I've been working for DBA Group since 2006,
the year it decided to diversify its activities
and embark on its ICT adventure.
When I started, I worked on the first web projects with DBA Lab,
and after a while, I became part of the communications team.
The group really has grown over the years,
along with the demands and the potential of the group's markets.
The communications department is involved with trade shows and events,
as well as organising sponsorships and public relations events.
Working for DBA means doing some soul searching.
It means setting new goals and embracing new challenges.
It means explaining in layman's terms
what the group's different companies do.
It means reaching new goals, and rising above oneself.
This is the most motivating and the most interesting aspect of my work.
Every day brings something new, and no two days are the same.
For more infomation >> #DBAGroup tells its story. CHAPTER 13. The challenges of every day. - Duration: 1:25.-------------------------------------------
Some tips to catch more fish in LRF - Algumas dicas para apanharem mais peixe em LRF - Duration: 9:55.
fish on
hi guys
welcome to another fishing video
This video will be the continuation of the first video made in the Hell's mouth
in Cascais
Will be a didactic video, it will not be a video with very beautiful landscapes
As I did at first despite having some tips
Will be a more didactic video so that you have your captures
To see what I'm doing and catch fish
And get some questions you may have
Let's talk about weight
We have here 5 and 10 grams
And this is fundamental
I've been fishing with 5.8 and 10 grams
However if you can not spend as much
Those of 5 and 10 grams you should have
Because 5 grams allows us to fish in shallower areas
Or when the fish is at the top of the water
While those of 10 grams allow us to look for the fish further away, sometimes the schoolfish moves away
And also allows us to fish in places where the fish is deeper
There were times when I had to use the 10 grams to look for the deeper fish
This is not to say that with a larger lure I will catch bigger fish and with a smaller lure small fish
I will purposely leave the capture of a very small mackerel with the largest lure
So that you see that with a jig of 10 grams you can catch small fish
Has nothing to do with the size of the lure with the size of the fish
Has to do with the distances in which I will look for the fish
And with the depth to which the fish is
I will not look for a fish 4 or 5 meters deep with a small jig
Because I'm going to spend most of the time waiting for the jig to reach depth where the fish is
there he goes
fish on
finally
Pretty mackerel
it will be?
Maybe not mackerel
It's a mackerel
there he goes
fish on
It's a mackerel
and release
In relation to the colors
Each of these sets comes with 3 different colors
we have the white
the pink
and the blue sardine
why?
This allows us to cover various aspects of fishing
I like to use this at night
I like to use the white at night too
I like to use the pink in the begin of the day
And with a single expense I can cover
All situations
fish on
fish on
they are small
fish on
What is this?
It's a bigger mackerel
In relation to decoy
Necessary or not?
This is a question that makes a lot of sense.
When I was fishing there were fishermen by my side who knew how to fish
They were fishing with sardine
And they were also capturing and one of them said
That with the smell of sardines even I could catch fish
well, the sardine smell is bad for us
so don´t fish near people using sardine because the fish will come to eat the small pieces of Sardine and don´t atack the lures
because the fish atack for two reasons
Or because he is hungry
Or because as predator it attacks by reaction
Our instinct to fish
With lures will be trying to have the reaction attack
They attack by hunger but also by reaction
The lure passing through them triggers the attack
If you have a person close and fishing with sardine
The fish will be attracted to the sardine smell
and the fish will look for those small Sardine pieces
And fishermen who fish with sardines manage to catch more
is bad for us fishing with lures, so try to avoid places where are people fishing with natural baits
the fish will look for those small piece of sardine and don´t attack the lures
if you are...
I will cut after
It's amazing
It's the third plane
amazing
so if you find someone fishing
with sardine avoid that place
$&%$&/$% of the fly
-------------------------------------------
LA PESCA delle VONGOLE nel DELTA DEL PO - DigitaLife - Duration: 2:28.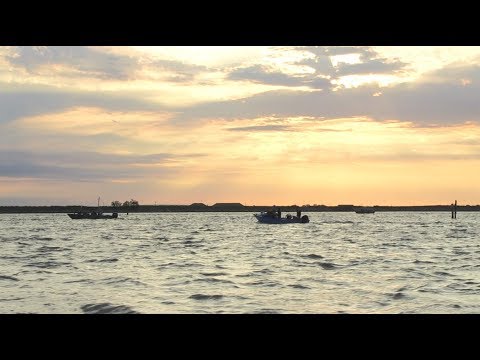
-------------------------------------------
Foca-se na Atividade ou na Produtividade? ERRO #1/25 - Duration: 1:50.
