Paris Saint-Germain star Kylian Mbappe was encouraged to join Arsenal by one of the London club's most famous fans on Thursday night
Mbappe, 24 hours after starring in PSG's 2-1 win over Liverpool, attended a Nike event in Utrecht alongside Dutch footballer Lieke Martens, boxer Zeina Nassar, tennis ace Elina Svitolina and four-time Olympic gold medallist Mo Farah
Long-distance runner Farah, who makes no secret of his love for the Gunners, grabbed a selfie with Mbappe and captioned it with a cheeky message on Instagram
MBAPPE THIS SEASON Ligue 1Starts: 7Sub appearances: 2Goals: 11Assists: 4Champions LeagueStarts: 5 Goals: 2Assists: 2 'Come to Arsenal bro', wrote Farah who tagged Mbappe in the post
Mbappe revealed earlier this year that he considered a move to Arsenal in 2017, before opting to leave Monaco for PSG instead
Speaking on French TV in June, he said: 'I met with Arsene Wenger, who is a great coach
He has a great reputation here in France, he's well-respected and knows how to develop young players
This was a real option for me.'We weighed up the advantages and disadvantages of all the clubs but my family told me it had to be my decision and one I needed to make
'It also had to be a long-term decision. So it was up to me and I decided to come here (PSG) in order to develop
'Since joining PSG, Mbappe has scored 24 goals and provided 12 assists in 36 Ligue 1 appearances
He has also hit the net six times in 13 Champions League matches and helped France to global glory by scoring four goals in their triumphant World Cup campaign at Russia 2018
For more infomation >> Mo Farah tells PSG star Kylian Mbappe: 'Come to Arsenal bro' - Duration: 2:38.
-------------------------------------------
Patrick Sébastien brisé par la mort de son fils, ce rituel immuable pour surmonter le drame - Duration: 1:17.
-------------------------------------------
SEÑALES DEL ESPACIO ¿QUIEN QUIERE CONTACTAR CON LA TIERRA? - Duration: 8:14.
-------------------------------------------
Regresión Lineal Simple - Teoría | #13 Curso Machine Learning con Python - Duration: 6:41.
-------------------------------------------
[Full] H'Hen Niê: "Showbiz đã thay đổi em" | BAR STORIES - Duration: 50:26.
-------------------------------------------
Ambassadors of Loro Parque Fundación - Duration: 1:04.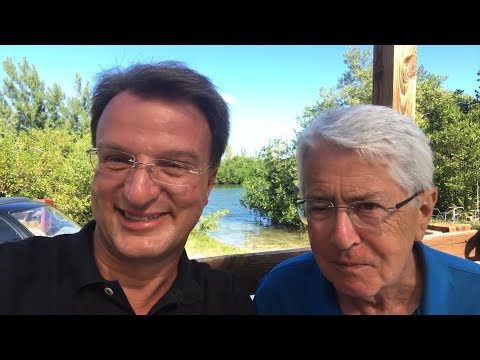
Hello, dear friends of Loro Parque Foundation, the two LPF ambassadors,
Frank Elstner and Mathias Reinschmidt, are reporting
from Bimini Island in the Bahamas, while making a trip with the goal of protecting the wildlife.
And this time it concerns...
Sharks! You can't imagine just how brave
Dr. Reinschmidt was yesterday. He even swam with a hammerhead shark!
I am not the only one who was brave, Frank Elstner is also brave,
we are committed to the protection of the species
and this is an especially important message that we are sending from the Bahamas:
we must commit ourselves to the protection of the seas and sharks
to guarantee a more promising future for them.
We hope that every single person that collaborates
with Loro Parque Foundation joins this cause and contributes to promoting this message.
Because what works best for the shark
it is also the best for all of us.
The protection of the species must always take the priority.
See you soon!
-------------------------------------------
Supplies Post Apocalyptic Hidden Messages Zombie illuminati - Duration: 16:26.
-------------------------------------------
Despedida de Tierra de artesanos. Huelva - Duration: 0:39.
-------------------------------------------
TA CHƯA TỪNG CỐ GẮNG | BLACK T x K-BOON | OFFICIAL MV - Duration: 4:02.
-------------------------------------------
La patada que le dará el agradecido Iglesias al señorito Echenique para que siga haciendo carrera - Duration: 2:40.
-------------------------------------------
@ Madrid Informa del 24 al 30 de noviembre - Duration: 1:53.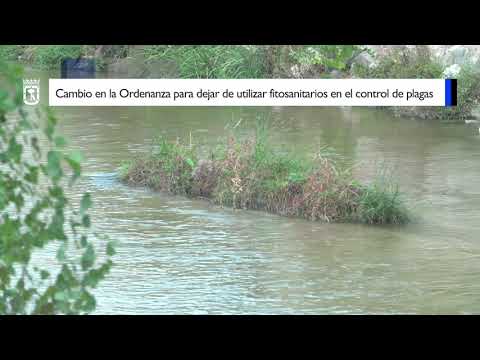
-------------------------------------------
Two images: If you tolerate this | Soy Cámara V.O.S.E. - Duration: 9:47.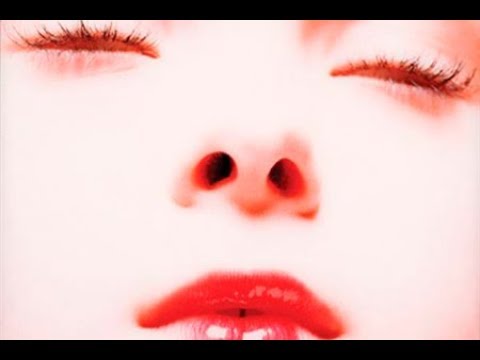
-------------------------------------------
Animaciones Fiestas Infantiles en Azuqueca de Henares 🐧 - Duration: 1:18.
-------------------------------------------
Yoga Videos For Beginners In Telugu | Yoga Videos For Beginners | Yoga Videos | Yoga In Telugu - Duration: 11:24.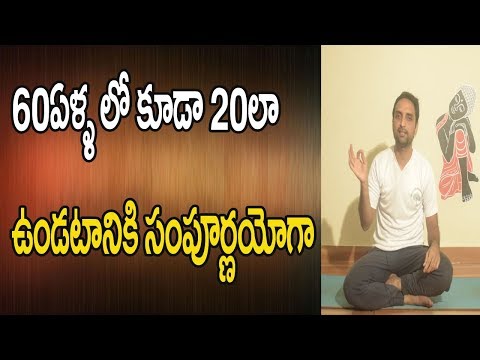
-------------------------------------------
Digipay Commision Chart List 2018 Not Official by CSC SPV - Duration: 1:41.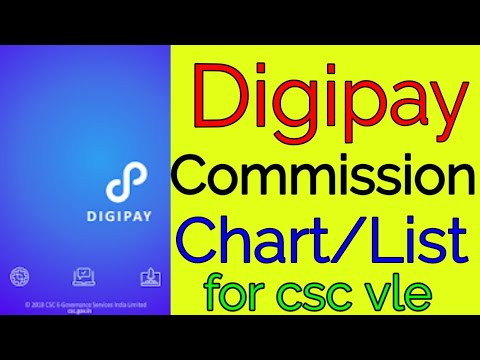
WWW.DIGITALHELPJAY.COM
-------------------------------------------
how to see live sub count of any channel. - Duration: 1:38.
First open Chrome browser
Search social blade
Click on the first site of social blade
Click on search tab and type any channel name like PewDiePie
Some icons will appear be sure and click on real channel
You will see channel analytics
Scroll down and see subscribers list
You will see live option in red colour click on it
Live sub count will start . See from here
You can do live stream now of sub count
If you like this video than please hit a like and don't forget to subscribe my channel
Search in search tab T-Series and do versus live stream !!
-------------------------------------------
झटपट नाश्ता रेसिपी - Besan Rava Toast Recipe In Marathi - Quick Breakfast Recipe - Archana - Duration: 3:09.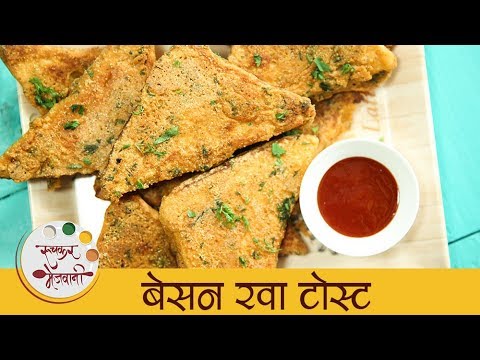
-------------------------------------------
How I Make My Thumbnail In Gacha Life + Shout Out - Duration: 8:33.
How I Make My Thumbnail In Gacha Life
-------------------------------------------
Volkswagen Transporter 2.0 Comfortline | 150pk | schuifdeur | achterdeuren | L1 H1 | - Duration: 0:52.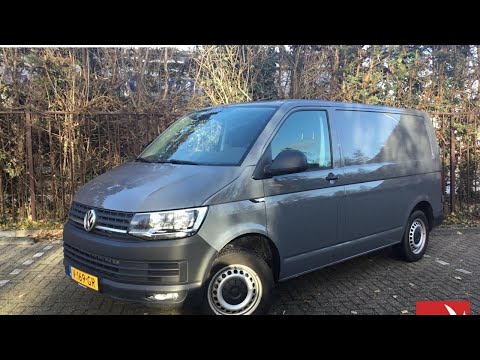
-------------------------------------------
Arsenal legend urges Unai Emery to perform stunning Man Utd and Barcelona transfer raid - Duration: 2:42.
That is the view of Arsenal invincible Lauren. With a high wage bill at the Emirates, funds are short for Emery to make major signings
But the Arsenal board will provide the Spaniard with money if the right opportunity arises
And the possibility of signing Martial and Dembele could give the Gunners serious momentum in the second half of the season
Martial has been excellent for Manchester United in recent weeks and his contract is set to end in the summer
United have the option of triggering the one-year extension on Martial's contract to prevent him leaving on free but from January 1 he can sign a pre-contract agreement with a foreign club
Meanwhile, Dembele has struggled with injury and consistency at Barcelona. Arsenal's chief scout Sven Mislintat brought Dembele to Borussia Dortmund in 2016 and would likely play a key role in recruiting him again
And Lauren believes Martial would be a guaranteed starter in the Arsenal XI. "If Martial doesn't renew his contract at Man Utd, Arsenal would be crazy not to try and snap him up," Lauren told Sporting Bet
"He's a fantastic player and is starting to show what he can really do when given a good run of games
"Martial won't go anywhere without being guaranteed first team football, which I think he would get at Arsenal
" Lauren then added that Dembele's style suits his former club perfectly. "Everything about his style of play matches what Arsenal are looking for," Lauren said
"He isn't getting the playing time at Barcelona, or playing in his strongest position, but Arsenal's high intensity will allow him to reach his potential
"Dembele can play on either side of the pitch, which is a bonus and he's showed that he can do it against the big teams, coming off the bench to rescue points for Barcelona
"I would love to see him at Arsenal."
-------------------------------------------
SOI 01 [BOY LOVE] SOI CẢNH TẮM CỦA HAI VỢ CHÔNG ĐỨC CHINH - TIẾN DŨNG [U23] - Duration: 2:32.
After Episode 1 is aired, maybe we are confused so much.
Why is Tien Dung present at Que Toi Village?
And Why is he doing prostitution? Why why????
Meanwhile, Duc Chinh got lost in the forest with Star Team.
And obviously, we're seeing Cong Phuong taking advantage of this opportunity to reach Duc Chinh
This time, maybe it make Dung's relationship become serious.
Don't worry, We have an answer for you that he had an accident and amnesia
So he has to seduce rich women to have money for his life.
And Diep Linh, where is she?
Chinh and Dung, what will be together?
And now, we will compare him and his wife while they are taking a shower.
Duc Chinh focuses on bathing, not singing
Scrubbing hahahaha, it looks like his legs are very masculine.
At the same bath time
Tien Dung loved life,
he just take a bath and sing but his voice is so bad
What is Episode 2 will be special with both?
Tien Dung vs Duc Chinh and another couple Dinh Trong vs Tin Dung.
See you on Tuesday at 19:00 every week.
-------------------------------------------
Op ontdekking met de Discovery - #8 - Duration: 1:02.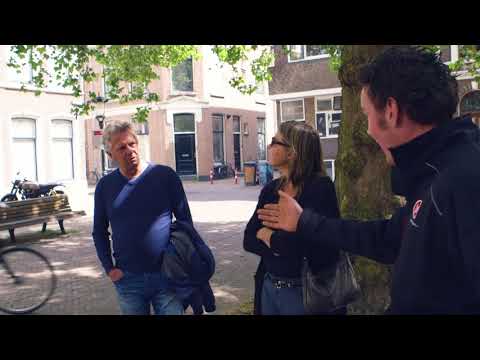
-------------------------------------------
Station Vlaardingen Oost Metro Hoekse Lijn 2018 - Duration: 1:41.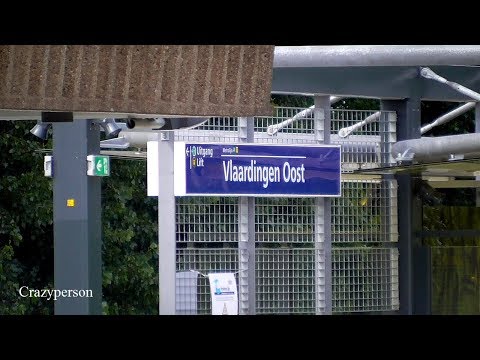
Vlaardingen Oost
-------------------------------------------
U&D: proposta di nozze e petali rossi per una coppia del pubblico | Wind Zuiden - Duration: 3:51.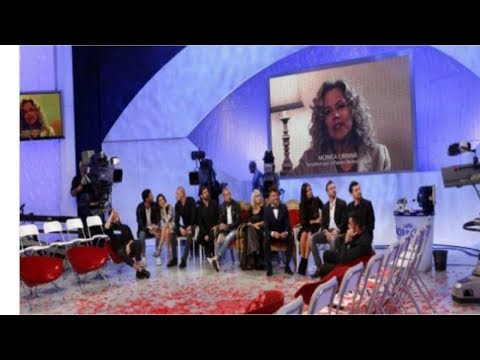
-------------------------------------------
TA CHƯA TỪNG CỐ GẮNG | BLACK T x K-BOON | OFFICIAL MV - Duration: 4:02.
