The family is all together for our picnic!
But we just don't have the time for that right now...
Right.
You never really know when another kaiju is gonna show up...
We can't forget that Aizen is still out there too!
There's no way he wouldn't try to target us again!
Next time, on Ultraman R/B...
"Episode 10 - Minato Family Vacation!"
Color me with your power!
R/B!
For more infomation >> Ultraman R/B- Episode 10 PREVIEW (English Subs) - Duration: 0:20.-------------------------------------------
P3WM Fetherman R live hero show from Act.4 The Indigo Pledge (female protagonist ver) - Duration: 2:09.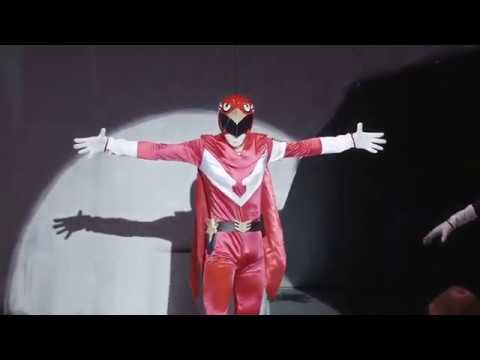
-------------------------------------------
1945, IMZ M-72 (Ural). Review & test-drive, part 1. Motorworld by V. Sheyanov classic bike museum - Duration: 5:59.
Today we will tell you and, let's say it bluntly, about the most significant military motorcycle of the Second World War
Someone will say that it was Harley-Davidson WLA, someone will think about the German BMW R-12
But, in fact, it was the Russian M-72
Someone will skeptically say: "What are you saying about? It's a copy of the German BMW R71." Quite right, but...
During the war years, there were produced more than 16 thousand units!
In absolutely harsh time, when all the factories on which production began, were evacuated
and in the shortest time, in a new place, in Irbit, among the mountains of the grizzle Urals, in the Sverdlovsk region, was re-established the production of these wonderful motorcycles at the facilities of the brewery
But let's back to the history. The summer of 1940 was a summer of panic in all the general staffs of all the armies of the world.
The general staff of the Workers' and Peasants' Red Army was also in the panic. You want to ask: "what was the reason to panic?".
The reason was that in June 1940, after only 5 weeks of the war, the strongest army of the world, the French army, have lost their war.
And if the tank wedges of the Wehrmacht could be called an arrow that pierced the French
That the tip of this arrow was the motorized parts of the Wehrmacht on motorcycles
When three motorcyclists with a heavy machine gun, could operate autonomously and simply cut off communication, the logistics nodes and communication centers of the opposing army,
the General Staffs suddenly realized that the moto-maneuvered parts would be the Alpha and Omega of the future war, and the Germans confirmed that in their operation against the French.
And then the wise Soviet engineers asked: "What should we do?"
Stalin, the legend speaks about it, wisely noted: "what is the last and best motorcycle of the Germans?"
Everyone immediately said - BMW R71. - So, copy it.
That was done in absolutely record-breaking, shortest time.
From August to November 1940, this motorcycle was developed and launched in the pre-series,
and then in early 1941 in batch production.
-------------------------------------------
Mercedes-Benz E-Klasse 200 D AUTOM WIDESCREEN Avantgarde Lease Edition navigatie - Duration: 1:06.
-------------------------------------------
Fiat Panda 1.2I 5DRS EDIZIONE COOL AIRCO 1E EIGENAAR - Duration: 0:46.
-------------------------------------------
WATCH LIVE: The National for Friday August 31, 2018 — NAFTA, Pipeline Reaction, E-Cigarettes - Duration: 1:04:17.
-------------------------------------------
Peugeot 208 1.4 e-HDi Blue Lease 5Drs.NAP,Nwe A.P.K - Duration: 1:11.
-------------------------------------------
Mercedes-Benz E-Klasse 200 D AUTOM WIDESCREEN Avantgarde Lease Edition navigatie - Duration: 1:06.
-------------------------------------------
Mercedes-Benz 190 1.8 E CLASS Lmv-Trekhaak-Radio/cd-Cv NL auto 2e eigen - Duration: 1:10.
-------------------------------------------
VLOG #24 What I eat in a day, sujebi and shrimp buchimgae(Korean style pancake) | Honeykki 꿀키 - Duration: 9:58.