-------------------------------------------
Programa Virando Jurista #1 - Profª Patrícia Rizzo Tomé l Mudanças no Processo de Família - Duration: 19:17.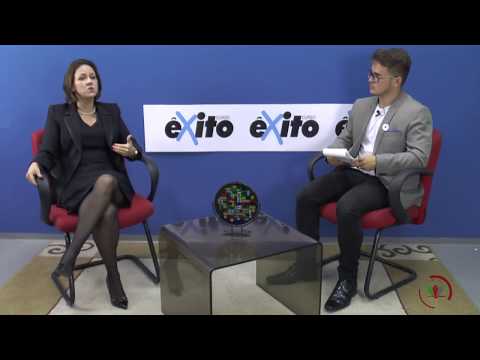
-------------------------------------------
54342 - Duration: 2:51.
-------------------------------------------
TG5 -PROFUGHI STRANIERI OSPITATI DENTRO UNA BASILICA DEI FRATI ( ROMA) - Duration: 1:59.
-------------------------------------------
Valeria Golino seducente con outfit Valentino: ma dimentica qualcosa !! - Duration: 2:28.
-------------------------------------------
JamesPayneDrums.com - Feet Technique: Leg Motion - Duration: 12:02.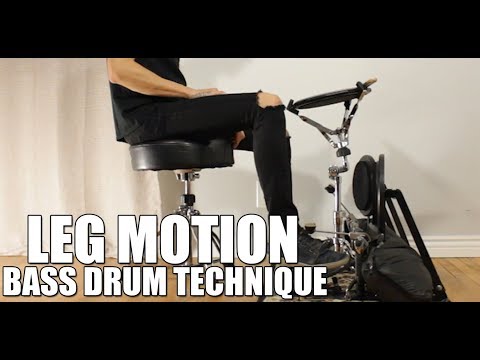
Hi guys, so, this week I want to talk about and study and practice the Leg Motion.
The leg motion, in my opinion, is a very important thing.
Not everybody, actually I think most of the people don't work on the leg motion as they
work on all the other kind of motions that they do.
Especially on ankle motions, sometimes we focus more on the technique it self and not
on what actually starts everything.
In fact, in my opinion, the leg motion is the injection of everything we're going to
do, for example, when we have to play 32nd notes patterns on the drums, for example for
a breakdown, sometimes I see drummers struggling with that part, with the beginning, where
they kind of start in that way and then they get rolling, and they start... being able
to play what they want, but how it should be is that we should be able to start straight
away to play with no problems, and that's possible using the leg motion as the first
stroke.
In fact, if we use the weight of the leg that's actually what happens in the leg motion, it's
using the leg to go against the force of the spring.
The spring is a force that we have to deal with that wants to throw the beater back as
the beater reaches the surface that we're playing on, in this case the pad.
So, from there dealing with this with small muscles like the articulation muscles of the
ankle, it gets difficult, it makes us lose control, and we either have to, kind of, do
a pressing motion, to beat that, or working on the release motion, which is starting already
in a stressed position, in a contracted position, against the spring, putting the weight of
our body in front and working on releasing the pedal, instead of being relaxed, work
with the leg motion and the weight of the leg against the spring and then take advantage
of that, which is what I do.
And this benefits me on staying relaxed the whole time and not putting pressure on the
knees, putting all the weight of my body in front, so on my legs, which damages your knees,
especially in the Swivel technique, and so, for this reason I really think the Leg Motion
is very important, and that 's why I want to start from there and talk about this today.
So, we will structure our lessons starting from the body control, which is practicing
without pedal, practicing just working on our body, and then we will do other steps to get
to the final result, which is playing, of course, the pedal with the spring on.
Basically the leg motion works exactly how the upstroke and downstroke for our hand works,
so we raise our arm leaving our hand relaxed, and we do the same thing with our leg, we
raise our leg in this position and then we just let our arm go, and in the same way,
we let our leg go.