-------------------------------------------
L'Isola dei famosi 2018, news su concorrenti e opinionisti: favorita Alba Parietti | Wind Zuiden - Duration: 3:38.
-------------------------------------------
À LA RADIO EN DIRECT CHEZ RCF ! Jeviensbosserchezvous© - Duration: 0:55.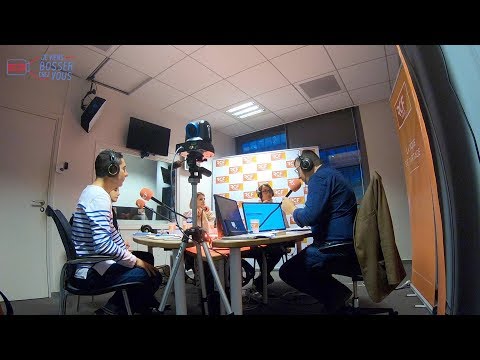
-------------------------------------------
Giulia De Lellis, la confessione: 'Io in politica? Perché no, potrei farcela' | Wind Zuiden - Duration: 3:53.
-------------------------------------------
Uomini e donne anticipazioni, i dubbi di Teresa su Andrea | Wind Zuiden - Duration: 4:28.
-------------------------------------------
BMW 3 Serie 320i EfficientDynamics Edition High Executive 1e eigenaar - Duration: 1:13.
-------------------------------------------
Animaciones Fiestas Infantiles en Azuqueca de Henares 🐧 - Duration: 1:18.
-------------------------------------------
Where I Hide My Tools - Duration: 9:47.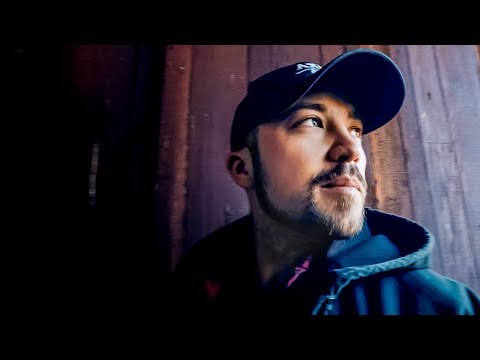
we've got some projects that we're working on today and one of them I don't
really know much about it so we got to go investigate but they said there are
there are three signs that need adjusting and so I don't know what that
means but I'll have to go check it out it's very cheap you can't come sorry I'm
gonna take the truck today follow us on Instagram if you don't communicate here
with radios so everybody that works here has a radio call each other and not have
to use your phone I don't have a cellphone that well I don't have a
cellphone that works right now although there's a new Timmy phone that is coming
in the mail here pretty soon and
even when it gets here it won't have cell service
some of you were gonna tell me I put my seatbelt on but I'm not leaving private
property and I'm not gonna be going faster than 10 miles an hour so I think
I'll be okay first thing we need to do is swing by the wood shop and I guess
there's a sign actually yeah go by the wood shop first
smells like somebody I was a fire going it smells really good I love the smell
of I'm looking for a sign somebody give me a sign I have no idea where it is
how many wanted to see this jig set up again for the belt sander so that's what
it looks like there you go there's all the plugs we made you guys have seen me
wear this flannel shirt a lot I mean I wear it a lot it's my favorite flannel
but I just noticed for the first time the other day look at this the tag the
logo for the company is the head of a dog which is really cool it looks like
it's a Labrador or some type of retriever I surprised it I've never
never noticed that all right I didn't find the sign but I need to go look at
all the locations but the signs need to be adjusted that way I'll have a good
idea of what tools I need to bring etc if you're new to the channel this is
inside of our truck and we have been traveling for last ten months across the
country visiting our friends and family kind of all of our main possessions are
in this truck right here so that's why there's a coat rack right there with our
stuff in the back seat you are new I'm happy you're here push the subscribe
button all in and click the bow so you get notified when we post new videos I
got stopped at the dog kennel real quick
left this little gasket in there the other day I thought it was too the the
hose that was in there but it actually goes on this gimbal the handle to the
gimbal that you're on right now has it comes off and so this little gasket
because this gimbal is supposed to be water resistant and this little gasket
goes on here all right we're off like a herd of
turtles
well this was a sign that was supposed to be in the woodshop this is our tree
course sign and I assume in either Ryan there's somebody picked it up and I took
care of it so I don't need to do that hopefully Jose you're not running me on
a wild goose chase right now go check out those other two signs
you said need to be adjusted if anything I'm I'm not mad that I'm out driving
around ok this sign looks like you need some adjusting this one's just on the
ground leaning against the posts I need my we were transporting some
firewood in here so all this stuff's from
this is a good thing I have my drill set with me only the only downside is I
don't get the drills out very much and so they're packed back here in the back
of the truck it's normally where we have Chiefs dog
bed here and he hangs out there but if you then under here just need to open it
you'll be able to get the drill out and fix these signs they do have a drill
back at the woodshop
how ha we did it like two out of three signs then no we didn't have to do
anything on the first one check out this last one it is chilly today it is a
habit though to put on my seatbelt I'm literally driving like a hundred
yards at five miles an hour so I think I'll be okay since there are
a lot of you watching you should always wear your seatbelt whenever you're
driving no matter what okay let's keep going
well there's the last sign and I'm not sure how it needs to be adjusted
maybe that right there this is broken a little bit this part of the sign looks
fine though the only thing I can see is this little piece of wood that's
flopping off all right so I got the top piece off
I spun that top cap around so it looks a little bit better maybe maybe that was
it he said small adjustments so yeah the office so I'm gonna run there and he is
gonna show me how we're gonna assemble the railing so we've been building this
railing and we're finally at the point where we're gonna start putting it
together so that way we can transport it up to
the building that it's gonna go on there's an example of what the railings
gonna look like along your sections and then this but you'll have the wood frame
and then the metal grates that we've been cutting and then you have these
ropes on the outside thing you'll look pretty good so right now this is where
everything is just kind of in staging and all the woods over here stayin ready
to go and then I put all the greats along this wall all the way down and
they're in different sections here there's two that are together and
they're the same length but this one here is a different length and so all of
these are different lengths and I got to figure out which posts go to each
section and then which boards go to each section as well so that'll be the next
step is starting to assemble all the railings and get them together in a fun
project it's cool I've never built a railing like this so I think it looks
really nice the hug panel I like this stain too it's a dark stain and it's the
same type of stain we've been using to stain the outside of these buildings
it's nice being a volunteer cuz we don't have like a strict schedule or anything
and we just are here helping out and we get a help with random projects as well
so we have about two weeks left being here hanging out working and my
brother's coming next week so I'm super excited for that and I'll try to share
that that time with you guys so that you get to see him a little bit some of you
guys who have been watching since we were back living on the ranch you saw
Jake in a lot of videos because I started this channel it was with the
intent of ax family being kind of just our whole family of Jake and I and and
our wives and and then as our families grew but then Taylor and I moved away
and so we're just continuing the channel and it'll be good to have Jake back in
the videos a little bit we'll see how much we can get him in here so we will
see in the next one hats off to you
-------------------------------------------
How I Make My Thumbnail In Gacha Life + Shout Out - Duration: 8:33.
How I Make My Thumbnail In Gacha Life
-------------------------------------------
Melanie - Find A Way [Official Music Video] - Duration: 5:07.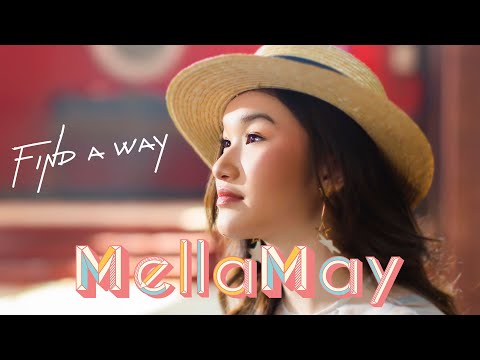
Coming close to crying, on the inside I'm dying
I'm gonna hide it with a smile,
okay?
Getting hard to fake it,
don't know how I'm gonna make it
Tired of answering the question "are you okay?"
Are your jokes funny now?
Wanna take a bow?
Cos you've won your prize
Is this it? I'm getting sick of this
Not a surprise
Now I see, I see reality
Cos real eyes realise real lies
Is it me? Am I going crazy?
I keep on running but can't hide
Find the sense of right and wrong
Hold your head up and carry on
Change the voices in your head
Make them like you instead
Losing all my patience
Little girl please be patient
We're gonna find a way out,
okay
I know you're tired of crying
But you gotta keep on trying
Cos one day you'll be okay
Are your jokes funny now?
Wanna take a bow?
Cos you've won your prize
Is this it? I'm getting sick of this
Not a surprise
Now I see, I see reality
Cos real eyes realise real lies
Is it me? Am I going crazy?
I keep on running but can't hide
Find the sense of right and wrong
Hold your head up and carry on
Change the voices in your head
Make them like you instead
(Find a way)
Now I see, I see reality
Cos real eyes realise real lies
Is it me? Am I going crazy?
I keep on running but can't hide
Now I see, I see reality
Cos real eyes realise real eyes
Is it me? Am I going crazy?
I keep on running but can't hide
Find the sense of right and wrong
Hold your head up and carry on
Change the voices in your head
Make them like you instead
(Find a way)
-------------------------------------------
W Kuchennych Rewolucjach pierwszy taki skandal! "Syf i malaria" - Duration: 5:50.
„Kuchenne Rewolucje" to jeden z tych programów, które w każdym epizodzie przełamują kolejne bariery
Magda Gessler jak nikt inny potrafi wywołać w telewidzach zupełnie skrajne emocje
Jeśli komuś wydawało się, że tym razem będzie inaczej, to prawdopodobnie żył on w największym błędzie, od kiedy sięga pamięcią
„Kuchenne Rewolucje" docierają do coraz to nowszych lokali gastronomicznych na terenie naszego kraju, gdzie wywracają zastaną koncepcję prowadzenia knajpy do góry nogami
Najczęściej wiąże się to ze łzami i zgrzytaniem zębami. Tym razem Magda Gessler zawitała ze swoją ekipą do restauracji „Masala Twist" w Toruniu
Takiej zadymy w programie nie pamiętają nawet najbardziej wytrwali widzowie. Kontrowersyjny uczestnik show TVN ujawnił kulisy produkcji! Szokujące wyznanie „Kuchenne Rewolucje": Magda Gessler nie uwierzyła własnym oczom Restauracja prowadzona jest przez rdzennych Nepalczyków, którzy współpracują ze sobą już od paru lat
Magda Gessler już od samego wejścia do lokalu wiedziała, że ta rewolucja nie będzie należała do najłatwiejszych
– Uuu, pachnie Wschodem. Gorąco jest okropnie. Jak możecie pracować w takim upale? Okno się nie otwiera? – zaczęła komentować
Po ulokowaniu się przy stole, restauratorka przeżyła kolejny szok, kiedy została jej podana karta dań
Menu zdecydowanie nie należało do najbardziej czytelnych pozycji, jakie można sobie wyobrazić
– Nie wiem, jak w takiej małej knajpie można serwować tyle dać. Karta jest jak książka telefoniczna – stwierdziła
Po chwili zastanowienia gwiazda złożyła niemałe zamówienie. Obejmowało ono zupę tajską z krewetkami, samosę, herbatę indyjską, sos miętowy z chlebem papadam, pad thai oraz kurczaka tikka masala
Dyplomatycznie mówiąc, Gesssler nie była zachwycona smakami potraw. – Jeszcze tak słodkiego pad thaia nie jadłam, jak deser
Chicken tikka masala to sam barwnik. Dlaczego dodajecie barwnika do sosu pomidorowego? Ten kolor to jest po prostu skandal – powiedziała przy okazji jednego z dań
DALSZA CZĘŚĆ TEKSTU POD GALERIĄ Jednak największy szok spotkał ją po wejściu do kuchni
Mało rzeczy jest w stanie wprowadzić Magdę Gessler w osłupienie, ale to co ujrzała, trudno było wytłumaczyć w jakikolwiek sposób
– To miejsce czystością nie grzeszy. Tu jest syf i malaria. To jest tak gruby tłuszcz, tego się nie da nawet pokazać
To nożem trzeba oskrobać. To jest tragedia. Koloranty do wyrzucenia w d*pę jeża. Żaden smar nie śmierdzi tak jak ten ryż – skomentowała
Rozgorączkowana restauratorka powróciła do lokalu na drugi dzień i wydała bardzo stanowczą opinię
– To miejsce kwalifikuje się do tego, żeby je zamknąć – ucięła wszelkie debaty. Dopiero tak mocny impuls poskutkował na pracowników knajpy, którzy w końcu wzięli się w garść
Dopiero na tzw. ostatniej prostej udało się przeprowadzić rewolucję w toruńskim „Masala Twist"
ZOBACZ TAKŻE Zobacz również
-------------------------------------------
Overnight closure, work begins on south I-25 Gap - Duration: 3:05.