It's been raining for days..
I craved sujebi because of the rain, so I had it for lunch.
Flour(about 1cup per portion)
salt
sesame oil or vegetable oil (My mom said it makes for more glutinous dough)
water (about half the amount of flour)
Knead the dough until a ball forms, cover with cling wrap for 30min.
In a pot, add the water and broth pack(like with anchovy and seaweed?) and simmer.
When the broth boils, prepare the veggies. (any veggies you want)
potato
carrot
Korean green zucchini (green squash)
Remove the broth pack and add sliced potato.
With wet hands, tear out flat bite sized pieces of dough into the broth.
soy sauce for the color and salt for seasoning.
pepper
chopped garlic
green onion
bring to the boil and it's done!
So hearty!
My puppy's snack time!
My current favorite drink: calamansi + passion fruit syrup + still or sparkling water
Ah.. my mouth is watering..
It's raining again! So I decided my dinner is shrimp buchimgae.
Korean chives
Korean green zucchini (green squash)
carrot
onion
I failed with measurement again… again!
Season with salt and pepper.
flour
egg
water
shrimp
(Tip: Oli the center of the buchimgae for crispiness all over)
Inevitably, makgelri(Korean rice wine)
(I like drinking the top clean part of makgelri without shaking it)
Late night buchimgae feast.
-------------------------------------------
Owlmaymay - Duration: 0:14.
Kill oneself
-------------------------------------------
떴다! 더보이즈(Come On! THE BOYZ): 여름방학 RPG편 주연, 제이콥, 케빈's Diary (JUYEON, JACOB, KEVIN's Diary) - Duration: 2:13.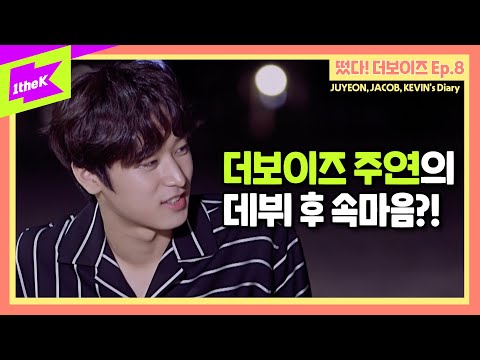
(Come ON! The BOYZ Summer Vacation RPG)
(Juyeon, Jacob and Kevin's Diary) (The Amazing Night Beach of The BOYZ)
(Juyeon, Jacob and Kevin's night at the beach)
(An earnest sharing of each one's innermost feelings)
It's been a while since I've been to the beach at night
Walking here it felt kind of weird
Why?
I used to come to Kangwon beaches a lot
It brought back a lot of memories
I started missing my family
(Oh really?)
How about you and Kevin?
Don't you miss your families?
Of course
Just walking along the beach and feeling the cool winds
All the conversations I've had I remember these memories
Driving along the beach
Feeling the sea winds
It feels great
I think we all enjoy sports
We did a lot of leisure sports during the break
All the sports we can do during the winter
Skiing and snowboarding That's going to be fun
Or making snowmen
- Snow fights - Igloos
Snow fights are fun
Snow fights are going to be fun
When it's dark you can see falling stars
I'm going to lie down
Oh yeah
I saw a falling star!
Really?
Did you see just now?
There are so many stars
Lying down was a good idea
I know, right?
It was a time of healing
Looking at just the sky
Now that summer break is over
We have to get back to work
Let's get back to work!
How do you say that in English?
Get back to work!
Back to work!
Shall we do a 'Yahoo!?'
- How about 'Let's go The BOYZ'? - Okay
One two three
Let's go The BOYZ!
(We're cheering you on!)
-------------------------------------------
Bruna Marquezine se manifesta após ser acusada de ser conhecida apenas como "namorada do Neymar" - Duration: 4:45.
-------------------------------------------
A fulfilling day in Hongdefa FLour Milling Machine Company - Duration: 1:18.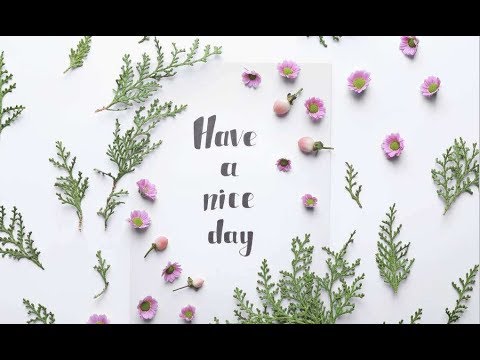
-------------------------------------------
Advanced English Pronunciation Practice - Quick Easy Pronunciation Tips - Duration: 15:16.