So, what happens is that when we release the leg, when we let it fall, the noise that we hear,
the sound that we hear, it's a Flam sound, it's not a flat sound.
It's not a Tap, but it's a Flam.
Because the toe reaches the floor before the heel, because our ankle is completely relaxed,
so as with the hand, where the fingers are in a lower position thanthe wrist, the same
thing happens with our foot, where the toes are in a lower position compared to the ankle.
So it's exactly the same concept, the same mechanincs that happens, just applied to the
lower part of our body.
And of course this requires us to put all the weight of our body on the seat and not in
front, if not we're going to have hard times doing this motion.
But we're going to talk about balance in another episode, I want to focus on the leg motion
today.
So the first exercise that we have to do, is, we have to raise our leg and make sure
that as we raise the leg our ankle is relaxed and we don't have tensions, we don't do anything
like that... we don't raise our toes, or any kind of contraction or muscular activation
Outside of this part of our leg, which, of course, it's going to work because it's going to raise the leg
So, the same thing has to be done with the left foot of course
And, we can work on this for 60 seconds
for each leg so, 60 seconds right leg, 60 seconds left leg
making sure
that
all our muscles are relaxed while we do this
it's very important to stay concentrated and it's very important to
repeat this exercise for at least the whole week once per day
From the moment that you understand what you have to do, that's just the beginning of your study curse
what happens when we study is, we have to make this kind of feeling
spontaneus and natural everytime we play
so even when we don't think about it, because now we're really focused on this part of our body
so, we can control it and we can let all the muscles relax while we do this
but, will this happen when we're going to play and we're dealing with clicks, the live stage and other situation?
we don't know, we have to keep repeating this so that our brain memorizes this thing
and this message that it sends, and then from there, it's going to be spontaneus, it's going to be natural
so yes, if we repeat it, then our brain will get used to this andwill apply it every time it has to work in this way
so, this is the first thing that we have do to, so working on our body, educating our brain to have this kind of approach
everytime we work in this way
then, we will work on the pedal without the spring
working without the spring is very important because it allows us to work very slowly
and we don't have the pressure and the needs that the spring gives reacting and controlling
the reaction of the spring, but it's just going to be dealing with the rebound
that really depends on how powerful we hit the pad or the surface that we're playing on
we'll have to think about different things in this situation, we have to think of raising our leg without
pressing down, if not we're already going to have a problem, and when we're going to put the spring
we're going to have tensions already, because we're working against the spring so, we'll have to work on
really raising our leg, and then letting it go, keeping the same exact motion that we were doing before
and then we'll have to work on not pressing the beater down but letting it come back
because all these motions are going to be in preparation of the final step, which is working with the spring
so once we can do this, and this is going to be done 60 seconds per leg
both right and left, again, so it's going to be another 2 minutes added
the final step will be to practice with the spring, and we'll have to deal with the sring, so as I was saying
before, we'll have to work with the weight of our leg against the spring
we're going to do the same exact thing that we were doing without the spring, so
raising our leg without pressing the beater down, and then we will let the leg fall
and then we will control the rebound, the come bac of the beater,
just by relaxing the foot and leaving it laid on the board
in this case, this a one leg motion stroke, instead if you want to work on different techniques
anduse the leg motion as the injection, this is what's going to happen:
so, this is why, in my opinion, the leg motion is very important
it's going to be the injection of all the motions that we're going to do and all the techniques
and also, of course, will help us playing slowly and without making any effort
just by working using the weight of the leg working against the force of the spring
and try to work on these motions with these steps at least once a day
and, of course, we're going to go through all the other techniques the I play and perform
this is just going to be the first step of a long way that will take us through all the techniques and all that we are
going to need to play fast with control and power without getting tired
-------------------------------------------
Aqa Meray Qarar Hain - Tanveer Ali Hakim - New Naat Album 2017 - Duration: 4:16.
