and comments.
No.
I worth more than that.
"It's Over!"
I quit the social media.
Now.
9 months after, I'm more productive because there's no distractions from the facebook
notifications and happier because I don't need anybody to like my photos nor do I have
to compare myself with a photoshoped achievement of another person.
Not only that, I now have better relationships with people I care so much about as I make
time to hang out and speak on phone more.
You probably have 3 questions, so let me answer your questions.
Do I advise you not to use social media?
No!
I still use social media for my business and you can do the same and even if for your personal
life, it's your life.
You can spend 3 hours every day on Instagram, Facebook and Whatsapp, as long as you like
the result you're getting, it's good for you my dear.
Question No. 2 Is YouTube a social media and why do I use
YouTube when I seem to hate social media?
Well, it all depends on what you do on Youtube.
I've seen so many people calling youtube a social media but I'll like to call it
the best university ever invented.
I spend hours on Youtube learning stuff I could never have learned anywhere else so
for me, YouTube is a school.
Question No. 3 What if you follow some really inspiring people
on social media?
Just like anything else, social media is not absolutely bad.
The weapon in the hand of a soldier is a wonderful instrument.
The same weapon in the hand of an armed robber is evil.
Social media can help you to connect with wonderful people you'll never meet otherwise
and you can follow some really inspiring people that'll change your life.
If you think the sacrifice of spending hours, envying other people's photoshopped life,
getting distracted by notifications while you should be productively busy really worth
what you get in return from the social media, then, you have no reason to consider leaving
social media.
-------------------------------------------
Get Clear Skin,Lightening Skin & Glowing Skin \\ How to Get Clear Skim In 5 Days // Skin Care Tips - Duration: 3:38.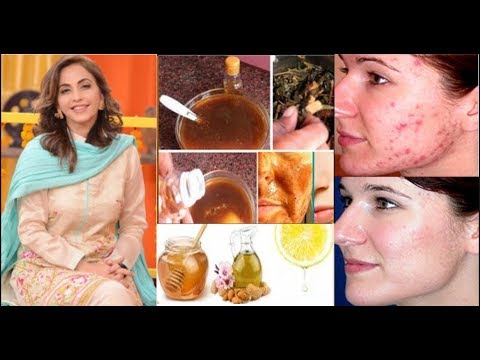
SUBSCRIBE to my channel & be a part of Rani G Family
SUBSCRIBE to my channel & be a part of Rani G Family
SUBSCRIBE to my channel & be a part of Rani G Family
-------------------------------------------
Very poor Lori hurt her tail hug mom tightly | Amari sad weakness can't care Lori |Monkey Daily 1545 - Duration: 10:23.
-------------------------------------------
Marine Water Treatment for Engine Cooling Systems - Duration: 13:38.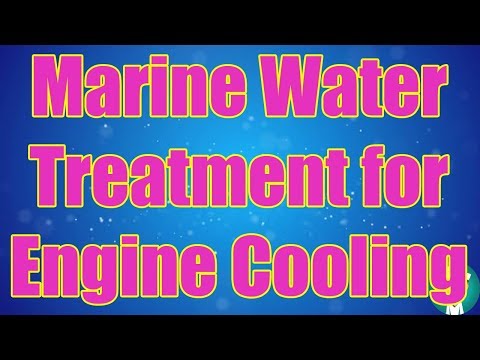
This course is designed to provide marine engineers and support staff with
an introduction to water treatment for engine cooling systems it agin x' with
an introduction to engine cooling systems and basic water chemistry the
course goes on to look at the problems caused by corrosion and scaling and the
water treatment solutions that are available the course examines the
importance of correct chemical dosing and control and the procedures for safe
sampling and testing there is a section on monitoring water test results and a
look at the tools and service that are available at the end of the course there
is a troubleshooting guide
marine diesel engines are used to provide ship's propulsion and electrical
power these engines are typically fueled by heavy fuel oil that is preheated and
cleaned by centrifugal filtration large quantities of waste heat are evolved
from the combustion processes some of the energy from this waste heat is
recovered and used to produce steam via exhaust gas boiler systems the majority
of the heat produced by combustion must be dissipated to prevent overheating and
failure of the engines moving parts such as the Pistons valves and associated
seals for this reason all marine engines are fitted with a water-filled cooling
system this diagram shows a schematic of a typical engine cooling circuit the
engine cooling circuit is designed to be a closed cooling system that is the
makeup is normally less than 5% of the system capacity per week we will review
how the combination of high temperatures and water conditions can lead to
problems of fouling corrosion and scale formation that can adversely affect the
performance of the engine we will also describe how good water treatment
practice will prevent such problems occurring the engine cooling circuit is
a closed system and absorbs large amounts of heat from the engine to
reject this heat sea water is in turn used to provide secondary cooling for
the engine cooling water sea water is introduced into the ship through open
inlets and stored in containing tanks called sea chests within the body of the
hull these cooling duties utilize a variety of heat exchanger designs which
can become severely fouled due to impurities and contamination in the sea
water supply the two main problematic organisms are the muscle mytilus edulis