-------------------------------------------
Yep, it really is a DMR... - Rainbow Six Siege - Duration: 8:50.
What's up guys, Rogue-9 here and I have pushed on with my analysis of the new guns
coming to Rainbow Six Siege with Operation Wind Bastion.
Today, we dive into the hidden stats behind the defender Kaid's weapons; so strap in
tight, this is going to get interesting!
Kaid of course brings two different main weapons to the table: the AUG A3 9mm SMG and TCSG12
semi-auto shotgun.
Both of these guns handle quite differently, so ultimately the question of which is the
better choice will come down to which one suits the map, current objective and your personal playstyle.
My analysis in this video will be as concentrated as I can make it, so do feel free to follow
up for yourself in more detail with my online spreadsheet (link in the description).
Let's start out by taking a closer look at the AUG.
This SMG, much like Nomad's AK-74, has below average damage per shot (both before and after
drop-off) and a significantly below average fire rate.
This unfortunate combination gives the AUG the lowest damage per second output (at close
range) out of all of the SMGs in Rainbow Six and also the slowest Time to Down or Kill
against all three armour types.
Yes, fair enough, we are talking about tens of milliseconds here but the fact remains
that this gun is even more of a pea shooter than Valkyrie's MPX or the GIGN's P90.
The capacity of 31+1 is ok I guess but the reload times are again significantly below
average compared to the rest of the SMGs.
In fact, the reload time from empty is exactly the same as the average assault rifle reload
and the tactical is even 100ms slower than the rifle average.
And that's not the only parallel between the AUG SMG and the assault rifles.
All SMGs in the game have an ADS time of 300ms which gives them a bit of an advantage against
the slower rifles when unexpectedly coming face to face with an opponent.
Kaid's AUG though, for some strange reason, once again shares the same stats as the rifles
and takes 450ms to aim down sights.
And last but not least, at least there is one good thing about this weapon and that's the recoil.
Even the baseline recoil is highly manageable and once you attach the vertical grip and
muzzle brake, it basically becomes a laser.
In fact the recoil is so mild, that I would even suggest that you ignore the vertical
grip and go for the angled grip instead.
That way, at least you reduce the ADS time to 270ms which then brings the gun more in
line with the rest of the SMGs.
In conclusion, the AUG is possibly the weakest defender primary in the game in terms of damage
output and in addition to that, it has the slower reload and ADS times of the attacker primaries.
This gun is clearly designed to be weak in order to compensate for Kaid's useful gadget.
To me, that gives him a role similar to Valkyrie.
The gadget is a great benefit to the entire team but the individual player picking these
characters will have to put up with lowered fragging capability for the entire round.
But that of course is only a third of the story with Kaid; we still have the option
to rely more on his primary shotgun or outrageous .44 mag sniper pistol.
The TCSG12… urgh again with these weird long acronyms that nobody even knows the meaning of?!
This is literally the BOSG.12.2 all over again…
Anyway, as I was saying: the Tactical Clutch Shotgun 12 is, as we know, a 10+1 shot semi-auto
slug shotty that can (for now) attach an ACOG, which let's face it, makes this gun into
more of a DMR with breaching capabilities than anything else.
One headshot or two body shots against any type of armour at distances of up to 19m as
well as the standard semi-auto fire rate is exactly the same (or better) than any of the
DMRs, the only difference here is the very unique damage drop-off curve of the Totally
Cool Super Gun 12.
Up to 19m, the gun will do the full 84 points of damage and at 21m the drop-off already
bottoms out at the minimum 40 points, so it's only in between where we see the transition.
This makes the gun's performance very bipolar: up to 19m, it's a guaranteed 2 shot to kill
weapon but from 21m onwards, it's always 4 shots to the upper body.
This does give the actual DMRs a long range advantage but this is Siege after all, where
the average kill distance is consistently below 10m from season to season, so you're
probably not even going to notice this disadvantage all that much unless you are going for some
particularly long range spawn peeks.
Reload times of the Tenaciously Cool Slug Gun 12 are 100% in line with the semi-auto
shotguns and significantly better than those of the other DMRs and this is also true for
the 300ms ADS time.
Recoil is harsh-ish, even with the vertical grip attached, but at least for PC players,
it is definitely something you can learn to handle with some experience.
For console players, the recoil may make the gun a little less viable.
But after all that, statistically this gun is pretty damn good in terms of its combat
capabilities but of course, it is still a shotgun and therefore comes with a whole bunch
of breaching benefits.
Basically, the TCSG functions just like Vigil and Dokkaebi's BOSG but this functionality
has been tweaked slightly on the Test Server compared to the live build.
In the current live build, Vigil and Dokkaebi can open hatches and shoot the studs out from
in between walls but it takes several shots to create an impulse in a soft wall.
On the test servers, as long as you are within 7m distance from a soft wall, each individual
shot will cause an instant impulse.
This makes the slug shotguns much better as breaching tools although the two shot capacity
of the BOSG is still a hugely limiting factor.
But of course the Top Capacity Shotgun 12 does not have this issue and so it can be
a pretty decent breaching tool.
It will never be as useful for breaching walls as other shotguns with their 8 pellets of
buckshot but it can get the job done.
When it comes to hatches, the slug shotguns can be pretty inconsistent.
If you just start randomly shooting holes into a hatch, it could take anywhere up to
eight shots or even more before the hatch gives way.
But if you create a shallow angle of attack and make sure to take out as many of the studs
as possible, you can open an undamaged hatch in a single shot.
It all depends on how much material the slug will travel through.
And that's pretty much all of the highlights you need to know about the TCSG and AUG; and
with all of this info in mind, I think the conclusion is quite clear.
Operation Wind Bastion brings with it two hybrid weapons that combine the best features
of two different Rainbow Six Siege weapon classes.
The TCSG has the breaching capabilities, ADS time and reload time of a semi-auto shotgun
but with the damage and combat capabilities that can rival and even outplay the DMRs.
The same goes for the .44 Mag Semi-Auto pistol: combat capabilities of the DMRs but with many
of the strong advantages of the pistol class.
Sadly, for the AUG A3, the exact opposite is the case.
This is one of the weakest possible SMGs with the added negative aspect of sharing the ADS
time and reload time with the attacker rifles.
Two of Kaid's guns take the best of two classes while one comes with the worst of two.
Does that mean that the TCSG is always going to be the better choice?
Not necessarily.
If you are playing on a map and site that will most likely end up in very close quartered
engagements, the controllability and full-auto capability of the AUG might still make it
the better choice for some players, but all in all, your choice will be between a poor
SMG and a very powerful DMR/Shotgun hybrid.
And then of course, there is still the .44 mag pistol.
If you want a detailed breakdown of this outrageous pocket sniper: feel free to check out my video
on Nomad's guns, where I go into significant detail about the strengths and weaknesses….
No wait, scratch that, there are no weaknesses… sooo, where I go into detail about the strengths
of this ridiculous firearm.
If you're interested in that video, click the upcoming link in the end card and with
that, many thanks for watching, I hope you enjoyed the video and I will see you in the next episode!
-------------------------------------------
Update: Eating Disorder & How things are going - Duration: 10:35.
If you keep listening to that I really believe that life can be better for all of you as well, and you have to keep believing in that as well.
And that was my motivational talk for now.
Go do the things you love and you'll find out you don't want an eating disorder anymore!
Hi everyone! Today I have a new video with an update, about how things are going at the moment!
I do think it's a bit weird to announce it like that.. that this video will be about that.
But I do have to say that there are lots of people, especially on Instagram, are asking for it.
Because they have the same problem themselves..
There was even a girl who wrote me a super long and sweet email.. So that's why I'm 'just' doing it..
If your first thought is: "Don't be such a wuss about that, why would you put that on YouTube"
Than you shouldn't watch this video, because that is were this video is about!
So this video is about my eating disorder.. I made two videos about it before, than I went to Australia and never said anything about it anymore.
So I do get why you guys are asking how I'm doing now.
Well, first of all, the fact that I went to Australia, that that was possible, does say a lot!
If I still would've been sick.. Physically and in my head as well.. I wouldn't be allowed to go to Australia at all.
And even if there would've been people who would've thought I wouldn't be able to cope, than they wouldn't have let me go.
So that's a positive thing itself.
I do have to say, that when I went to Australia I was still thinking about what I could and couldn't eat all the time.
Actually the moment I left, I was still following my meal plan.. In my head especially.
It probably wasn't obvious for the people around me..
But in my head I still had that list with what I could eat..
And I couldn't go over that because it would 'make me gain weight'.
So especially in the first weeks in Australia that was pretty hard..
Because you suddenly have to leave your 'save world', and you have to adjust to a new country..
To other food, eating habits, all these kind of things.
So in the beginning that was hard.. And on top of that nobody knew about my eating disorder.
So I couldn't talk about it with anyone when I was there and no one was aware of it..
It was a conscious choice of mine.. because I didn't want people to treat me different any longer.
So i didn't say anything about it on purpose but sometimes I still thought: "Little do you know..!"
Generally thing were going much better otherwise I wouldn't be able to go there..
And while I was there things were going great!
I could really enjoy things there and I was so happy!
I could also ignore the bad thoughts way better there.. and when I did have a bad thought I would just think:
"Maureen, u feel this way now.. Shit and fat.. Or you feel like losing weight.."
"But you're on the other side of the world.. You're doing the thing you wanted.. Than why would you worry about this..
When you can see how many nice things there are, which things you are capable of doing..
When you're going to lose weight again, you can't do this anymore.
So I could really put things in perspective there; that losing weight wasn't going to help me.
That it would only make things worse again and that I would become more unhappy than.
So that was really nice! But of course I had to go back home again after some time..
And I was so scared I would get stuck in my eating disorder again..
Because it all started here in this house.. At home everything was save and I could do everything the way I wanted it.. All these kind of things.
So I was quite scared for that.. But actually it turned out better than I thought it would.
It's still going well actually, even though I find that hard to say..
Because I tried filming this video before. And a few weeks ago I sat crying in front of the camera..
Because I felt so bad and I wanted to film this video.
Afterwards, I'm not going to put that video online.. Not because I'm ashamed of it.. because I know these bad moments are still there..
But because I want to be clear and I want to be able to explain it the right way.
And at that moment I wasn't feeling well and comfortable in my skin.. so I couldn't talk positive about how things were going.
So that's why I'm filming it again right now.
So in general it's going really well! But I still have a lot of moments were I fall back in the negative thinking.
And there are a few other eating disordered things I 'relapsed' in.
I still feel bad saying that.. Because I really hoped everything would have stayed the same as in Australia.
But there still are a few things that are 'shit' or not going well..
But I did learn how to cope with that.. And that is going way better already!
And I can ignore it a bit more now
I feel myself being 'too much' at the moment as well.. I'm alright but I just feel big, heavy, too much, too present.
And at the same time I feel like I'm not good enough and that I'm not doing enough..
And those two sides really compete against each other..
And than I feel bad.. but I am better at getting over it now than I used to be..
Because when I used to feel fat I knew what I had to do.. Lose weight. So I stopped eating.
DON'T DO THAT. That's not good and not the right way.
But now I have that feeling, I feel those feelings, I think about it A LOT. I feel bad about it..
But I try everthing to get myself back together now and I go on.
So I think that's the healthy part of my mind which I do have now! ;')
Which does let me feel: "That's not the right way to deal with it.. It's better to go on.."
"And than everything will be alright and the negative feeling will leave."
And when I feel really bad I sometimes do tell my boyfriend..
Or when I feel really fat I tell my sister or one of my friends..
I do have a few friends who now how it feels really well.. Because they've had the same.. Or because they have known me from 'the beginning'.
So that's really nice.. And that way I'm not alone with my feelings.. And I can still share it, even thought you can't see that I'm not doing well at the outside anymore..
It's not like people can still tell I'm not doing well now because I lost weight or something..
And that's something I found really difficult in the beginning.. Because people don't ask how you're doing anymore..
But because I do have these people around me now, were I can talk about these feelings with.
Does make it easier to keep going as well.
And even though these feelings are still there.. Feeling fat, being insecure about how I look..
If I'm still good enough or do good enough..
And even the exercising sometimes.. that I still do that with eating disordered thoughts.
That doesn't mean I'm not doing well right away.
Because I didn't get these things in year.. it lasted years that things went a bit more downhill everyday.
And I think because of that, it can take years for it to go all away as well. I think you just have to give it time.
That sounds so cliché.. I sound like a gradmother saying that. But I do think it's true! :')
And besides that I don't think everything is bad or shit.. Because there are many things going way better as well!
Because even though I feel fat now, I can go out for dinner or something spontaneous now
Or eat something 'unhealthy', I do have rules about it inside my head but I'm better at just thinking:
"Are you really going to let these thoughts ruin your time with this person.. or are you just going to live again?"
I don't know why that just made me feel so.. emotional.
It's going way better! It's just annoying that some things, inside my head, are still difficult.