Aqa Meray Qarar Hain - Tanveer Ali Hakim - New Naat Album 2017
-------------------------------------------
Vatanım Sensin / Wounded Love Trailer - Episode 12 (Eng & Tur Subs) - Duration: 1:03.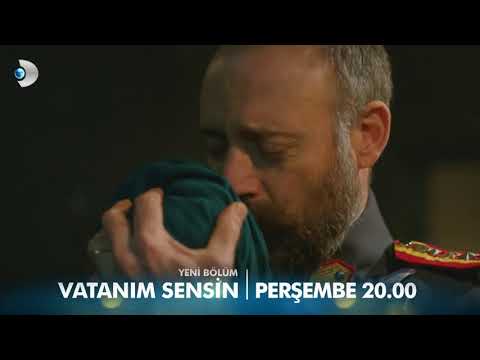
How does love begin in the heart?
When does it grow enough to long for the impossible?
When does this ache runs from the heart to the hands...
...from the knees to the eyes?
Without loving someone, one cannot know how to love a country.
We are not enemies. This is not our war.
The fate of so many periods changed because of a child. Many turned into servants while others became rulers, because of a child.
I will tell her who shot her husband behind his back in Thessalonike, who the real treator is.
Does a heart endure love the same way it endures an invasion and screams of an innocent person?
No!
-------------------------------------------
Zoomer Dino Indominus Rex
-------------------------------------------
Volvo V40 2.0 T2 122PK R-Design - Duration: 0:58.
-------------------------------------------
Volkswagen Tiguan 2.0 TDI DSG * 4-MOTION * R-Line * LED * XENON * - Duration: 0:48.
-------------------------------------------
Help Us: Group Uses Flashlight To Signal To Tv Crew - Duration: 0:21.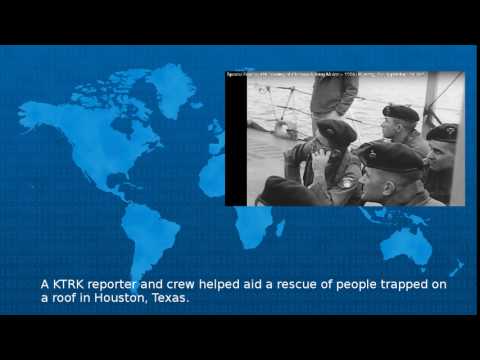
-------------------------------------------
Suzuki Vitara - Duration: 1:07.
-------------------------------------------
Suzuki Vitara - Duration: 1:05.
-------------------------------------------
Word of Truth - Creation
-------------------------------------------
Opel Insignia 2.0 T COSMO Automaat * 139.912 Km * Navi * NIEUWSTAAT * - Duration: 0:59.
-------------------------------------------
Volvo V70 2.0T Summum Navi Bi-Fuel CNG Leder Standkachel 5 Cilinder! - Duration: 0:54.
-------------------------------------------
Alexis Sanchez upset at being replaced after 62 minutes of Arsenal comeback – and don't we know - Duration: 3:26.
Alexis Sanchez upset at being replaced after 62 minutes of Arsenal comeback – and don't we know it
SO that went well then…. Alexis Sanchez started for Arsenal the first time this season at Liverpool but was substituted after 62 minutes. Alexis Sanchez reacts to being substituted by wiping his face on his shirt.
The Chilean was obviously upset at Arsenals 4-0 thumping by Liverpool. And the Gunners were hammered 4-0.
Sanchez, the subject of summer-long transfer speculation, trooped off having put his shirt over his head in resigned mood as he was replaced by Olivier Giroud.
The Chilean had a quiet, ineffective game as Arsenal succumbed to one of the best Liverpool performances in years. After Mohamed Salah had converted Liverpools breakaway third goal, Sanchez slumped to his knees.
Eventually he stood up, shook his head and tried to get into the game. But his efforts were in vain.
A couple of minutes later he trooped off, touched hands with boss Arsene Wenger, and slumped onto the bench. But as he took his place behind the dugout Sanchez was spotted smirking.
Sanchez slumped to his knees after Liverpools third goal.
Soon afterwards he was replaced by Olivier Giroud.
Sanchez walks solemnly past boss Arsene Wenger.
The Arsenal forward was later caught smirking on the bench. This drew the following comment from Sky Sports analyst Gary Neville, who said:.
I doubt hes aware the cameras on him. Not sure what hes smiling about. Then, as the camera panned towards disappointed Arsenal fans, Neville added: Thats more representative of what he should be looking like.