and the barnacle balanus balinese these are common shelled filter-feeding forms
of marine life found around the world they can grow up to 10 centimetres in
length and 5 centimetres in diameter and cause severe fouling where sea water is
used as a coolant fully grown mussels and barnacles can be a
eliminated by filters and strainers however it is the freshly spawned
species villagers that cause problems these villages start life in a
microscopic size and can easily find their way into the cooling circuit once
in the system pipe work they attach themselves to surfaces using strong
elastic threads of protein once attached they can readily feed and grow and as
their size and numbers increase fouling and blockage of waterways takes place
the best approach is to eliminate the mussels and barnacles when they are in
their most vulnerable state has villages and prevent them from attaching and
growing this can be accomplished by the routine application of a proprietary
biocide or anti foul and optimum engine performance is linked to good cooling
efficiency the engine cooling circuit must be kept free of corrosion damage
and scale deposition in general water is never pure normal tap water contains a
number of constituents that are important and beneficial to our
Constitution the table shows that sea water has a predominance of sodium
chloride with significant amounts of calcium and magnesium salts these
impurities will cause severe operational problems if not removed or if the system
metals are not protected for example dissolved gases such as oxygen and
carbon dioxide will cause corrosion and dissolved salts such as calcium
carbonate will lead to scale deposition corrosion is an electrochemical process
where metal in contact with an electrolyte water is oxidized to
corrosion products local difference is in chemistry metallurgy and oxygen
concentrations will induce potential differences on the metal surface and a
cathode and anode is formed at the anode corrosion will take place and metal will
be lost characteristic deposits of iron oxide
rust are also formed there are a number of factors that can affect corrosion in
the engine cooling system as previously discussed the corrosion rates of metals
with respect to pH can vary depending on their
electrochemical nature for example the corrosion rate of Steel is greatly
increased in acid conditions as they prevent the formation of a protective
oxide layer the corrosion rate of mild steel reduces as pH Rises up to around
pH 13 because of the reducing solubility of iron oxide in this range copper
behaves in a similar manner aluminium and zinc because of their amphoteric
nature exhibit increased corrosion rates at extremes of pH as a general rule each
10 degrees Celsius increase in temperature doubles the rate of most
chemical reactions therefore an increase in temperature will increase the speed
of corrosion because the reactions at the cathode will proceed faster the rate
of oxygen diffusion is also increased up to around 80 degrees Celsius in an open
system the increase in corrosion rate begins to reduce because of the reduced
solubility of oxygen however in a closed system such as an engine cooling circuit
the oxygen cannot escape an increased corrosion rates will continue to be
observed as the temperature rises small negatively charged ions such as chloride
ions tend to gather at the anodic sites to electro chemically balanced the
positive ions Fe 2 plus etc produced by corrosion of the metal chlorides
increase the localized conductivity which creates an accelerated environment
for corrosion to progress in the marine environment it is usual to recommend
higher levels of corrosion inhibitor when sea water contamination has
occurred stress corrosion cracking is a phenomenon mostly associated with
stainless steels here the chloride ions are just the right size to enter the
atomic matrix of the metal and their concentration greatly accelerates
corrosion and causes the propagation of cracks in the metal catastrophic failure
is often the outcome of such corrosion mechanisms this relatively common form
of corrosion occurs when two dissimilar metals are connected and exposed to an
aqueous environment one metal becomes anodic and the other cathodic thus
setting up what is to a galvanic cell the anodic metal will
exhibit corrosion in preference to the cathodic one the most common example of
this type of corrosion is when copper and mild steel are connected in water
the mild steel becomes a notic because it will give up electrons more readily
than copper and will rapidly corrode this diagram shows the galvanic series
of common metals and alloys the closer the metals are together in the series
the less the corrosion rate and vice-versa the rate of corrosion at the
anode is very much related to the relative surface areas of the anodic and
cathodic metals at the high temperatures experienced metal surfaces in the engine