Advanced English Pronunciation Practice - Quick Easy Pronunciation Tips
-------------------------------------------
AUTARQUIAS DO HUMOR 190 - Duration: 31:14.
-------------------------------------------
how to add dial pad my photo||अपनी फोटो को call Keyboard में लगाने का best tricks..... - Duration: 3:01.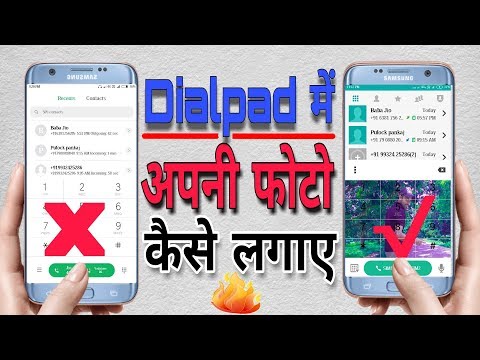
-------------------------------------------
Vital Caps Funciona Mesmo Depoimentos Bula - Duration: 2:16.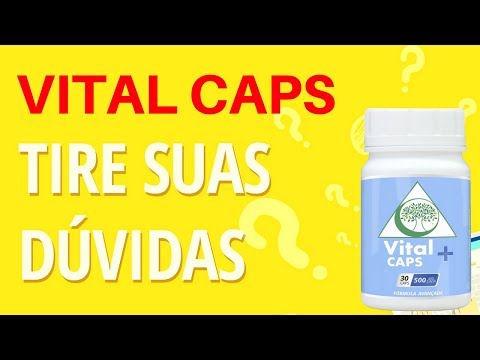
-------------------------------------------
Precisamos de sua ajuda Bradesco AG: 1545-8 CC: 0100825-0 - Duration: 3:44.
-------------------------------------------
Ultraman R/B- Episode 10 PREVIEW (English Subs) - Duration: 0:20.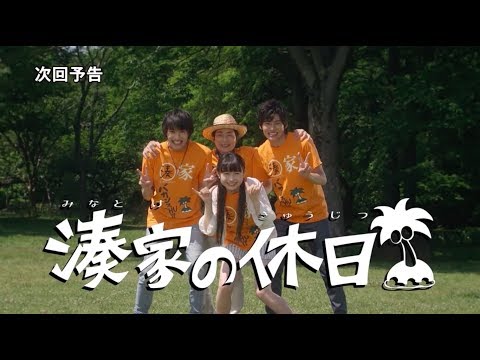
The family is all together for our picnic!
But we just don't have the time for that right now...
Right.
You never really know when another kaiju is gonna show up...
We can't forget that Aizen is still out there too!
There's no way he wouldn't try to target us again!
Next time, on Ultraman R/B...
"Episode 10 - Minato Family Vacation!"
Color me with your power!
R/B!
-------------------------------------------
P3WM Fetherman R live hero show from Act.4 The Indigo Pledge (female protagonist ver) - Duration: 2:09.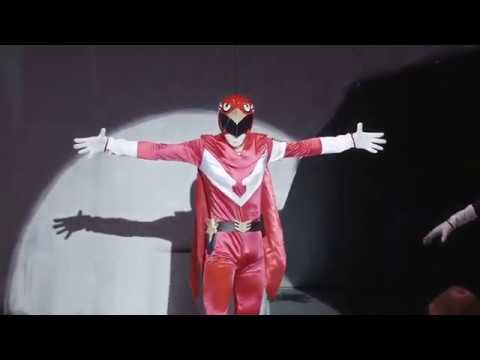
-------------------------------------------
1945, IMZ M-72 (Ural). Review & test-drive, part 1. Motorworld by V. Sheyanov classic bike museum - Duration: 5:59.
Today we will tell you and, let's say it bluntly, about the most significant military motorcycle of the Second World War
Someone will say that it was Harley-Davidson WLA, someone will think about the German BMW R-12
But, in fact, it was the Russian M-72
Someone will skeptically say: "What are you saying about? It's a copy of the German BMW R71." Quite right, but...