And that that can still make me feel so bad, I think that's what makes me emotional.
And like I just said; That I just want to live, be happy and enjoy things. And that these feelings still get in the way sometimes.
I've never been depressed.. but I did have depressive periods. Which is something different!
I would never just say that I've been depressed. But the negative thinking, the depressive periods.. If that's what you want to call it; it's what they said in therapy.
The fact that that's still there.. is just a bit shit because..
I just hoped that it would have stayed away.. or would have been gone sooner.
BUT, things are going WAY better!
And I especially want to share that because when things are not going great with you, things can get way better for you as well!
And you really have to keep believing in that!
Because I always thought people were lying as well.. I thought that my head/brain must been different..
But that's really not the case. Everyone can get better and even get rid of it.. I still believe in that as well.
That's hard.. and sometimes it will feel like it's not possible and you can't do it. But you really can!
Do what your surroundings say what's right, what your therapist says, what your doctor says
What your healthy mind tells you what's good. Because you always have a bit of that left, I hope ;)!
And if you keep listening to that I really believe in the fact that it can get better for all of you as well!
And you have to keep believing in that yourself as well! And that was my motivational talk for now!
I think you all get what I mean.
Go do the things you love and you'll find out you don't want an eating disorder anymore!
Or whatever mental illness or something different you have..
Go do the things you love and you will find out you that you want to do fun things in live
and that you don't want to sit at home in your room and feel bad and all these things..
I hope gave the answer to your questions.. That it was a bit clear.
I'm doing good it's going way better and I'm really happy with that.
And these few things that are not going great or the moments that I'm not doing great. I will survive that!
And at some point that will go away.
And I really want you all to keep going for that as well!
If you have any questions, please leave them in the comments!
If you don't want to ask it on YouTube you can send me an Instagram DM as well, or an e-mail.
It doesn't matter at all, I really want to help whenever is possible! So if you have any questions, just ask!
Thank you all for watching and I'll see you in my next video! Bye! ♥
-------------------------------------------
A WEEK IN MY LIFE | FUMIYA VLOG - Duration: 13:38.
Today, I'm here at Philippines restaurant in Japan.
Wow! There are stage!
Mr.Fujita!
There are many Filipino food!
I don't know the name of this food!
I'm gonna eat Sinigang and...
What's this?😂
I don't know this food😂
Sinigang is good!
Lately I've started to like Sinigang.
Masarap!
Good!
My hair has grown!
Since I'm always having the same hairstyle,
I wanted to have a change of image!
I haven't decided of what hairstyle I'm gonna have, but I want to change my image!
Today, I'm gonna try freestyle basketball
I got this ball from my friend!
Let's play!
Please show us your basketball skill!
Kenta: Wait!!
We're taking a break now.
And we are gonna eat Takoyaki!
Japanese street food
Wow! Amazing!
What's inside the egg?
It's only egg😂
Your reaction is so fast😂
I'm gonna eat this!
It's so Delicious!!!!
I got some package!
Kpop artists have their hair until the nape of the neck, and it's getting popular in Japan too,
so I would like to do that today.
I want to have other hairstyles too!
I want to dye my hair too!
Anyway, I bought this snack!
I'm craving for a chocolate egg!
I don't know why
Chocolate egg is so delicious ,right?
I really like this
I found The Incredibles!
I like Disney movie!
I've watched The Incredibles many times
It's so interesting!
And recently I watched Incredibles 2!
It was nice!
My favorite character is Dash
I like Dash!
He is a fast runner.
Let's eat!
This brings back memories!
This is seldom sold in Japan
I only wanted this toy when i was child
But now I want to eat this chocolate
Good!
This chocolate tastes like from other country.
I like this chocolate,
because it tastes like my favorite ice cream Magnum
I used to drop my ice cream and got scold by my parents!
I like this chocolate!
I'm gonna open it!
It's not Dash!
What's this?
I really don't know how to use😂
This character is Jack-Jack
Oishi!(Good)
I got some package today!
It's like an electronic cigarette
This does not harm the body!
It doesn't contain nicotine and tar.
This contains vitamins!
I'm not sure if this is really good for the body,
but it's better than cigarette for sure!
I'm not sure, but I bought this!
I actually used to smoke before,
but then I got a lung pneumonia and had a hole in my lungs!
Had an operation.
After that, I quit smoking.
But i wanted to try this! so bought this!
This is Mint flavor!
I might start to like this!
-------------------------------------------
与丈夫离婚后的你还能再遇到真爱吗? - Duration: 7:21.
-------------------------------------------
塔罗占卜:你心中的TA对你的印象是什么样的? - Duration: 7:33.
-------------------------------------------
DIY How to make candle holder out of pine cone (ENG Subtitles) - Speed up #546 - Duration: 1:34.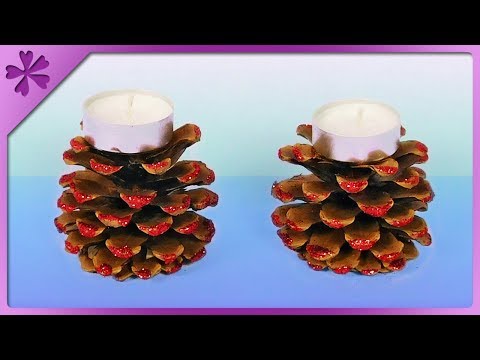
Hi. Today I will show you how to make candle holders out of pine cones.
Detailed list of all needed items is in the description of this video.
Remove a top part of pine cone by using wire cutter.
Apply a glue on all the scales of pine cone.
Now, apply a glitter.
Shake the pine cone to remove an excess of glitter.
Let the glue dry.
Finally, place a tealight candle on top of the pine cone.
And it's done.
These candle holders will looks gorgeous on a Christmas table.
Of course, instead of glitter you can use various small decorations.
I invite you to my channel, Facebook page and Instagram profile.
Thanks for watching. Bye bye.
-------------------------------------------
albee福利辣照二連彈!一個前傾」正面上下開更火辣:開始放大絕了 - Duration: 3:08.
-------------------------------------------
5 Favorite Books by Latinx Authors - Duration: 9:02.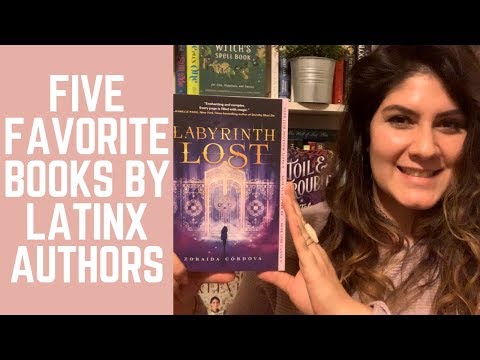
I'm Vanessa. I'm a contributing editor here at book riot. And unless you've been
walking around doing a little bit of lalalala, you have probably been
disheartened and heartbroken by some of the news coming out around the us-mexico
border and really surrounding the immigrant narrative in general.
Feeling kind of downtrodden, I decided I wanted to take a little bit of time this week
to ignore the negativity and instead focus on empowering and uplifting the
voices of some pretty fantastically talented Latinx individuals, in this
case authors. So I want to share some of my favorite reads written by Latin
American authors as of late. Here we go. First two books we're gonna talk about
are kids picture books. The first of which is Alma and how she got her name by
Juana Martinez-Neal. These-- this author is Peruvian American but I, as a
Mexican-American as I'm sure we'll tons of Latin Americans from all sorts of
countries, relate so much to this beautiful story of a little girl whose
father is explaining to her what the meaning is behind each of her names.
Because her name is not just Alma, it is
Alma Sophia Esperanza Jose Candela, which is a fantastic name if I've ever heard
one. So I know I'm the anomaly in my family only having a first and last
name. Shout-out to my parents for giving me the initials VD. Most often in Mexican
naming tradition, you'll have a first name, you'll have a last name, that last name
is actually two names because it is your father's last name and your mother's
maiden name, and then you'll have one or more middle names that could be
something completely unique or the name of a saint or a relative. Long story
short, I think this is such a fantastic little story to teach kids who come from
that particular naming tradition that they should have pride in their names.
That it's beautiful. It's nothing to be ashamed of. That it's actually pretty
freakin awesome. So that's Alma by Juana Martinez-Neal.
Next I will talk about Dreamers by Yuyi Morales, which is first
and foremost just a stunning work of art. All of the art in this book was drawn
and painted, as is explained at the end of the book, by Yuyi herself.
It's just bursting with color. It's awesome. And it's actually her story.
So in 1994, Yuyi Morales became an immigrant when she crossed the border in
Mexico to Texas and I think made her way eventually to Northern California to
join the father of her two month old son who she was getting ready to marry. And
her story, much like the you know main character of this book, is one of
crossing the border in search of a dream, of opportunity, and you know feeling a
little bit lost when you find yourself in a new place where you don't speak the
language, where you are trying to both fit in and also hang on to pieces of
your culture. There's a really great scene where she finally like discovers
what a library is and how amazing and eye-opening and educational that
experience is for her. Again, beautifully drawn, really touching story. I love that
there is an immigrant narrative that has been put down to paper in such a
beautiful way. So Dreamers by Yuyi Morales. Next pick is YA and it's Erika Sanchez's
I am not your perfect Mexican daughter, which feels like a manifesto from my
young life. So in it we meet Julia who is 15, going on 16, and she's having a
rough go at grieving the loss of her older sister Olga who just died. Olga
was I believe in her early twenties. She was going to college, got a good job, she was
supporting her parents and was really pure and noble and was always gonna take
care of mom and dad. And Julia is rebellious. She wants to be a writer. She
wants to go off to college. She's a little bit embarrassed by what she
perceives to be her parent's kind of strictness and and real strong adherence
to which she considers to be kind of outdated Mexican customs. And she also
really resents constantly having been and still being compared to her sister
when she, you know, is trying to forge her own identity. I've seen some reviews
complain that Julia is a bit of a brat, to which I say have you met teenagers?
It's kind of in their job description. I think it is
just a really honest look at what it's like to be that age and to be straddling
that difficult position of wanting to, at times, assimilate into mainstream culture
but also hanging on to pieces of where you're from and how you were raised.
It's about grief. It's at times very sad. It's also coming of age,
finding your place in the world. I love that I got to see names like Ama and Apa on
the page which were what I referred to my parents as growing up. And I've heard
Erika say that she wants to write the stories at wish she wishes she saw
growing up. And this is exactly what I wish was around when I was a kid just
like desperate to see someone that sounded or looked and felt like me in
the books that I read. So thank you so much to her for doing this. I recommend
this every chance I get. And that's I am not your perfect Mexican
daughter by Erika L. Sanchez. Another YA author whose work I'm kind of
obsessed with is Ecuadorian American's Zoraida Cordova and her Brooklyn
bruja series, the first of which is labyrinths lost. Bruja is Spanish for
witch and in this book we meet Alex who is a teen who happens to be the most
powerful enchantress that her generation has ever seen. But she's not
down with the magic thing. She hates brujeria, she rejects it. She doesn't want
anything to do with her powers. So on her Death Day celebration in which she's
supposed to sort of come into her powers, she decides instead to cast a spell
that's gonna rid her of those powers for good.
Of course it backfires in epic fashion and it leads to her whole family being
swallowed whole by the earth and leaving her alone. She has to decide how and when
to potentially harness these powers to go get her family. It's a bit of an epic
journey at this point. There's some really fantastic world building.
My favorite part of all of course is getting to see Latinx culture injected
into a genre story, a fantasy, an urban fantasy where the Latinx culture
is a thing but not necessarily a thing that the whole book is structured around.
The second installment in the Brooklyn Bruja series is Bruja Born and it's
also out now. I loved it. I believe there's one more coming. Again
I just love everything that she's doing with fantasy and I can't wait to read
everything else does she puts out. So that's Zoraida Cordova and the
Brooklyn Bruja series. And the last book I want to talk about is crux: a
cross-border memoir by Jean Guerrero, who I was fortunate enough to meet this
year when the bookstore that I work for hosted her book release party.
So Jean is a claimed journalist. She is the KPBS Fronteras reporter based
here in San Diego. And her memoir is obviously her story but also that of her
father, or at least her attempts to get to know the man that he was, and is.
In her childhood, her father's presence was a little bit kind of
erratic and all over the place. He was very, very intelligent and just insanely
curious. And his curiosity's over time took on kind of an obsessive quality.
So much so that he left Jean and her mother behind while he went to travel to all
these different parts of the world, ultimately settling in Mexico.
It's unclear how much of what he experienced was you know an actual true life
experience or might have been a hallucination. He was convinced at one
point that the CIA were running mind-control experiments on him. So when
Jean is old enough to do so, she embarks on a journey of her own to try to get
down to brass tacks about who her father was, what he experienced, what parts of
his narrative were fact, fiction, or fabrication. And that leads to her doing
kind of a full on family history that takes her obviously across the border
into Mexico. She finds out she has like a clairvoyant in the family and really
questions whether her father's eventual diagnosis of schizophrenia
was accurate or not. So anyway there's so much to love here. It is timely and above
all her writing is just gorgeous. I guess I expected as a journalist that
it might be a little more cut and dry. But it's not. It's downright lyrical
and I've heard that from multiple people that I've recommended this book to.
So definitely check it out. That's crux: a cross border memoir.