cooling system cavitation damage can be experienced the mechanism of cavitation
can be described as the instantaneous formation and collapse of vapor bubbles
in a liquid that is subject to rapid and intense localized pressure changes when
these phenomena act at the metal surface the hydrodynamic forces created by the
collapsing vapor bubbles create microscopic torpedoes of water these
torpedoes can have velocities of up to 500 meters per second and on impact with
the metal surface dislodge the protective oxide coating and deform the
metal itself the damaging effect of cavitation is typically seen on engine
liners and pump impellers where high temperatures and pressures cause
localized boiling the effect of scale is to thermally insulated of the cooling
surface and retard the flow of heat from the metal to the water the only way the
heat can get out is by raising the metal temperature and by raising the exit gas
temperature from the engine the former may endanger the engines structure the
latter will reduce engine efficiency the presence of scale on the heat transfer
surfaces of the cooling circuit can lead to a situation where the alkalinity in
the system begins to concentrate by evaporation within the scale deposit
high concentrations of OAH alkalinity can attack pipe work and in particular
lead to rapid failure of aluminium pipe work and components the primary method
of scale control engine cooling circuits is to ensure
that the make up water is delivered from an evaporator or is suitably pretreated
to remove scale forming salts if the system is made up with shore water then
the amount of makeup should be minimized to less than five percent per week and
the corrosion inhibitor selected should contain a suitable polymeric scale
inhibitor to help prevent deposition options do exist for minimizing
corrosion by improved design material selection and improved construction
techniques economics dictate that most systems are designed and fabricated in
such a way that the application of a chemical inhibitor is the most cost
effective option for corrosion control in engine cooling as we have seen
corrosion is an electrochemical circuit therefore any chemical treatment applied
to the water that stops the anodic or cathodic reactions will inhibit
corrosion corrosion inhibitors are classified on how they affect the
corrosion cell and can be categorized as a notic inhibitors cathodic inhibitors
combination inhibitors engine cooling systems typically contains several types
of metals for best corrosion protection a corrosion inhibitor must be applied
that can protect all types of metal corrosion inhibitors used in engine
cooling circuits are typically blends of nitrite alkalinity and Hazel's and other
specialist chemicals once a suitable corrosion inhibitor has been selected
and is applied to an engine cooling circuit general testing of water quality
would be undertaken to measure the levels of inhibitor pH and chlorides has
a check for contamination and hardness salts the performance of the corrosion
inhibitor can be monitored by directly measuring corrosion rates it is best
practice to install chemical dosing and control systems for engine cooling
systems the now track 1000 control system works by directly monitoring the
conductivity of the cooling water conductivity is proportional to the
level of corrosion inhibitor and the product is dosed to meet a control
setpoint routine water sampling and testing is carried out to control a
performance of treatments for engine cooling water
systems most treatment chemicals have a set of control parameters that need to
be maintained for correct performance appropriate sampling frequency and
procedures are important to get consistent results click on the pictures
for more information about the correct sampling procedures weekly testing is
adequate if the system is tight more frequent
testing is advised if there are significant water losses if the systems
are experiencing problems higher testing frequency will be required typical
control parameters are shown in the table below it is important that test
results are recorded both for quality purposes and to help with the
interpretation of trends this enables corrective decisions to be made quickly
and effectively water testing is an essential shipboard activity that should
be performed on a regular basis water proof is software developed to enable
the crew onboard the vessels to electronically store the results from
the water tests when entering the test results the user immediately gets
notified if the results are within the set limits or if corrective actions are
needed the test results can be sent to Williamson ship service for review a
report from our water treatment experts will be returned within days after the
defined test period is closed
-------------------------------------------
KOREA MOVIES 2018 || Maybe Someone Will Go About Remix || Loner - Missing - Duration: 1:10:24.