Keep up to date with all the latest news, gossip, rumours and done deals in SunSport's live transfer blog. In the end he departed the scene looking forlorn, knowing he had witnessed two clubs heading in different directions.
Manchester City are very keen to nab Sanchez by Thursdays transfer deadline. The player, at least, has been given further food for thought.
-------------------------------------------
#20 Old CNC Machine Cutting New One From Acetal #20 / Design Upgrade - Duration: 19:28.
In this video I will cut the redesigned plates for my CNC machine using acetal, and begin
the process of replacing the original plywood plates.
I built my CNC machine with plywood plates at first to keep cost down but also as a test
if the design was sturdy and accurate despite the plate material.
I always intended to replace the machine plates with ones made from more durable material,
and I decided to go with acetal, mainly because it would be a lot quicker to cut than aluminium.
My first step was to cut the larger 500mm by 500mm sheet of 12mm thick acetal into smaller
section so they could fit on my current machines waste-board.
I don't have a nesting module on the software that I am using, so I had to do this manually
by moving pieces around within the software until I was happy with the amount of waste.
Ok I've secured it down with three mending brackets. I'm going to drill out the holes
first for each plate that's going to fit on this piece of acetal. And then I'll screw
it down using these cup washers and screws, so each individual piece is held. Then I'll
remove these and cut the remaining cuts out. This method allows me to cut pieces a lot
closer together and without having to worry about larger clamps getting in the way of the toolpaths.
I can't tell how well you can see this but
there's a lot of different size holes. Now what I'm going to do is start securing stuff
down.
One, two, three, four.
I should be able to take these off now. Because I set my origin position at the beginning
I could return to that point, load new gcode files and make follow on cuts – cutting
the plates out in stages. I've secured each piece, so there'll be four
pieces I'll be cutting out from this one block of acetal, with two screws and cup washers each.
Ok it's cut out. Dust has built up. The extraction
isn't as strong as I'd like. Before unscrewing the pieces I check that
all the holes had cut out correctly, and also fitted a few bearings within their allotted
recesses. I also physically check the plates were identical
by placing them over one another. Well it feels like it lines up.
I am cutting the second piece of acetal now. I used the same method of screws and cup washers
to secure the material. It's worth mentioning between cuts I gently sanded any raised bumps
on the MDF wasteboard caused by the screws. This will allow the acetal to lie flat against
the wasteboard. Once this had completed I decided to check
the temperature of the CNC machine by using this laser temperature measurer. I've been
cutting on and off for a couple hours now and well I'm just curious.
It's over thirty. The results are good on the machine and not
too bad in the enclosure considering I haven't put any extra cooling fans inside yet.
I then cut the two sides of the gantry. I didn't redesign this part to use smaller v-wheels.
I'm going to have to clear up the back a little
bit but it's looking really good. Really nice material to work with. If you've never tried
halloumi board I really recommend it. So now I'm going to do this plate here. I
am now cutting the z axis plate. This will be a little more complicated because I am
going to change over to a larger 8mm bit to area clear a trench for the spindle mounting
parts. The spindle mounts will be cut out from a 250 by 250mm sheet of 16mm thick acetal.
I measured this material with a veneer calliper and changed the dimensions of the trenches
to compensate. I added half a mm to this, so the fit won't be super tight. As long
as the trenches are parallel this will help me fit the spindle mounting parts, so the
spindle is square to the plate. Ok here goes, the last cut.
I added half a mm to this, so the fit won't be super tight. As long as the trenches are
parallel this will help me fit the spindle mounting parts, so the spindle is square to
the plate. So that's 16.1mm. That's the same. The depth
is pretty good, it's 2.2mm. Wow, ok that's what I put in. I'm bleeding all over the place.
I should check this piece fits in there. It does that way. But this side here doesn't.
So I can either leave it like this, and make sure I position the cuts so that the pieces
that will fit onto the grooves are on the thinner side, or I can quickly run another
toolpath while I still got the origin set. Let's see what time it is? Do I have the time?
I don't think I've got the time to do that, so what I'm going to do is get some tape.
That's ok, that's ok, that's not ok. Thin, and thick.