So thanks for joining me today on this little Latinx author love fest. It is
just so important and something that I'm so passionate about to support and
uplift and talk about the work, not just of these Latinx authors but tons of
others that I obviously couldn't ever get to in one video. And really to draw
more attention and support the work of marginalized voices, in general. It's so
important. We need diversity, representation matters. I'll say it 'til I'm
blue in the face. Thanks for letting me do it for a couple of minutes of your day.
And I'll see you next week. Bye.
-------------------------------------------
越老越辣!劉嘉玲黑蕾絲透視裝秀辣肉!53歲依舊保養得宜同場的名媛都輸她! - Duration: 3:01.
-------------------------------------------
最帥大叔為愛帶大4歲女友私奔…扛下兒子所有大錯 24年後竟承認:不是親生的 - Duration: 8:15.
-------------------------------------------
自爆體重106斤!陳喬恩被拍衣服穿太緊,驚現『可疑肉團』&『麒麟臂』?! 網友:贅肉都被勒出來了 - Duration: 5:39.
-------------------------------------------
Gigantyczny wyciek o brutalny sekret Kaczyńskiego. Polacy zaniemówili - Duration: 9:46.
-------------------------------------------
Stolarze mówią o branży i życiu - Blum w Trasie 2018 - Duration: 35:01.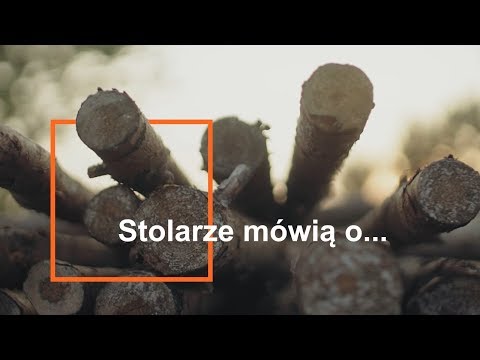
Presents
There weren't any computers.
You had to take a liking to a machine and not feel intimidated by it
because then you could easily destroy it or do something careless.
This was my great grandfather's drill.
It is quite advanced.
My father used more high-end equipment.
Two rotational speeds, it took some work to use it.
There weren't any soft close cabinets then.
Thirteen years ago, the soft close drawers were top-shelf products.
The times are changing.
You need to replace the machinery, have your eyes wide open,
watch the market trends or you will lag behind.
I would feel stupid
if a client asked me about something I don't yet have.
Clients know exactly what we can do for them.
Clients have become more aware in the area of product purchase.
They know what they want.
I try to approach them individually to make them happy.
There are different ways to do it.
CARPENTERS TALK ABOUT...
FUNCTION
My name is Iza Bucka.
I have worked as interior and furniture designer for 20 years now.
I am also a carpenter.
I run a family company and continue the family tradition.
Before I start designing I take some time to talk to a client
and learn their needs.
I take their preferences into account
and try to make the project whole.
For me these are the two equally important things
that make a good project.
First, we take care of the visual aspect
We want the project to be breathtaking.
This may convince a client to buy it.
After developing the visual project
we look for furniture that best fits the interior
so that the kitchen is nice-looking but also ergonomic.
Maybe we should convince a client with practicality
just ask him to take something out from a cabinet
and when he opens a drawer and has access to everything
he stops thinking about the looks
and focuses on the practical aspects of using the kitchen.
ERGONOMICS
My name is Gosia Błaszczak
and together with my husband Piotr we run Vigo Meble company.
We have four showrooms
and a carpentry shop, in which our designs come to life.
Once, the kitchen was in fact a place where food was prepared.
That was the main focus of our clients.
Now, most houses are based on an open floor plan.
However, we still need to hold to certain standards.
We have to talk to our clients so that the crucial kitchen zones
are well-designed.
Such zones are the ones by the hob and the the sink
and the storage unit.
There is a number of basic kitchen elements that must be easy to use,
ergonomic and based on durable systems with a longer warranty period.
A technological process taking place in the kitchen
should be based on a triangle.
The more equal the triangle sides,
meaning the number of steps taken during the production process,
including cooking, the better the functionality.
Kitchen test drive - a great solution.
Clients love it.
Once they try it they say this is awesome.
You can call it "cabinets on wheels".
I show clients a 3D kitchen using a computer.
They can do the same standing in front of the kitchen,
moving the cabinets around
and change the location of appliances to their liking.
It is helpful especially for those
having some trouble with spatial imagination.
For them the test drive is a must.
Sometimes a client tells us that the trip to Blum to have a test drive
helped him finally understand the layout.
It also helps us because the client learns what he wants
and we have a whole project worked out.
In the past the supplies were stored in additional rooms.
Now we make the kitchen bigger to find extra room for such supplies
and this is where the pantry-cabinet really works,
bacause it is spacious and offers everything at a hand's reach.
Space Tower is a dry refrigerator for products
that should stay out of the fridge.
When placed side by side they solve many problems.
We have our supplies at hand and we unpack our groceries faster.
Most clients decide in favor of the solution and are happy with it.
Time is of great significance nowadays
and time is saved when everything has its place and is easily accessible.
We need to explain it to our clients,
which is why there are several kitchen projects presented here.
We work with a client, ask him to come here - to our showroom.
To show him the difference: cheaper, more expensive guide
You need to know how to help a client.
The kitchen is as good as the materials used to make it.
There are elements, which are durable and of little significance
but there are such moveable parts as lifting mechanisms,
MOTION hinges, drawers, guides that wear out
and the quality determines their lifespan.
So, that's about it.
Soft closing guides and hinges are widely used.
We virtually stopped using other solutions.
My name is Paweł Cwalina, I run a carpentry shop.
The company's name is Wesoły Kornik.
We make all kinds of custom furniture
which sometimes requires using certain tricks, which I personally love.
It is a sign of the times.
Developers may still build objects of the same size,
but the apartments are smaller and smaller
and people want the kitchen, apart from being convenient and nice,
to be technologically advanced.
A trash can drawer is used more often than the front door.
Hence the popularity of the Servo-Drive system,
which is applied in many kitchens.
This is what people want, they want everything simpler, faster.
Electrical solutions are very convenient.
When we ask a client if he wants Servo-Drive Uno,
which costs this and that, he often decides not to buy it,
but when he buys the system in package
then he often realizes afterwards that he "has something like that".
We do not ask a client if he wants electric drawers,
for us they are standard.
My husband eats a lot.
My husband eats a lot and I have to cook all the time
because once I cook something he eats it and I have to cook again.
This has its good sides
because I have great practical advice for our clients
what to avoid, where to place the countertop, a drawer, trash cans.
If we cook ourselves, our contact with a client is easier.
The Aventos HF lift applied by Blum is great.
It gives kitchen users the possibility to open all cabinet doors
using one button or with two, three movements.
We do not walk around opening every cabinet
and the cabinets do not interfere with our work in the kitchen.
Then we close everything and once again enjoy our beautiful kitchen
without wasting time on opening and closing cabinets
or on searching for products because once everything is open
we may easily locate the product we are looking for.
These are the things that once installed, stay in the furniture forever.
So, I think that a functional and well-designed kitchen
is money well spent
because it saves us time usually spent on housework.
TIME
The downside of self-employment is that you spend 24 hours a day,
7 days a week at work.
Why did I decide to be self-employed?
I wanted my life to be fulfilling.
I think working for someone would not let me enjoy it.
Of course, there are better times and worse times.
There are times when I can have my 1 o'clock coffee
without anyone standing above me and telling me to work.
But there are also days when I drink my coffee at 9 p.m.
because I have work planned until 2 a.m.
I am Marcin Barczewski, the owner of Fachu Meble.
I am a wood technology technician by education.
Is my job stressful?
Yes.
Unfortunately yes and currently I usually fight a battle with time.
We always work against the clock, we always have too little time.
At first my wife was fine with the fact
that I spend most of my time at work
but when my son was born
I noticed that I am missing out on his childhood
and on many occasions I had to choose between
his performance and work and many times I wasn't there.
Today everyone wants to have everything right away
and gives us deadlines impossible to meet.
Companies do not have much choice,
accept the deadline and try to meet it.
My name is Tomasz Włodzik, I am the owner of Forma Meble company.
How did I become a carpenter?
My grandfather would carve a piece of wood and ask me to sit on it
to stop it from moving.
He carved and carved using a hand carver and I sat on the board
and must have fallen in love with carpentry through my behind.
Unfortunately my grandfather passed away but I kept his tools.
He wanted me to have the tools
because he knew I would not destroy or discard them.
In the past the tools were difficult to get.
When he found a broken file, my grandfather would keep it,
he would make handles for every blade, knife or needle he found.
In the past the furniture was hand-made so it took a lot of work.
My friend once told me that
when his father worked in a carpentry shop during the war
and a client ordered one set for a bedroom
there were three men who worked on it for a month
and they had to split the money for the month between themselves.
Today when a client orders furniture for a bedroom
we need to do it in one day.
OPTIMIZATION
What definitely changed are the technologies used.
They have become more advanced and made our job easier.
My father's museum displays
the tools of my great-great-grandfather Florian, a carpenter
and when you compare his screw-driver with mine
you can easily answer the "what changed?" question.
The market develops really fast and we try to keep up with it
by introducing to our offer Blum Legrabox drawers,
a professional product used in 50% of our kitchens.
We also adapted tools to make such drawers.
For example, a milling machine, which we bought to mill the bottoms
and which makes our work easier.
We now see the difference in time used on the same activity
before purchasing the machine.
Most of all, the product quality is much different now.
The machine helps us achieve great precision
when building a drawer, a cabinet, anything.
I have this saying: "work well-organized is work well-paid".
Why would we do something two times longer
if we can do it two times faster.
I tell my boys to "clean the shop" but a clean shop is a clean head.
We definitely go for all-purpose solutions
because they make production easier.
It is easier to have one, multi-purpose guide
than use numerous different guides.
These days a carpenter must follow the technological development
whether we say about machining centers or furniture design programs,
a modern press or an edge bander.
For the company to develop, even if it is tradition-based
and even if it works based on tradition, using simple machines
it must follow the technological development.
This is the future.
Dynalog is used mainly for furniture production.
It changes forms into cross sections.
When we introduce a kitchen to dynalog,
the program selects a set of accessories
and furniture parts for a particular kitchen
and generates all technical drawings
showing how to assemble the kitchen
as well as all kitchen elements and drilling holes.
It makes things much simpler for a person who places an order
or releases goods from the warehouse.
Technology and furniture are closely connected
and it does not apply only to design, which also changes
but there are certainly at least a few technological changes a year.
How did we meet?
I had a car accident
and my doctor recommended that I swim regularly.
When we met my wife was in her swimsuit.
You probably already know about the meeting at a swimming pool.
To cut the story short, I could not leave her alone.
That is how we met.
They say that a good wife leaves after 7 years
but I wouldn't want my wife to leave, we are great together.
We share everything.
We live together - we share hobbies.
I don't know any marriage that would spend so much time together.
Usually people are surprised it's even possible,
I often hear "If I worked with my wife it would not end well".
We must certainly like each other to spend all this time together.
We share all happy and difficult moments we face as a company.
For me this is very important.
SUPPORT
Sometimes life throws different challenges at us
in such moments the Easy Assembly app is a great technical help.
You just need to activate the lift, specify a cabinet's height
and it will adjust itself, the app shows all holes, heights.
If you don't have the book or the application
you can always call a technical consultant
who even on his way to Hannover will stop the car
and answer all the questions.
"You know what, I am driving now, I am on holiday,
but I will tell you everything you need"
and he really tells us everything, so the consultant is great.
I value my employees.
I am very proud of their work.
As I said, for me they are the carpentry elite
and I think that they like a challenge.
I have a good and strong team that gives me great support.
Work of a carpenter is wonderful
but young people must learn and must want to learn
improve their skills, constantly develop, attend trainings,
I learn something everyday.
Trainings are important to become better, expand your knowledge
to keep up with the market and current trends.
MARKETING
We usually meet premium clients
when I work with them as interior designer.
Clients contact me after seeing my work
and once they learn that I have my own carpentry shop
which means that I will bring our design to life,
they treat it as the added value.
A client is attracted by the display and the lighting.
Whereas publications, good website, videos
show a client the kind of furniture we make.
This would be virtually impossible without good advertising.
We receive marketing support
including car-wrap advertising
or placing special signs on drawers, furniture or countertops.
My father is Mister Kornik [English: borer] and I am Mister Kornik.
We hear "Good morning Mister Kornik" at the stores.
The name is old, my father used it
before I even started working on my own.
He wanted it to be something original,
a name that would attract attention and make people smile.
To this day, after 15 years the clients come back to us
and say "I couldn't find you, but I remembered it was borer something"
and they search through the Internet and find us.
We are very trustworthy.
We rely on good old grapevine and not on Facebook
but it works, we have many clients and a lot of work.
HERITAGE
It is a family history.
My grandfather was 12 years old
he took his shoes and went looking for a job.
He finished his travel in Vienna
where he was hired as an apprentice by some carpenter.
The carpentry shop was built by my grandmother Stefania in 1922.
I graduated from the faculty of Industrial Design
at the Academy of Fine Arts
making a piece of furniture as my diploma project.
I tried to bring my designs to life at different carpentry shops
but the carpenters were usually unreliable
or said the designs weren't feasible.
I decided that this is pointless.
The designs were developed by me
so, I have to be the one to bring them to life.
About my daughter? What she does?
She makes furniture.
Is she good at it?
I think she is good.
They say you should be energetic to keep up with all this
and she has energy.