-------------------------------------------
Amazing Brand New Exquisite Tiny Home for sale in Eugene, Oregon - Duration: 2:47.
Amazing Brand New Exquisite Tiny Home for sale in Eugene, Oregon
-------------------------------------------
OldBot for Tibia 11 - Everything about Marketbot [English subtitles) - Duration: 15:28.
There will be added english subtitles soon!
-------------------------------------------
The Singing Traveler — Danny Ray (EmiSunshine) — Cover - Duration: 2:38.
Headin' down to Baton Rouge
To ease my worried mind
Headin' down to Baton Rouge
Maybe I'll go tonight
Maybe I'll go tonight
Been here in Knoxville town
With my Danny Ray
Forgot how Louisiana feels
In the month of May
In the month of May
[Scat singing]
Met my sister Lizzie Jane
Just the other night
We made our plans to leave Knoxville town
When that moon burns bright
Oh when that moon burns bright
Sit down by that Pontchartrain
And visit New Orleans
Rest a spell at Café du Monde
Big Easy rock me to sleep
Big Easy rock me to sleep
[Scat singing]
Danny Ray was good to me
For nigh on fifteen years
I ain't no good for leavin' him
Cryin' in his blue eyed tears
Cryin' in his blue eyed tears
Woman's made from Adam's bones
I got a mean streak three miles long
Danny Ray was good to me
But with that burnin' room I'm gone
But with that burnin' room I'm gone
[Scat singing]
Thanks for watching
Like & Subscribe
-------------------------------------------
'RHONY': Carole Slams Bethenny As A 'Bully' As They Go To War Over Past Insults - Daily News - Duration: 2:43.
The long-standing feud between Bethenny Frankel and Carole Radziwill continued during Part 2 of the 'RHONY' reunion special on Aug
29. Get all the details, here! Andy Cohen drew more attention to Carole Radziwill and Bethenny Frankel's fallen friendship during the Aug
29 episode of The Real Housewives of New York City, when he called attention to the Carole's latest blog posts, in which she seemed to hint that their feud has gotten "worse"
He actually read an excerpt from one of her blogs that appeared on Bravo's website, where she called Bethenny a "narcissist" and a "bully" who "lies about" everything
This led Bethenny to ask Carole where she got her medical degree. "No one needs a medical degree [to know these things about you], you just need two eyes," Carole shot back
Carole then went after Bethenny for "saying on television" that she "didn't have a career" — a statement that Bethenny still stands behind because she shot back by saying, "you don't have a career" while shrugging her shoulders
"Is this what you call female empowerment, Bethenny?" Carole asked. In turn, Bethenny started screaming at Carole, saying her remark came after she read what Carole had to say about her in her blogs
But Carole said she wasn't insulting Bethenny. Instead, she claims she was just trying to hold Bethenny "accountable" for all the mean things she said about her
So basically, the two ladies couldn't agree on who threw more insults throughout the season
Carole didn't feel she ever insulted Bethenny this season, but Andy rolled back some footage that showed otherwise
Bethenny insisted Carole "bashed" her many, many times, but Carole still denied doing such a thing
It seemed as though they weren't shown the old footage, and it was just later inserted after filming of the reunion completed
But even so, after it was disputed between Bethenny and Carole, Andy then took an opportunity to question Carole's denial
When he said, "You bashed each other on the show," Carole shot back, saying, "You're so full of s***, Andy
I didn't bash her on the show. I didn't bash her on the show. Are you kidding me?" Then, she thew some shade his way, asking, "Are you afraid of her, too?" As for Bethenny, she laughed as she watched the Carole and Andy start their own feud
-------------------------------------------
Madhyamik geography suggestion 2019| Madhyamik 2019 geography suggestion| Physics Academy Mahishadal - Duration: 10:23.