Here's the final piece. Now I need to decide what I'm going to do about the spindle mounting
plates, and in particular the hole for the extraction tube. The redesigned files on fusion
360 have this a little further towards the spindle, just to make it look a little more
squat. Obviously if I cut that out I'll have to make the bloody dustshoe. And I'm not sure
I can really be bothered to do that. These are the spindle mounting parts. I decided
to change the location of the extraction port so the dust shoe will also have to change.
Ok I took the first section out coz the tabs didn't hold that well and I was worried they
were going to move around. Lets just test this fits.
I made the openings for the spindle exactly 80mm – but when I originally cut the plywood
plates I had shrunk this by ½ a mm or so. Annoyingly, the spindle is a little loose
now. I don't want to have to re-order new material to cut this out again so what I could
do is either wrap some Kapton tape around the area of the spindle which I'll clamp
against, or glue some neoprene tape onto the smaller clamping section of the mount, although
it's notoriously difficult to glue anything to acetal. I could even drill and tape some
holes through the side of the mounting pieces for flat faced grub screws, which I can use
to tighten against the spindle. It's not ideal but I have subsequently changed the
fusion 360 and DXF files again in case anyone decides to cut these plates out. I'll make
the mistakes so you don't have too.
Before I forget this is a tiny wafer of acetal. An offcut that was left between two of the
parts. I think it was something like that. And I just didn't realise how strong this
material was until I picked this up and instinctively went to snap it, and I just literally cannot
break it. I actually think maybe the thickness of the plates was a bit over kill for how
tough this material is. If this was a bit of mdf or birch ply, just doing that would
break it. I decided that I needed to assemble as many
of the plates sections as I could before I dismantled and upgraded the CNC Machine. If
it turns out I made a mistake along the way, and need to recut something – well it would
be very difficult with the machine in pieces. I am waiting form some new wheels to come
through the post but I was able to use parts from a cbeam linear actuator which I originally
bought to upgrade the xcarve to test the machining and mock up a y plate.
I used my bench vice to push the eccentric spacers into their openings. And for each
wheel I placed either an eccentric or 1/4inch spacer, a precision shim, a wheel and then
a locking nut. I also used washers on the outside of the plate to make sure the machine
screw didn't protrude too far out and potentially scratch the aluminium C beam.
There are two types of wheels – which include Delrin and polycarbonate. Some of the Polycarbonate
wheels actually fractured over time so I prefer to use Delrin.
I'm just looking down the aluminium extrusion, while I turn the eccentric spacer. Essentially
what you want is, to be able to slide the plate along but to stop the wheel turning
if you press your thumb or finger against it. You don't want it any tighter than that
coz then it will start top push the plate and the machine screws out.
What I found originally when I built the first machine, I used larger wheels at the top and
even though I changed the spacing as I saw other people doing them, and as I was advised
I was still not getting the wheels lining up as they should. It just makes more sense
to stick with one type of wheel and to remove that problem from the build.
And the feet lift the y plate high enough so this doesn't get in the way anywhere.
Ok, I though everything was going well and I suddenly noticed that there is an opening
here that's missing. When I tried to work out where this was going to go I ended up
creating a new sketch, and somehow I forgot they were two separate section and I overlooked
it. It's quite faint but I've just cut the outline of this shape so I can pop it on top,
and use that to then do the next cut. That was lucky. It came out quite easily.
All the wheels, and parts and bearing as so on, have arrived. So I'm going to put them
on to the different plates.
To speed up the process I use a vice to press four bearings at a time.
I would do one side first, flip them over, place the precision shim between the two bearings
before completing the wheel assembly.
I then made the z axis plate up next. Annoyingly two of the outer wheels on one side were just
shy of the aluminium extrusion. I think while adjusting the eccentric spacers within the
c-beam the plate shifted ever so slightly – and I didn't anticipate this in the
3d model. I think AVE has a term fort type of tolerance and you're welcome to guess
what it is in the comments section bellow. Let's just say you couldn't cut a slice
of cheese this thin, but you're welcome to try and to send me pictures.
So I had to re-order some more 12mm acetal and I decided to also buy some 16mm as well
to re-cut the spindle mounting parts. So I've just cut a new plate out. The sight
difference is these holes have been spaced in by about 1/2mm each, and that will just
mean the wheels on the eccentric spacer will make contact with the c beam.