During the war years, there were produced more than 16 thousand units!
In absolutely harsh time, when all the factories on which production began, were evacuated
and in the shortest time, in a new place, in Irbit, among the mountains of the grizzle Urals, in the Sverdlovsk region, was re-established the production of these wonderful motorcycles at the facilities of the brewery
But let's back to the history. The summer of 1940 was a summer of panic in all the general staffs of all the armies of the world.
The general staff of the Workers' and Peasants' Red Army was also in the panic. You want to ask: "what was the reason to panic?".
The reason was that in June 1940, after only 5 weeks of the war, the strongest army of the world, the French army, have lost their war.
And if the tank wedges of the Wehrmacht could be called an arrow that pierced the French
That the tip of this arrow was the motorized parts of the Wehrmacht on motorcycles
When three motorcyclists with a heavy machine gun, could operate autonomously and simply cut off communication, the logistics nodes and communication centers of the opposing army,
the General Staffs suddenly realized that the moto-maneuvered parts would be the Alpha and Omega of the future war, and the Germans confirmed that in their operation against the French.
And then the wise Soviet engineers asked: "What should we do?"
Stalin, the legend speaks about it, wisely noted: "what is the last and best motorcycle of the Germans?"
Everyone immediately said - BMW R71. - So, copy it.
That was done in absolutely record-breaking, shortest time.
From August to November 1940, this motorcycle was developed and launched in the pre-series,
and then in early 1941 in batch production.
-------------------------------------------
Mercedes-Benz E-Klasse 200 D AUTOM WIDESCREEN Avantgarde Lease Edition navigatie - Duration: 1:06.
-------------------------------------------
Fiat Panda 1.2I 5DRS EDIZIONE COOL AIRCO 1E EIGENAAR - Duration: 0:46.
-------------------------------------------
Abarth 500 1.4 T-Jet 160pk Abarth Turismo - Duration: 1:12.
-------------------------------------------
Volvo C70 Convertible 2.4 T LUXURY Cabrio,Hardtop,Airco,Trekhaak,Cruise,youngtimer - Duration: 1:08.
-------------------------------------------
高云翔案件女主发声: 喜欢的是王晶, 高云翔顺水推舟惹大祸 - Duration: 6:19.
-------------------------------------------
A weekend of negotiations for many school districts in Washington - Duration: 2:16.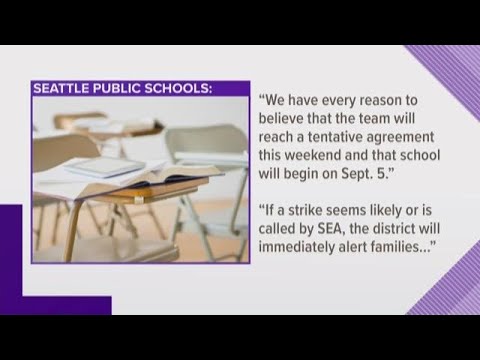
-------------------------------------------
Great time for Timo newborn enjoy sweet milk mom | Timo happy sweet milk & sleep | Monkey Daily 1564 - Duration: 10:27.
-------------------------------------------
US economy is freighted down with debt: David Stockman - Duration: 5:51.
-------------------------------------------
World's Most Beautiful Samford Valley Small House in Australia - Duration: 5:35.
World's Most Beautiful Samford Valley Small House in Australia
-------------------------------------------
Study No. 24 | Classical & Fingerstyle Guitar - Duration: 1:08.
Study No. 24 | Classical & Fingerstyle Guitar
-------------------------------------------
Kunal Kemmu shares beautiful picture of daughter Inaaya and we can't stop looking at her eyes! - Duration: 2:22.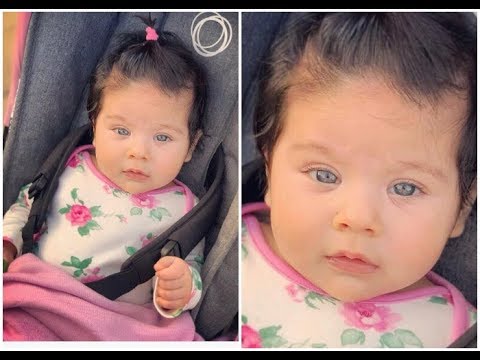
Kunal Kemmu shares beautiful picture of daughter Inaaya and we can't stop looking at her eyes!