welcome to physics academy mahishadal
today we will discuss about madhyamik 2019 geography suggestion
today we will discuss the 4th chapter of madhyamik geography
-------------------------------------------
풍산개 믹스인줄 알았던 짱절미가 유달리 귀여웠던 이유 - Duration: 1:21.
45만 팔로워를 자랑하는 'SNS스타' 짱절미의 비밀이 밝혀져 온라인상을 뜨겁게 달구고 있다.
지난 28일 절미의 보호자는 에 게시글을 올렸다.
그는 "웰시랑 풍산 섞인 느낌도 들고 비글도 섞인 거 같다고 그러심"이라며 절미의 품종을 공개했다.
즉 절미는 풍산개와 웰시코기, 비글 3종류가 섞인 믹스견이라는 것.
누리꾼들은 이에 "어째 짧은 다리가 귀엽더라", "뭐든 사랑해 절미야", "바람직한 혼종이다"라는 등의 뜨거운 반응을 보였다.
한편 절미는 어미를 잃고 혼자 도랑에 빠져 물에 떠내려오다 지금의 보호자에게 발견됐다.
목숨을 잃을뻔한 절미의 사연은 삽시간에 온라인상을 뜨겁게 달구며 크게 화제를 모았다.
지난 17일 절미 보호자가 개설한 인스타그램은 벌써 45만 팔로워를 달성했다.
-------------------------------------------
Arsenal star Pierre-Emerick Aubameyang dances with Alexandre Lacazette - Duration: 2:35.
Arsenal strikers Pierre-Emerick Aubameyang and Alexandre Lacazette appeared to be in sync as they performed a dance during Wednesday's training session
Neither frontman has yet scored a goal this season but both appeared in high spirits as they prepared for Sunday's trip to Cardiff City by throwing some shapes
Aubameyang seemed to be in a particularly good mood and he was seen celebrating after hitting the net in a practice game
Former Dortmund forward Aubameyang then had a brief stint as a goalkeeper and fully embraced the opportunity by diving to make a spectacular save
Arsenal claimed their first win of the season on Saturday by overcoming West Ham 3-1 at the Emirates Stadium
Aubameyang started as the Gunners' lone striker but was joined by Lacazette, who entered the fray as a half-time substitute
Despite making an unconvincing start to the season and taking just three points from their first three games, Arsenal will be confident of beating Cardiff
The Welsh side have yet to score in the Premier League this term and were knocked out of the Carabao Cup 3-1 at home by Norwich on Tuesday night
Arsenal are unbeaten in their last 13 meetings with Cardiff — a run that dates back to 1961
Mesut Ozil missed last week's win over West Ham through illness but was back in training and seen battling Hector Bellerin for the ball
Right back Bellerin was not surprised that the Gunners beat West Ham and he told Arsenal Media: 'I wouldn't describe it as relief
'We've been working hard now for the last two months, so we knew it was just a question of time
'We had two tough games to start after lots of changes at the club.We knew it was a question of time, a question of scoring the chances that we had
No comments:
Post a Comment