That's going to be a problem. I need to counter sink these and use some other machine screws.
Or I could buy some of these low profile machine screws.
I also assembled the gantry. I thought I could make some PTFE washers to
shift one side of wheels across so all sat properly on the aluminium extrusion, but in
practice this resulted in a gap forming on the opposite side. I also tried replacing
the combination of precision shims, spacer and two shims between the wheels with some
3/8 inch or 9.5mm spacer which I had from the x carve, but they weren't any good either.
If I had an engineers lathe I could just make some the correct size but alas, I don't.
I decided I should try assembling as much as I could before I dismantled the CNC machine.
This included cutting out a negative of the smaller spindle mounting part which holds
the extraction tube, which I could use to hold the piece while drilling its mounting holes.
It does feel quite close to the edge but the
holes are only going to be 5mm.
I also drilled the tapped the opposite parts,
including the mounting holes to the z axis plate.
I just put a bit of kapton tape there, and
that's a lot tighter now. If really really go for it, I can twist it but that's pretty
good. There is a little bit of a gap here, I feel like maybe the material opened up a
bit after I cut it? So I took the tape off and it feels pretty good. It's lining up ok.
I mean really it's all about this section here clamping downwards. I would have preferred
it if it was a little bit tighter here. You can see a bit of light.
The top is nice and flat.
No light is coming through.
I didn't realise how translucent this stuff was.
This one I'm going to drill all the way through.
So previously I drilled the holes before tapping with
a 4.2mm bit for the 5mm but this time I'v actually used a 4mm in the pillar drill so
the thread is a little bit more pronounced. One of the m5 clamping machine screws lost
its thread so I had to replace those with M6 bolts. Tapping holes with a drill, even
if you go slowly isn't possibly the best method. Ok that feels good. I was worried the spindle
would be loose in the mount but the bolts applied a lot more pressure than I could by
hand, and it seemed to hold quite well. I'm just putting some 16mm flanged
through this plate and it will hold the z axis.
In next video I will being dismantling the CNC machine with the ply-wood plates and replacing
those with the acetal ones which I've just cut.
As usual don't forget to sacrifice a thumb to the algorithm gods, and let me know your
thoughts in the comment section below. Thanks again.
-------------------------------------------
[스타와 나의 플레이리스트(STAR PLAYLIST)] SUNMI(선미) _ Gashina(가시나) - Duration: 7:58.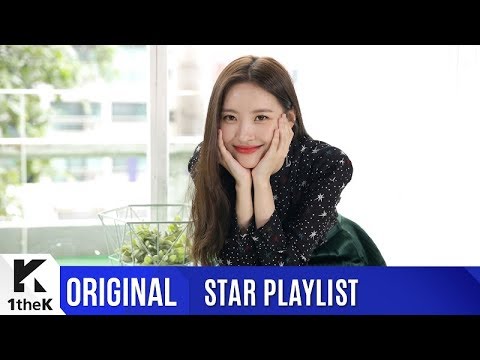
-------------------------------------------
VIP AND WALL MIX Playthrough EP 2 (No savestates) [Subtitle commentary] - Duration: 12:33.
That is some very unfitting music for a cave...
D'oh i missed!
No worries, this isn't the star world. It leads to the yellow switch palace.
Annnd... i screwed up!
Screw your blue block. I have a cape!
Dangit!
Let's continue tr[!]ng hard from here on.
Aw man... (BTW Start selecting out of a level doesn't count as dying.)
NO! That's so cheap... (Btw that doesn't count as dying either. I don't lose a life when i fall here, it just ends the level.)
Ok that wasen't really worth anything other than VIP coins, but i'd still like to show as much as i can from each level.
Uh ok...
Hmm... Maybe i needed the Yoshi?
Great...
Screw it, i'll just do a shelljump.
And NOW the pipe works. ARE YOU SERIOUS?!
What the hell even are those things?
Wow that was a short level. Anyway that's it for this episode.