I talked my brother into reviving a carpentry shop,
which was run by my grandfather and father and was then closed.
I like the combination of stone and polished stainless steel,
natural veneer or solid wood,
when the beauty is in the quality and class of the materials used,
in simple forms.
DESIGN
Currently, the main market trend
is a designer kitchen
requiring the use of modern materials, such as quartz sinters.
This means that we must search through the market
for products to use with such fronts.
Fortunately, there are such solutions as thin hinges
which can be used with such fronts.
For me personally
interesting, creative, modern and also timeless materials
are what really catches the eye.
We got used to standard, silver hinges.
They started to be problematic in case of top-shelf kitchens
made for clients who pay attention to every detail.
It was problematic when we had to use bright hinges with dark fronts.
Now, the market offers dark hinges
thus making our work easier.
Listen, this is the real problem of our times.
Clients have too many things.
They start to collect things they don't really need.
I open a drawer and see 4 potato peelers
and then I ask a client if she uses all four peelers
and why there are four and not one.
Once or twice I organized my client's kitchen.
I asked them to change the location of plates
and the client says this is how she had it before
and I tell her "this is not how we do it".
Sometimes people just don't see something
and we need to show it to them.
Their clothes are not stored properly,
they should be folded or sorted differently.
A designer is like a mirror.
Organizers help keep the drawer contents in order.
Their name implies their function.
They also help keep the drawers quiet
because the items inside them are well-organized
and do not move around.
We mainly use Legrabox drawers
because they have these thin, beautiful panels
in white, anthracite, brown-black and inox steel colors.
I have a sense of mission, I feel that I need to educate my clients
smuggle beauty, harmony and this gives me great satisfaction.
I show my clients different combinations of materials, colors, proportions
that are beautiful and look nice.
I am lucky or unlucky, depending on how you look at it,
that my job is my hobby, my passion.
Maybe it's the question of balance and harmony
between work, passion and family life.
I think you find that as you grow older
and I have it now.
BALANCE
I moved here for the views.
Here we had our two children
but before my second child was born
we knew that we wanted to raise a child and work in a nice place
which is inspiring
but also helps us relax and escape from the hustle and bustle.
You know work is work and life is life.
If you took a walk around here, you would see the views
that are best described by the words of Mickiewicz
"I made for the open body of dry ocean's breed".
Wood has been in our lives for many years.
The best moment is when I hear "This is beautiful Mister Kornik".
The smell of plywood is different
when you work with wood in a carpentry shop,
the smell of wood is everywhere
and a real carpentry shop is the one smelling of wood.
I would once say that carpentry is my hobby
but today I sometimes need a break from it.
I have a different passion - motorcycles.
I ride all around Europe.
Today I am going to Warsaw,
tomorrow my daughter has her second birthday
so, I will have to come back from Warsaw to go to her birthday party.
Some things have changed
and today I know how to draw a line.
I try to take part in a family life when I am needed.
I like to take a day off when I want
and organize the work by myself.
Sometimes I don't feel like working so I take a break
to work better and with satisfaction when I feel like it.
I must admit that when I see the finished kitchen and a happy client
because it's his smile that is most important
I am happy myself.
This is a great feeling
because nothing gives as much reinforcement as working for people
as their happiness, satisfaction.
Sometimes in the very evening I get a text from a client instead of a call
saying that they have what they wanted, that this is great
and that moment is very rewarding.
The film was made under the patronage of BLUM POLSKA
starring
and
Thanks to carpenters' families and people involved in the production.
Production commissed by BLUM POLSKA
-------------------------------------------
MY MLBB LOOK 분위기 있게. 말린장미 메이크업 🥀(ENG CC) - Duration: 10:45.
Hi guys~
It's been a while since I filmed a Talk-through makeup tutorial.
The weather is getting cold these days.
So I will start making makeup with warm sweater today!
Because It's been a while since I got up, I already did the basic care and wore the sunscreen.
Now I'll start base makeup step
I use this foundation for daily use these days.
This is Estee Lauder's Futurist aqua brilliance foundation.
When you apply base makeup in dry season like these days,
you have to be careful about dead skin cells.
I put a little drop of face oil in the foundation
and mix it~
With using foundation brush moistened with water
( I'm gonna put on it all over my face from the inner side )
you can add one or two more drops of oil
depending on your skin condition or taste.
One thing you should keep in mind, if you use too much oil,
Something like…Foundation would not be applied well on skin?
It isn't absorbed well in the skin and can get super oily
So you need to control the amount of it.
This Estee Louder brand foundation has a lot moisture.
It has also good coverage and good durability.
I really love glowing skin complexion
so I'm gonna try it again today.
Let me show you the coverage of the foundation.
Consider that I have a lot of facial blemishes~
Because it's coverage is so good, it can cover redness and tiny blemishes well
so I do not need any additional concealers.
Next, I'll use 'Make up for ever's UHD pressed powder.
Firstly apply the powder on the brush
For keeping cheek's glowing condition
I'll apply it on my jawline and hairline
Are your skin conditions okay these days?
My skin is so dry and flanky. ;(
I'm gonna use a smaller brush to get rid of T-zone's oil.
So anyway, you know sticky moisturizers, right?
moisturizers which are clogging your poles If you use it in the summer. haha
I apply that sticky product on my face before going to bed.
I'll use Espoir's Contour powder for shading.
Um, did you find out my face is puffy now?
Actually I drank with friends yesterday.
Im not good at drinking…
Ah that's what many people are talking about, right?
'I do not drink well, but I like the atmosphere of drinking with people'
Anyway, it's real haha
I couldn't help it. Yesterday was my friend's birthday.
Celebration and alcohol are inseparable.
So I had a lot of fun.
But I am trying to avoid drinking too much these days
So my face is a bit swollen but I'm completely sober now.
I'm gonna add contour to my eyelids in advance.
Now shading is over,
Now in this state, I'll spraying a spray for shetting..
(pronunciation miss) shetting?
for Setting beautifully.
This is YSL's Top secret setting spray.
Ah~ I really like the unique fragrance of YSL's spray.
Something like a luxurious scent? I love it!
And I'll just apply eye primer.
Anyway, I asked my friend
what she would like to have for birthday present.
Then, she told about orchid color sweater from COS brand in my lookbook.
That sweater is thin but warm and has unique color
so it is rare to see in winter.
My friend told me she want it
so I visited a COS store and bought it for her,
And she told me she needs a foundation, so I also bought Estee Lauder's product for her present.
I was happy to give presents my friend need.
I hope she uses them well. Haha
And moving on to my eyeshadow,
I'll use Laura mercies's ginger color.
This is really good for daily use
I show it to you on makeup video for the first time in a while.
I'll apply this color all over my eyelids and define shadow.
Isn't this pretty?
Today I'll make my eyes to look deeper
with just one color.
Now I finished eye shadowing.
Next, I'm gonna draw my eyebrows with Benefit's eyebrow pencil.
and I just made end of eyebrow slightly arched.
then I tried the other side.
Let's finish drawing eyebrow now,
and I'll put peanut brown color brow cara
on the head of the eyebrow and make warm and soft mood.
And I'll use Mergy's brown gel pencil eyeliner.
let's fill in the water line and lash line
it's color is bright so I'll draw the lines without hesitating.
Finish drawing eyelines,
I'm gonna use eye shadow which has brown color without red
its color is like this.
I'll fill in outside the under eyebrows(the outer corner eye) softly.
and also fill the empty area to make eyes look bigger.
Aren't they curled up well?
I'm not sure whether I use false eyelashes or not.
I'll think about it again after applying mascara.
This is my favorite mascara~
I'll curl up eyelashes with Kiss me's Heroin mascara.
Today I make eye makeup with only deep shade
so I'll add a point with pretty color mascara on lower lashes.
this is a soft rose color mascara.
I'll apply it on lower lashes.
This is a dried rose color mascara,
when I put it on, it doesn't look strong like black mascara,
but it has a soft rosy mood.
Then I'm gonna apply blusher now.
i'll use these two products.
Ginger color is like this.
And sand pink color is like this.
Now mix these two colors ~
And I'll dab and apply it underneath eyes and in cheek area using brush.
and I'll brush the nose horizontally for applying color lightly.
Ta-da~ moving on to lips,
I will use a No wear odd pencil which was released as a holiday collection in Espoir.
Retro design of package is so pretty
and the pencil size is so cute!
I'll show you this color.
It looks good right?
It's a product that melts on your lips
and it's very transparent and moist without it clumping up together.
I'll pick A+RED from these three color.
I think It's color is dried rose's color with some red.
I tried to make my lip toned down to put on lip makeup My face looks bad. haha
Anyway this product is applied very smoothly.
It's moist but it doesn't look glossy too much
and it feels very comfortable.
So I think this product is good enough to use as a blusher.
This is very good at blending enough to put on the cheeks.
Apply once more on the inside of your lips~
Now I finished makeup simply.
Um, which earring should I wear today?
It's hard to pick.
Lastly, I'll apply Heaven's hue highlighter from 'Stila'
on upper lip line and cheekbones.
on upper lip line and cheekbones.
I appreciate and thank you for watching this video!
be careful for the cold all the time.
Bye~~
-------------------------------------------
Uomini e donne anticipazioni, i dubbi di Teresa su Andrea | Wind Zuiden - Duration: 4:28.
-------------------------------------------
Italian fish soup (or brodetto) by Angelo Troiani - Duration: 9:24.
Hi, I'm Angelo Troiani. I'm executive chef in the Acquolina and
AcquaRoof restaurant, where we are now. Today I'm making a fish soup -
no, it's actually wrong to say "soup". Soup is simply the preliminary
part, the liquid part, so it's something that we could drink. We are
actually eating the fish, as well, so I'm making a light broth
in my way, something that taste a little like the Marches and a little like Thyrrenian.
For the soup, we need a good variety of fishes, as the smell, fragrance and taste
come exactly from this mix of crustaceans, seafood and fish.
The ingredients are: Atlantic stargazer, goatfish, tub gurnard,
red shrimps, caramote prawns, mussels, clams. Garlic, onion,
red and green tomatoes, bell pepper, parsley. Bread, oil, salt, vinegar.
First step is cleaning the fish, filleting, taking the carcasses and
heads to make the soup, so, proceeding in a simple way:
first I'm removing the head from the stargazer. What I have to pay attention to is these
bones. They hurt a lot. I'm taking a small piece of fillet. It has a very
firm meat, it's the right fish, typical when making a light broth or soup as it must be
cooked in moist. I'm removing the pulp as well and I'm taking the fillet. I'm removing
the other fillet as well, and I'm taking the carcass that I'm using to make the soup.
I'm making the same with the goatfish. I'm lightly carving the bone
to clean it better and letting out the blood part it contains
inside. Here, as well, I'm making a nice fillet.
Same with the tub gurnard. This is one of the most ancient fishes,
the last heir of the flying fishes family, let's say. It's very suitable to
the use in soups and sauces, and so in our light broth. Now, as before
I'm removing the darker part, the stomach, and I'm taking the fillet. I'm taking the
squid that I cleaned, removing the suckers part that are
hard and don't cook, I'm keeping the tentacles and I'm taking two nice pieces of the squid.
I'm cutting in the two directions the squid. I'm doing this to simply obtain a choreography,
let's say, regarding the presentation.
We're now cleaning and washing the carcasses to remove impurities and
obtain a base with a cleaner taste. I'm trying to clean as best as I can and remove
the little clumps that are inside. From these carcasses, I'm taking
the flavor, concentrated as if it was
some kind of stock cube, so to say, I'm trying to take all the flavor
and taste of all the fishes. We're now adding the bell pepper as it is, whole,
in the oven. We're letting it roast at 180°C, in a dry oven, without extraction.
We're now making the soup. Onion or spring onion, I like tasting
a lightly more persistent flavor, so I prefer the fresh spring onion.
I'm coarsely cutting it, without much care. Then a clove
of garlic. I'm removing the core if it is present, but in this case it's not there. It's a very
fresh garlic. A drizzle of oil, the carcasses.
As you can notice, I added the garlic and the onion as well as the carcasses. It means
that I'm not browning the garlic and onion before. Why? Because I don't
need it. I don't have to destructurate the oil
before and I don't need a stronger flavor from the garlic
and onion. Doing this, I'm getting
a healthier recipe, being this the base of all my recipes.
I'm cutting the tomatoes: the green tomato, that gives a characteristic taste that is
lightly sweet and sour, together with the vinegar that diversifies it
from the classic sauce for pasta.
Now I'm taking half of a red tomato, as well.
We're now moving on the flame.
We're now waiting for the temperature to rise. The carcasses will let out water first,
meaning this strong flavor and fragrance of fish, then gradually
will caramellize and create a more concentrated taste. The fish
flaked apart well, creating this coat, this light glaze on the bottom of the
pot. This is what I need to give such a concentrated flavor.
I'm adding the vinegar. White wine vinegar.
I'm cleaning, scraping the bottom of the pot and I'm adding the tomatoes. I'm cooking
the tomatoes a little bit, waiting for them to flake apart and create some kind of sauce, adding
a little bit of water from time to time. I'm letting the soup ripen and concentrate,
then I'm blending it. As the soup cooks, I'm going to finish
the preparation of the pepper, cutting the parsley and the bread to complete
the light broth, the final preparation. I'm cutting the parsley and keeping the stalks. The stalks
are the tastiest part of the parsley, for me. It's the most scented and
mentholated part, while the leaf is the most bitter part, the stalk
keeps the nicest fragrance of the parsley. If they're not too big, nor
woody, I'm always using them. I'm cutting it coarsely, to keep the
fragrances and not to ruin the parsley too much.