Kunal Kemmu shares beautiful picture of daughter Inaaya and we can't stop looking into her eyes!.
On October 6, 2017 Kunal Kemmu and wife Soha Ali Khan welcomed their little bundle of joy to this world. Bollywood actress Soha Ali Khan gave birth to a baby girl on the ninth day of Navratri (Navmi).
The couple named their daughter Inaaya Naumi Kemmu. Earlier, the couple shared the picture of their munchkin on social media, which set the internet abuzz in no time.
And today, on Christmas, daddy Kunal Kemmu shared another beautiful picture of their 2 months-old daughter on Instagram. Check the picture here.
It's a merry Christmas everyday when you got the best gift in the world look at you with so much love .
He wrote: It's a merry Christmas everyday when you got the best gift in the world look at you with so much love.
Although, baby Inaaya is looking ethereal on a whole, but we can't stop looking at her eyes. The baby has got hazel eyes, just like her cousin Taimur Ali Khan.
The tiny ponytail on her head reminds us of our childhood when our mother used to tie our hair in the funniest manner possible.
Baby Inaaya and Baby Taimur are ruling the internet hands down.
Earlier, Kunal Kemmu shared a picture of baby Inaaya on Children's Day wishing his fans on the occasion. The baby was too young and fragile at that time. But she has grown up a bit since that time for sure.
Wishing all the children everywhere and my little munchkin a very happy children's day. May your innocence continue to inspire us to be better people.
Soha Ali Khan, ahead of her book launch, posted a picture of herself with her daughter on Instagram. In the picture, the new mommy and author of the book 'The Perils of Being Moderately Famous', are reading the book.
However, baby Inaaya's face is partially covered by the book in front of her. ICYMI, Kunal Kemmu having a daddy-daughter moment with his baby in this picture.
-------------------------------------------
Inside Phillip Fulmer's bar recommendation - Duration: 1:51.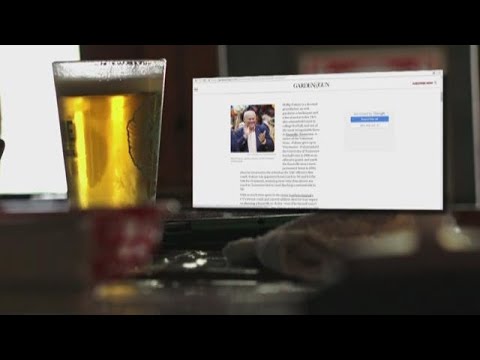
-------------------------------------------
Undaunted Raiding Handbook: Trialing as a Mythic Raider - Duration: 3:43.
[Transcription available in the description]
-------------------------------------------
Why the Duchess Kate Middleton only ever carries a clutch Bag - and This Is The Reason - Duration: 4:30.
-------------------------------------------
Undaunted Raiding Handbook: Attendance Policy - Duration: 3:24.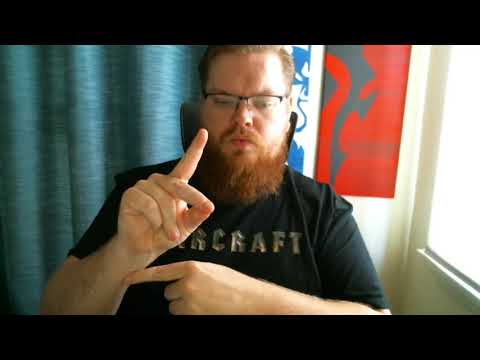
[Transcription available in description]
-------------------------------------------
香蜜沉沉烬如霜 第54-55-56-57集 锦觅伤心欲绝,月下仙人红红知道后赶紧跑到魔界找凤娃,可怜的月老在 天界被润玉让人拖走不算 - Duration: 5:12.
-------------------------------------------
ENG SUB | You Shouldn't Do This at the Office [Office Watch] EP08. Time and a day - Duration: 7:22.
-------------------------------------------
Amazing Sage - 24' Tiny House on Wheels for sale in Houston, Texas - Duration: 4:20.
Amazing Sage - 24' Tiny House on Wheels for sale in Houston, Texas
-------------------------------------------
Marine Steam Boiler - Duration: 11:56.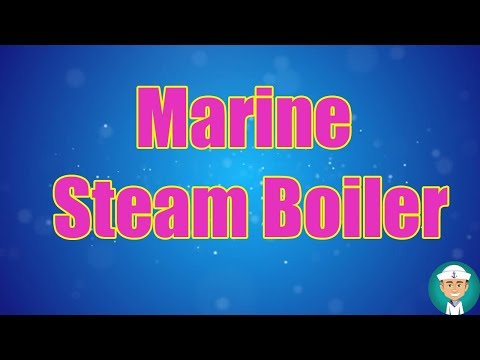
This course is designed to provide marine engineers and support staff with
an introduction to water treatment for steam boiler systems it begins with an
introduction to steam boilers and basic water chemistry the course goes on to
look at the problems caused by corrosion and scaling and the water treatment
solutions that are available the course examines the importance of correct
chemical dosing and control and the procedures for safe sampling and testing
there is a section on monitoring water test results and a look at the tools and
service that are available at the end of the course there is a troubleshooting
guide
a steam boiler is a piece of equipment into which water can be fed the water is
heated under pressure and is continuously evaporated into steam steam
is an excellent medium for the supply of heat and can easily be piped to the
required point of use click on the question marks for some examples of
typical uses for steam shell and tube boilers can be found on ships and are so
called because the water is described as being on the shell side of the
construction heat is provided by a burner firing inside a large diameter
furnace tube a series of smaller diameter tube banks above the main
furnace tube provides secondary heat recovery because of the large diameter
of the furnace tube the maximum pressure limit of operation of Shell boilers is
around 20 bar vertical water-tube boilers are the most common type of
boiler found on marine vessels they're almost exclusively used in the marine
industry because of their compact construction and ease of operation let
us look at the principle of operation the vertical water tube boiler has a
cylindrical shell and contains a hemispherical or cylindrical furnace
chamber at its base the burner is fired into this space and the hot gas is
produced pass around a series of tubes containing boiler water and exhaust
through an internal flue to the stack here the water is on the tube side of
the construction to compensate for the short retention time of hot combustion
gases water tubes can be fitted horizontally vertically or obliquely
cross tubes in the furnace section to maximize heat transfer inside a water
tube boiler the water circulation is controlled by having a series of
non-heated downcomers connecting the upper steam water chamber
to the lower ring shaped bottom header the water in the downcomers is cooler
and denser than in the hot Rises and this causes a natural circulation of the
boiler water the maximum operating pressure can be in the order of a tea
bar but is typically 10 to 30 bar the pipework inside water-tube boilers
is configured to extract as much heat from the furnace area as possible common
pipework configurations attempt o d and a type boilers in a typical steam boiler
system feed water is pumped into the boiler and heat is applied from a burner
system temperature and pressures increase according to the boiler design
valve arrangements are used to allow steam to flow in a controlled manner
from the headspace above the water level steam flows to the point of use and
cools and condenses back to water condensate water is typically recovered
and recycled as boiler feedwater once the ship is underway it is usual
practice to utilize the heat rejected from the main engine exhaust gas to
generate steam this means that the boilers do not need to burn valuable
fuel oil whilst at sea steam is raised by circulating water in a large non
fired heat exchanger these types of boilers are referred to as exhaust gas
boilers the fired and non fired boiler systems are usually interconnected in
general water is never pure normal tap water contains a number of constituents
that are important and beneficial to our Constitution the table shows that sea
water has a predominance of sodium chloride with significant amounts of
calcium and magnesium salts when introduced to marine steam boilers or
engine cooling systems these constituents will cause operational
problems if not removed for example dissolved gases such as oxygen and
carbon dioxide will cause corrosion and dissolved salts such as calcium
carbonate will lead to scale deposition as we will see corrosion and scaling are
serious problems if not controlled corrosion is an electrochemical process
where metal in contact with an electrolyte water is oxidized to
corrosion products local differences in chemistry metallurgy and oxygen
concentrations will induce potential differences on the metal surface and a
cathode and anode is formed at the anode will take place and metal will be lost
characteristic deposits of iron oxide rust are also formed broadly speaking
corrosion can be divided into two types uniform corrosion and pitting corrosion
click on the pictures for more information
oxygen chloride salts and pH all contribute to corrosion corrosion in
steam condensate systems can be particularly aggressive due to partially
wet and hot conditions carbon dioxide and oxygen in the boiler feedwater
flashover with steam and rhe dissolve in the condensate water the condensate
water is very pure and has no buffering capacity so relatively small amounts of