We're making the croutons. Since we have to cook it again, the crust tends to become bitter,
so I'm just keeping the soft inside of the bread.
These are the croutons and at this point I'm moving them in the oven.
I'm now taking the pepper I put in the oven before, placing it in a simple
bowl and covering it with film. This lets the vapor that is left
inside the bowl detach the skin of the pepper well.
Five minutes are enough. I'm now shelling the shrimps and caramote prawns, the crustaceans, then
using the tip of a knife or a stick, very simply,
I'm lightly carving on top of the back of the crustacean and pull, removing
the stomach. We're now removing the skin of the pepper. You can see
how easily we can remove it. We're peeling the pepper, opening it and cutting it in pieces.
The soup is ready, can you see? The tomato flaked well, and so the fish,
the head released all of its flavor and the part of the
fat. These are fatter fishes, so it is now ready. I'm now sifting it
with a fine net sieve. This one is called chinois and allows you
to press well and extract all of the juice. Done! Now we just have to add
the base. If you noticed, I didn't add salt, as the broths and bases
should never be salted, because they are reduced, so I have to get to
the final preparation without ever adding salt.
Now I'm adding the fishes, the squid, the crustaceans,
the seafood. I'm salting it. I'm adding the peppers I previously roasted
and peeled. Just a light drizzle of oil. I just have to close it, using
a glass lid so I can also check on the cooking.
We're using a vapor oven, 85°C for about 25 minutes.
I'm now adding a couple of croutons and at last, a drizzle of oil. A fruity
and light one. The light broth is ready, now try to make it at
home! It's not difficult, all you need to do is to
understand what you have to do. Or you can simply taste it here with us, in
AcquaRoof, Molinari Terrace, in one of the most beautiful terraces in Rome. We're waiting for you!
Ciao!
-------------------------------------------
Gigantyczny wyciek o brutalny sekret Kaczyńskiego. Polacy zaniemówili - Duration: 9:46.
-------------------------------------------
ARTICLE 13 THE END OF THE INTERNET| ISABEL MAKE 400 NEW EMPLOYMENT| ZENU STILL IN THE CHAIN - Duration: 12:42.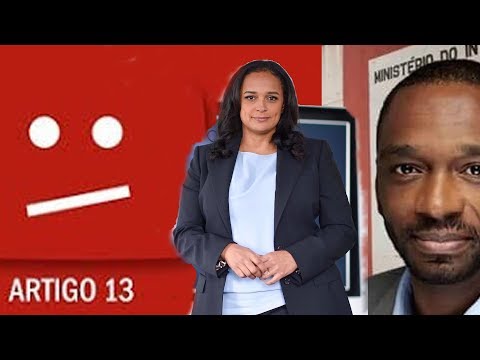
Hi boyz and girls
whats upp?
im etiandro sardinha
and welcome to new video
-------------------------------------------
Stolarze mówią o branży i życiu - Blum w Trasie 2018 - Duration: 35:01.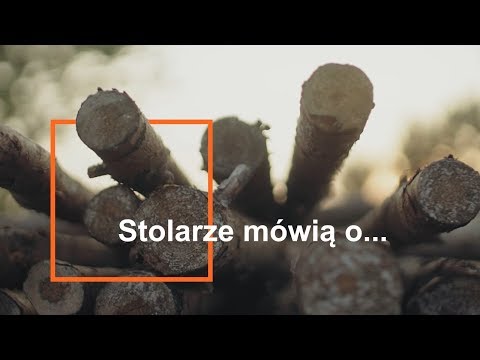
Presents
There weren't any computers.
You had to take a liking to a machine and not feel intimidated by it
because then you could easily destroy it or do something careless.
This was my great grandfather's drill.
It is quite advanced.
My father used more high-end equipment.
Two rotational speeds, it took some work to use it.
There weren't any soft close cabinets then.
Thirteen years ago, the soft close drawers were top-shelf products.
The times are changing.
You need to replace the machinery, have your eyes wide open,
watch the market trends or you will lag behind.
I would feel stupid
if a client asked me about something I don't yet have.
Clients know exactly what we can do for them.
Clients have become more aware in the area of product purchase.
They know what they want.
I try to approach them individually to make them happy.
There are different ways to do it.
CARPENTERS TALK ABOUT...
FUNCTION
My name is Iza Bucka.
I have worked as interior and furniture designer for 20 years now.
I am also a carpenter.
I run a family company and continue the family tradition.
Before I start designing I take some time to talk to a client
and learn their needs.
I take their preferences into account
and try to make the project whole.
For me these are the two equally important things
that make a good project.
First, we take care of the visual aspect
We want the project to be breathtaking.
This may convince a client to buy it.
After developing the visual project
we look for furniture that best fits the interior
so that the kitchen is nice-looking but also ergonomic.
Maybe we should convince a client with practicality
just ask him to take something out from a cabinet
and when he opens a drawer and has access to everything
he stops thinking about the looks
and focuses on the practical aspects of using the kitchen.
ERGONOMICS
My name is Gosia Błaszczak
and together with my husband Piotr we run Vigo Meble company.
We have four showrooms
and a carpentry shop, in which our designs come to life.
Once, the kitchen was in fact a place where food was prepared.
That was the main focus of our clients.
Now, most houses are based on an open floor plan.
However, we still need to hold to certain standards.
We have to talk to our clients so that the crucial kitchen zones
are well-designed.
Such zones are the ones by the hob and the the sink
and the storage unit.
There is a number of basic kitchen elements that must be easy to use,
ergonomic and based on durable systems with a longer warranty period.
A technological process taking place in the kitchen
should be based on a triangle.
The more equal the triangle sides,
meaning the number of steps taken during the production process,
including cooking, the better the functionality.
Kitchen test drive - a great solution.
Clients love it.
Once they try it they say this is awesome.
You can call it "cabinets on wheels".
I show clients a 3D kitchen using a computer.
They can do the same standing in front of the kitchen,
moving the cabinets around
and change the location of appliances to their liking.
It is helpful especially for those
having some trouble with spatial imagination.
For them the test drive is a must.
Sometimes a client tells us that the trip to Blum to have a test drive
helped him finally understand the layout.
It also helps us because the client learns what he wants
and we have a whole project worked out.
In the past the supplies were stored in additional rooms.
Now we make the kitchen bigger to find extra room for such supplies
and this is where the pantry-cabinet really works,
bacause it is spacious and offers everything at a hand's reach.
Space Tower is a dry refrigerator for products
that should stay out of the fridge.
When placed side by side they solve many problems.
We have our supplies at hand and we unpack our groceries faster.
Most clients decide in favor of the solution and are happy with it.
Time is of great significance nowadays
and time is saved when everything has its place and is easily accessible.
We need to explain it to our clients,
which is why there are several kitchen projects presented here.
We work with a client, ask him to come here - to our showroom.
To show him the difference: cheaper, more expensive guide
You need to know how to help a client.
The kitchen is as good as the materials used to make it.
There are elements, which are durable and of little significance
but there are such moveable parts as lifting mechanisms,
MOTION hinges, drawers, guides that wear out
and the quality determines their lifespan.
So, that's about it.
Soft closing guides and hinges are widely used.
We virtually stopped using other solutions.
My name is Paweł Cwalina, I run a carpentry shop.
The company's name is Wesoły Kornik.
We make all kinds of custom furniture
which sometimes requires using certain tricks, which I personally love.
It is a sign of the times.
Developers may still build objects of the same size,
but the apartments are smaller and smaller
and people want the kitchen, apart from being convenient and nice,
to be technologically advanced.
A trash can drawer is used more often than the front door.
Hence the popularity of the Servo-Drive system,
which is applied in many kitchens.
This is what people want, they want everything simpler, faster.
Electrical solutions are very convenient.
When we ask a client if he wants Servo-Drive Uno,
which costs this and that, he often decides not to buy it,
but when he buys the system in package
then he often realizes afterwards that he "has something like that".
We do not ask a client if he wants electric drawers,
for us they are standard.
My husband eats a lot.
My husband eats a lot and I have to cook all the time
because once I cook something he eats it and I have to cook again.
This has its good sides
because I have great practical advice for our clients
what to avoid, where to place the countertop, a drawer, trash cans.
If we cook ourselves, our contact with a client is easier.
The Aventos HF lift applied by Blum is great.
It gives kitchen users the possibility to open all cabinet doors
using one button or with two, three movements.
We do not walk around opening every cabinet
and the cabinets do not interfere with our work in the kitchen.
Then we close everything and once again enjoy our beautiful kitchen
without wasting time on opening and closing cabinets
or on searching for products because once everything is open
we may easily locate the product we are looking for.
These are the things that once installed, stay in the furniture forever.
So, I think that a functional and well-designed kitchen
is money well spent
because it saves us time usually spent on housework.
TIME
The downside of self-employment is that you spend 24 hours a day,
7 days a week at work.
Why did I decide to be self-employed?
I wanted my life to be fulfilling.
I think working for someone would not let me enjoy it.
Of course, there are better times and worse times.
There are times when I can have my 1 o'clock coffee
without anyone standing above me and telling me to work.
But there are also days when I drink my coffee at 9 p.m.
because I have work planned until 2 a.m.
I am Marcin Barczewski, the owner of Fachu Meble.
I am a wood technology technician by education.
Is my job stressful?
Yes.
Unfortunately yes and currently I usually fight a battle with time.
We always work against the clock, we always have too little time.
At first my wife was fine with the fact
that I spend most of my time at work
but when my son was born
I noticed that I am missing out on his childhood
and on many occasions I had to choose between
his performance and work and many times I wasn't there.
Today everyone wants to have everything right away
and gives us deadlines impossible to meet.
Companies do not have much choice,
accept the deadline and try to meet it.
My name is Tomasz Włodzik, I am the owner of Forma Meble company.
How did I become a carpenter?
My grandfather would carve a piece of wood and ask me to sit on it
to stop it from moving.
He carved and carved using a hand carver and I sat on the board
and must have fallen in love with carpentry through my behind.
Unfortunately my grandfather passed away but I kept his tools.
He wanted me to have the tools
because he knew I would not destroy or discard them.
In the past the tools were difficult to get.
When he found a broken file, my grandfather would keep it,
he would make handles for every blade, knife or needle he found.
In the past the furniture was hand-made so it took a lot of work.
My friend once told me that
when his father worked in a carpentry shop during the war
and a client ordered one set for a bedroom
there were three men who worked on it for a month
and they had to split the money for the month between themselves.
Today when a client orders furniture for a bedroom
we need to do it in one day.
OPTIMIZATION
What definitely changed are the technologies used.
They have become more advanced and made our job easier.
My father's museum displays
the tools of my great-great-grandfather Florian, a carpenter
and when you compare his screw-driver with mine
you can easily answer the "what changed?" question.
The market develops really fast and we try to keep up with it
by introducing to our offer Blum Legrabox drawers,
a professional product used in 50% of our kitchens.
We also adapted tools to make such drawers.
For example, a milling machine, which we bought to mill the bottoms
and which makes our work easier.
We now see the difference in time used on the same activity
before purchasing the machine.
Most of all, the product quality is much different now.
The machine helps us achieve great precision
when building a drawer, a cabinet, anything.
I have this saying: "work well-organized is work well-paid".
Why would we do something two times longer
if we can do it two times faster.
I tell my boys to "clean the shop" but a clean shop is a clean head.
We definitely go for all-purpose solutions
because they make production easier.
It is easier to have one, multi-purpose guide
than use numerous different guides.
These days a carpenter must follow the technological development
whether we say about machining centers or furniture design programs,
a modern press or an edge bander.
For the company to develop, even if it is tradition-based
and even if it works based on tradition, using simple machines
it must follow the technological development.
This is the future.
Dynalog is used mainly for furniture production.
It changes forms into cross sections.
When we introduce a kitchen to dynalog,
the program selects a set of accessories
and furniture parts for a particular kitchen
and generates all technical drawings
showing how to assemble the kitchen
as well as all kitchen elements and drilling holes.
It makes things much simpler for a person who places an order
or releases goods from the warehouse.
Technology and furniture are closely connected
and it does not apply only to design, which also changes
but there are certainly at least a few technological changes a year.
How did we meet?
I had a car accident
and my doctor recommended that I swim regularly.
When we met my wife was in her swimsuit.
You probably already know about the meeting at a swimming pool.
To cut the story short, I could not leave her alone.
That is how we met.
They say that a good wife leaves after 7 years
but I wouldn't want my wife to leave, we are great together.
We share everything.
We live together - we share hobbies.
I don't know any marriage that would spend so much time together.
Usually people are surprised it's even possible,
I often hear "If I worked with my wife it would not end well".
We must certainly like each other to spend all this time together.
We share all happy and difficult moments we face as a company.
For me this is very important.
SUPPORT
Sometimes life throws different challenges at us
in such moments the Easy Assembly app is a great technical help.
You just need to activate the lift, specify a cabinet's height
and it will adjust itself, the app shows all holes, heights.
If you don't have the book or the application
you can always call a technical consultant
who even on his way to Hannover will stop the car
and answer all the questions.
"You know what, I am driving now, I am on holiday,
but I will tell you everything you need"
and he really tells us everything, so the consultant is great.