carbon dioxide will make the condensate water very acidic aggressive corrosion
will rapidly deteriorate metal surfaces and lead to pipe work failure and leaks
specialized treatments have to be applied to inhibit condensate line
corrosion scale deposits are formed when impurities such as calcium carbonate are
allowed to enter the boiler due to the negative solubility properties that is
decreasing solubility with increasing temperature of these salts deposition of
scale is favored on hot surfaces scale deposits form hard and tenacious layers
inside the boiler tubes such deposits will reduce heat transfer efficiency
cause overheating and potential tube failure to address the problems of
scaling and corrosion a range of water treatment chemical technologies have
been developed these are applied to adjust the properties of the feed boiler
and condensate waters and provide protection of the system methyl work a
typical boiler treatment program consists of a combination of chemicals
in open boiler systems it is usual practice to raise the temperature of the
feed water to minimize the level of oxygen present oxygen scavengers are
then applied to further reduce the oxygen to sub ppm levels for best
corrosion protection there are various types of oxygen scavenger available to
carry out this task and selection of the best approach is a function of the
mount of oxygen present feed system design economics and any particular
limitations required by the process using the steam some oxygen scavengers
such as D ha hydrazine and carbohydrate promote a protective iron oxide film
called magnetite that further enhances corrosion protection steel surfaces are
best protected in an alkaline environment alkalinity builders are used
to increase pH and alkalinity to the desired levels for best corrosion
protection alkalinity builders also help with scale control in alkali phosphate
treatment programs the alkalinity of the water also acts as a buffer a property
that will absorb pH changes if acid components are introduced and maintain
an alkaline pH in alkali phosphate treatment programs soluble phosphate is
incorporated into the treatment program to precipitate any trace hardness salts
passing into the boiler and disperse the salts before they can deposit on the
heat transfer surfaces scale dispersants are also used to ensure that any
precipitated scale salts are maintained free flowing in the boiler water
precipitated salts are then removed by routine blowdown this treatment approach
relies on good quality pretreatment usually see water evaporators elevated
pH and free caustic alkalinity helped the mechanism of precipitation carbon
dioxide is present in most waters and in the boiler system it will evaporate and
follow the steam into the condensate system when condensation occurs the
carbon dioxide will read azov' and lead to a low pH which consequently causes
corrosion neutralizing a means of volatile alkaline materials that flash
over with the steam they combined with the condensate water to elevate pH and
provide corrosion protection many Marines steam boiler systems operate at
low pressure and run at a steady-state this allows for the application and
control of multifunctional treatment products and for small and moderate
sized boilers this is the most common treatment approach typical
multifunctional treatments are shown here
a complete boiler treatment program can be furnished by two or three products
whether is variable steam load variable feed water temperature and with high
pressure boilers control of the selected water treatment program is best obtained
by dosing product types separately it is best practice to install chemical dosing
and control systems for steam boilers click on the question marks to see the
benefits of such a system this chart describes how good control of water
treatment applications can optimize cost and improve system protection water
sampling and testing is used to control the performance of water treatment
programs most treatment chemicals have a set of control parameters that should be
maintained for optimum system protection correct sampling frequency and
procedures are important to achieve inconsistent results system control
parameters should be in line with BS 1170 1983 treatment of water for marine
boilers consult your water treatment technical manual for further guidance it
is important that test results are recorded both for quality purposes and
to help with the interpretation of trends this enables corrective decisions
to be made quickly and effectively water testing is an essential shipboard
activity that should be performed on a regular basis water proof is a software
package developed to enable the crew onboard the vessels to electronically
record store and display results from water tests when entering the test
results the user immediately gets notified if the results are within the
set limits or if corrective actions are needed the test results can be sent to
Williamson ship service for review this is done via the internet or email a
report from our water treatment experts will be returned within days after the
defined test period is closed
-------------------------------------------
Henderson to start, Mane keeps his spot Predicted 4-3-3 Liverpool XI to face Leicester City - Duration: 2:12.
Liverpool will face a tough test as they
take on Leicester City at King Power
Stadium this weekend THG red should be
glad about not facing Jamie Vardy who is
unavailable for this clash however the
Foxes will not be easy prey at their own
turf dr vinkle ops minh defeated the
foxes 3-2 in the corresponding fixture
last season and there aren't many injury
concerns for the Merseyside club dot
three wins on the spin should not see a
lot of tinkering in the team but we
predict there could be one small change
in the lineup to face Laster predicted
Liverpool's eye formation 4-3-3 manager
Jurgen Klopp Alison Becker after three
clean sheets in as many games it would
be difficult to drop a listen the
brazillian has been great between the
six but he must cut out the tricks and
flicks with the ball Trent Alexander
Arnold's another player that has started
to see Andy Robertson Robertson is
another player that it's done well right
from the first game and his marauding
runs will be important while breaking
Lester's defense
Jordan Henderson the one change we
alluded to at the start Henderson looked
great in his cameo against Brighton
meaning we could see him start in place
of James Milner Virginia which now them
the Dutchman has been our best performer
in the midfield and should not be
dropped from the team Navy kirakira has
shown his ability in bits and pieces
over the three games the guinea
midfielder wasn't that his best against
Brighton & Hove Albion but he could do a
lot of damage to the Foxes on Saturday
sadiel main the former Southampton Man
had a poor outing against Brighton but
he must add to his tally of three League
goals on Saturday
-------------------------------------------
Advanced English Pronunciation Practice - Quick Easy Pronunciation Tips - Duration: 15:16.
Advanced English Pronunciation Practice - Quick Easy Pronunciation Tips
-------------------------------------------
William H. Macy Says Emmy Rossum 'Made the Right Choice' Leaving Shameless - Duration: 4:17.
William H. Macy is proud of his TV daughter Emmy Rossum. A day after Rossum announced her exit from Shameless after 9 seasons, the 68-year-old actor opened up about her decision to leave
"We've been expecting it," Macy said during an interview with Entertainment Weekly Friday
"I tell you, when you get to season 9 and you think of [whether] to keep going, it's daunting
" "It's hard not to think of: 'What would my life be post-Shameless?' And part of it is very frightening and part of it is very exciting," Macy told the outlet
"She's young and I think she's made the right choice. She's got another show that she's an executive producer on, so she's going right into something and she wants to branch out
Plus, she just got married," Macy said in reference to Emmy's husband, Sam Esmail
"I wish her well," Macy told EW. "I can't wait to see what she's going to do next
" Rossum, 31, announced her departure on Facebook Thursday. "See, in real life, unlike Fiona, I'm an only child
I never had a big family. Being ensconced in that messy Gallagher family love is something I'd always dreamed of
But even off set, it feels real. We've watched the kids grow up into the strong, talented, independent human beings that they are," Rossum wrote
"The opportunity to play Fiona has been a gift. There are few characters— female or otherwise— as layered and dynamic
She is a mother lion, fierce, flawed and sexually liberated. She is injured, vulnerable, but will never give up
" "She is living in an economic depression, but refuses to be depressed. She is resourceful
She is loyal. She is brave. I knew it the second I read the pilot script, this was different, this was special," Rossum continued
"I know you will continue on without me, for now," she concluded. "There is much more Gallagher story to be told
I will always be rooting for my family. Try not to think of me as gone, just think of me as moving down the block
" Her departure comes two years after she made headlines when she refused to sign on for the Showtime drama's eighth season unless she was offered more than Macy to make up for the seven years she was paid significantly less
Days later, the Golden Globe-nominated actress and Warner Bros. came to terms on a new contract
After Rossum posted her announcement, producers and executives released statements wishing her well
"Emmy Rossum will forever be part of the Shameless family. She has been integral to the show's success, from her wonderful portrayal of Fiona to her leadership role on set, as well as directing multiple episodes of the series
We are hard at work now creating a season nine finale for Shameless which we hope will provide a Gallagher-worthy sendoff for Fiona that honors the great work Emmy has done," executive producer and showrunner John Wells said
Season 9 of Shameless premiers Sept. 9 on Showtime.
No comments:
Post a Comment