I value my employees.
I am very proud of their work.
As I said, for me they are the carpentry elite
and I think that they like a challenge.
I have a good and strong team that gives me great support.
Work of a carpenter is wonderful
but young people must learn and must want to learn
improve their skills, constantly develop, attend trainings,
I learn something everyday.
Trainings are important to become better, expand your knowledge
to keep up with the market and current trends.
MARKETING
We usually meet premium clients
when I work with them as interior designer.
Clients contact me after seeing my work
and once they learn that I have my own carpentry shop
which means that I will bring our design to life,
they treat it as the added value.
A client is attracted by the display and the lighting.
Whereas publications, good website, videos
show a client the kind of furniture we make.
This would be virtually impossible without good advertising.
We receive marketing support
including car-wrap advertising
or placing special signs on drawers, furniture or countertops.
My father is Mister Kornik [English: borer] and I am Mister Kornik.
We hear "Good morning Mister Kornik" at the stores.
The name is old, my father used it
before I even started working on my own.
He wanted it to be something original,
a name that would attract attention and make people smile.
To this day, after 15 years the clients come back to us
and say "I couldn't find you, but I remembered it was borer something"
and they search through the Internet and find us.
We are very trustworthy.
We rely on good old grapevine and not on Facebook
but it works, we have many clients and a lot of work.
HERITAGE
It is a family history.
My grandfather was 12 years old
he took his shoes and went looking for a job.
He finished his travel in Vienna
where he was hired as an apprentice by some carpenter.
The carpentry shop was built by my grandmother Stefania in 1922.
I graduated from the faculty of Industrial Design
at the Academy of Fine Arts
making a piece of furniture as my diploma project.
I tried to bring my designs to life at different carpentry shops
but the carpenters were usually unreliable
or said the designs weren't feasible.
I decided that this is pointless.
The designs were developed by me
so, I have to be the one to bring them to life.
About my daughter? What she does?
She makes furniture.
Is she good at it?
I think she is good.
They say you should be energetic to keep up with all this
and she has energy.
I talked my brother into reviving a carpentry shop,
which was run by my grandfather and father and was then closed.
I like the combination of stone and polished stainless steel,
natural veneer or solid wood,
when the beauty is in the quality and class of the materials used,
in simple forms.
DESIGN
Currently, the main market trend
is a designer kitchen
requiring the use of modern materials, such as quartz sinters.
This means that we must search through the market
for products to use with such fronts.
Fortunately, there are such solutions as thin hinges
which can be used with such fronts.
For me personally
interesting, creative, modern and also timeless materials
are what really catches the eye.
We got used to standard, silver hinges.
They started to be problematic in case of top-shelf kitchens
made for clients who pay attention to every detail.
It was problematic when we had to use bright hinges with dark fronts.
Now, the market offers dark hinges
thus making our work easier.
Listen, this is the real problem of our times.
Clients have too many things.
They start to collect things they don't really need.
I open a drawer and see 4 potato peelers
and then I ask a client if she uses all four peelers
and why there are four and not one.
Once or twice I organized my client's kitchen.
I asked them to change the location of plates
and the client says this is how she had it before
and I tell her "this is not how we do it".
Sometimes people just don't see something
and we need to show it to them.
Their clothes are not stored properly,
they should be folded or sorted differently.
A designer is like a mirror.
Organizers help keep the drawer contents in order.
Their name implies their function.
They also help keep the drawers quiet
because the items inside them are well-organized
and do not move around.
We mainly use Legrabox drawers
because they have these thin, beautiful panels
in white, anthracite, brown-black and inox steel colors.
I have a sense of mission, I feel that I need to educate my clients
smuggle beauty, harmony and this gives me great satisfaction.
I show my clients different combinations of materials, colors, proportions
that are beautiful and look nice.
I am lucky or unlucky, depending on how you look at it,
that my job is my hobby, my passion.
Maybe it's the question of balance and harmony
between work, passion and family life.
I think you find that as you grow older
and I have it now.
BALANCE
I moved here for the views.
Here we had our two children
but before my second child was born
we knew that we wanted to raise a child and work in a nice place
which is inspiring
but also helps us relax and escape from the hustle and bustle.
You know work is work and life is life.
If you took a walk around here, you would see the views
that are best described by the words of Mickiewicz
"I made for the open body of dry ocean's breed".
Wood has been in our lives for many years.
The best moment is when I hear "This is beautiful Mister Kornik".
The smell of plywood is different
when you work with wood in a carpentry shop,
the smell of wood is everywhere
and a real carpentry shop is the one smelling of wood.
I would once say that carpentry is my hobby
but today I sometimes need a break from it.
I have a different passion - motorcycles.
I ride all around Europe.
Today I am going to Warsaw,
tomorrow my daughter has her second birthday
so, I will have to come back from Warsaw to go to her birthday party.
Some things have changed
and today I know how to draw a line.
I try to take part in a family life when I am needed.
I like to take a day off when I want
and organize the work by myself.
Sometimes I don't feel like working so I take a break
to work better and with satisfaction when I feel like it.
I must admit that when I see the finished kitchen and a happy client
because it's his smile that is most important
I am happy myself.
This is a great feeling
because nothing gives as much reinforcement as working for people
as their happiness, satisfaction.
Sometimes in the very evening I get a text from a client instead of a call
saying that they have what they wanted, that this is great
and that moment is very rewarding.
The film was made under the patronage of BLUM POLSKA
starring
and
Thanks to carpenters' families and people involved in the production.
Production commissed by BLUM POLSKA
-------------------------------------------
A Fazenda: Após expulsão de Catia Paganote, Evandro Santo fala o que pensa e dispara - Duration: 4:28.
-------------------------------------------
SUBLIMACIÓN con ROTULADORES Blim Art 🖍️🎨 - Duration: 4:42.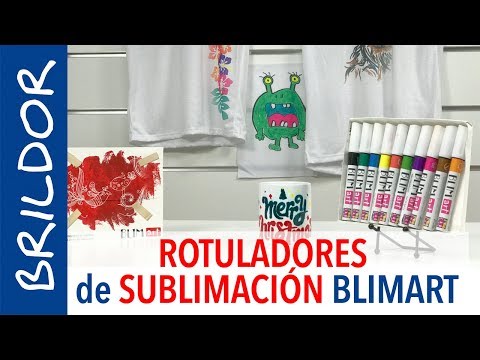
-------------------------------------------
RESSONÂNCIA PSICOBIOFÍSICA - Dr Carlos Carvalho explica o que é - Duration: 25:34.
-------------------------------------------
BOLSONARO RECUA E EMBAIXADA EM JERUSALÉM VIRA ESCRITÓRIO - Duration: 2:49.
-------------------------------------------
EM DEPOIMENTO, PEZÃO NEGA PROPINA E DIZ QUE CONTA ESTÁ 'DESATIVADA' - Duration: 1:56.
-------------------------------------------
DIY How to make candle holder out of pine cone (ENG Subtitles) - Speed up #546 - Duration: 1:34.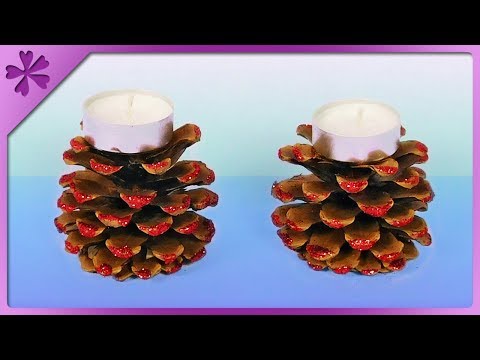
Hi. Today I will show you how to make candle holders out of pine cones.
Detailed list of all needed items is in the description of this video.
Remove a top part of pine cone by using wire cutter.
Apply a glue on all the scales of pine cone.
Now, apply a glitter.
Shake the pine cone to remove an excess of glitter.
Let the glue dry.
Finally, place a tealight candle on top of the pine cone.
And it's done.
These candle holders will looks gorgeous on a Christmas table.
Of course, instead of glitter you can use various small decorations.
I invite you to my channel, Facebook page and Instagram profile.
Thanks for watching. Bye bye.
-------------------------------------------
공무원 1.8% 확률을 뚫어라! - 합격한 자와 포기한 자, 그리고 공부하는 자 - - Duration: 6:53.
-------------------------------------------
Robertsová: Mé neoholené podpaží rozhodně nebylo projevem feminismu - Duration: 9:21.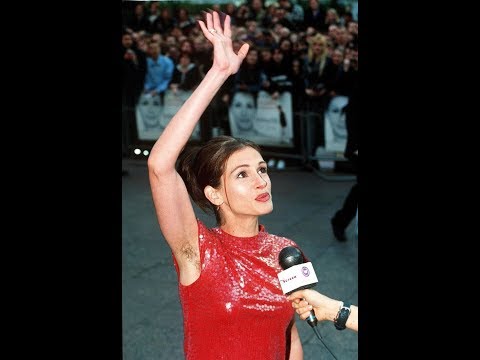
-------------------------------------------
Após reatar relacionamento, Chay Suede compartilha clique fofo de jantar com Laura Neiva - Duration: 1:38.
-------------------------------------------
Miało być drugie 500 plus, jest totalna kompromitacja! Morawiecki pali się ze wstydu - Duration: 5:02.
Mateusz Morawiecki musi przyjmować na swoje barki wszystkie problemy związane z rządami Prawa i Sprawiedliwości
Nie wiadomo jednak, jak długo uda mu się wytrzymać tak wielki ciężar. Właśnie ujawniono zupełną porażkę jednego z największych programów państwowych, który miał stać się tak wielką rewelacją jak 500 plus
Mateusz Morawiecki zdaje się coraz częściej robić dobrą minę do złej gry. Premier mierzy się z kolejnymi kontrowersjami, płynącymi z działań polityków partii rządzącej, które bardzo mocno mogą rzutować na społeczne poparcie
Niestety dla niego, kolejne dni nie zapowiadają się na łatwiejsze. Szczególnie, że nawet doradcy Prezesa Rady Ministrów nie pozostawiają złudzeń co do tego, że najbardziej zuchwały projekt państwowy jest kompletną klapą
Minister ujawnia prywatny, brutalny sekret Kaczyńskiego. Będziecie w szoku Mateusz Morawiecki skompromitował się po raz kolejny? Mieszkanie Plus miało być jedną z tych propozycji, która przyciągnie młodych ludzi do Prawa i Sprawiedliwości
Tak jak 500 plus miał poprawić sytuację młodych polskich rodzin. Perspektywa wejścia w posiadanie własnych czterech kątów przy obniżonych kosztach była bardzo kusząca dla wielu młodych par, które były przerażone rynkowymi cenami mieszkań
Jednak rzeczywistość bardzo brutalnie zweryfikowała realizację całego przedsięwzięcia
Rząd zlecił sporządzenie specjalnego raportu, który miał podsumować dotychczasową realizację Mieszkania Plus
Okazał się on druzgocący dla ekipy Mateusza Morawieckiego, gdyż nawet eksperci powiązani z Prawem i Sprawiedliwością nie pozostawili na projekcie suchej nitki
– W realizacji programu Mieszkanie plus od momentu jego inauguracji w czerwcu 2016 r
popełniono liczne błędy. Częste zmiany koncepcji programu i źle przygotowane przez Ministerstwo Infrastruktury i Budownictwa akty prawne sprawiły, że pierwsze dwa lata jego funkcjonowania należy uznać za stracone – można przeczytać w części raportu opublikowanej na łamach Rzeczpospolitej
Pośród lokatorów największe zastrzeżenie budziły przede wszystkim zmieniane warunki przyznawania lokum oraz wołające o pomstę do nieba realizacja mieszkań
Krzywe podłogi, przeciekające rury, czy wilgotniejące ściany to tylko kilka przykładów
Dodatkowo, już po zamieszkaniu, okazało się, że koszty nie są wcale tak niskie, jak zakładano
DALSZA CZĘŚĆ TEKSTU POD GALERIĄ Pytanie, jakie stawia wielu obserwatorów, dotyczy przede wszystkim tego, czy jeszcze w jakikolwiek sposób da się uratować Mieszkanie Plus przed haniebnym odejściem w niepamięć
Wszystkie najważniejsze decyzje są jednak w rękach Polskiej Federacji Rynku Nieruchomości, która w tym roku jest odpowiedzialna za realizację przedsięwzięcia
Do poprawnego funkcjonowania projektu niezbędne są również zmiany w prawie. Komentujący sprawę eksperci podkreślają, że może być to nie do przeskoczenia znając opieszałość rządu do podejmowania naprawdę ważnych decyzji
Dwie najbardziej kluczowe ustawy powinny zostać uchwalone do końca bieżącego roku, natomiast jedna z nich doczekała się dopiero pierwszego czytania, a druga nawet nie trafiła do Sejmu
ZOBACZ TAKŻE Zobacz również
-------------------------------------------
Fernanda Gentil e Priscila Montandon se casaram em segredo - Duration: 2:53.
-------------------------------------------
Ex de Bruna Marquezine, Neymar teria criado perfil falso para dar em cima de pretendentes - Duration: 11:58.
-------------------------------------------
Rebel - Ben Böyleyim (2018) - Duration: 2:09.
-------------------------------------------
Misato Nonomiya, part 1 - Hots TV - Duration: 3:04.
Thank you all for watching the video. Please subscribe to the channel to support me. have a nice day
No comments:
Post a Comment