(I love that name)
-------------------------------------------
Some tips to catch more fish in LRF - Algumas dicas para apanharem mais peixe em LRF - Duration: 9:55.
fish on
hi guys
welcome to another fishing video
This video will be the continuation of the first video made in the Hell's mouth
in Cascais
Will be a didactic video, it will not be a video with very beautiful landscapes
As I did at first despite having some tips
Will be a more didactic video so that you have your captures
To see what I'm doing and catch fish
And get some questions you may have
Let's talk about weight
We have here 5 and 10 grams
And this is fundamental
I've been fishing with 5.8 and 10 grams
However if you can not spend as much
Those of 5 and 10 grams you should have
Because 5 grams allows us to fish in shallower areas
Or when the fish is at the top of the water
While those of 10 grams allow us to look for the fish further away, sometimes the schoolfish moves away
And also allows us to fish in places where the fish is deeper
There were times when I had to use the 10 grams to look for the deeper fish
This is not to say that with a larger lure I will catch bigger fish and with a smaller lure small fish
I will purposely leave the capture of a very small mackerel with the largest lure
So that you see that with a jig of 10 grams you can catch small fish
Has nothing to do with the size of the lure with the size of the fish
Has to do with the distances in which I will look for the fish
And with the depth to which the fish is
I will not look for a fish 4 or 5 meters deep with a small jig
Because I'm going to spend most of the time waiting for the jig to reach depth where the fish is
there he goes
fish on
finally
Pretty mackerel
it will be?
Maybe not mackerel
It's a mackerel
there he goes
fish on
It's a mackerel
and release
In relation to the colors
Each of these sets comes with 3 different colors
we have the white
the pink
and the blue sardine
why?
This allows us to cover various aspects of fishing
I like to use this at night
I like to use the white at night too
I like to use the pink in the begin of the day
And with a single expense I can cover
All situations
fish on
fish on
they are small
fish on
What is this?
It's a bigger mackerel
In relation to decoy
Necessary or not?
This is a question that makes a lot of sense.
When I was fishing there were fishermen by my side who knew how to fish
They were fishing with sardine
And they were also capturing and one of them said
That with the smell of sardines even I could catch fish
well, the sardine smell is bad for us
so don´t fish near people using sardine because the fish will come to eat the small pieces of Sardine and don´t atack the lures
because the fish atack for two reasons
Or because he is hungry
Or because as predator it attacks by reaction
Our instinct to fish
With lures will be trying to have the reaction attack
They attack by hunger but also by reaction
The lure passing through them triggers the attack
If you have a person close and fishing with sardine
The fish will be attracted to the sardine smell
and the fish will look for those small Sardine pieces
And fishermen who fish with sardines manage to catch more
is bad for us fishing with lures, so try to avoid places where are people fishing with natural baits
the fish will look for those small piece of sardine and don´t attack the lures
if you are...
I will cut after
It's amazing
It's the third plane
amazing
so if you find someone fishing
with sardine avoid that place
$&%$&/$% of the fly
-------------------------------------------
Old Goa | Must Visit Churches | Wandering Minds VLOGS | Day 9 - Duration: 6:20.
-------------------------------------------
[ENG] Amazing! BJ Ban Li Na's healthy hot body "A man who supports BJ" [oh Hot] - KoonTV - Duration: 1:44.
"Have I ever been to BJ Ban li na's broadcast?"
Naturally started 'A man who supports BJ'
As soon as we watch her, our eyes feel cleansed
" Today's outfit is also hot"
figure show time
Oh! figure show!!
The queen of figure!!
Eyes full of instinct
"Will she join competition?"
"Great!"
First, cover eyes
Watching mode
Can't keep...
"Big thing in somewhere"
Oh my...
What a perfect body!
That makes you forgot your say
'Sexy' can't express all of feeling about her body
unbelievable
amazing
fantastic
It looks like her body is getting better
firm thigh
fatal charming makes
insane brain
In the end
Perfect back
Finished show time
Thanks a lot to Koon
Koon is no.1!
Very satisfied
Thank you
Nice
-------------------------------------------
How to get a Free iPhone 7 2017.Reality exposed??? - Duration: 5:00.
-------------------------------------------
How's Socialism Doing in Venezuela? - Duration: 5:31.
Once there was a South American country with a promising future.
It had a functioning democracy, a rapidly developing economy, and a growing middle class.
All the important indicators, including education, health care, and foreign investment,
were pointed in the right direction.
It was far from perfect, but the mood was hopeful – and with good reason.
But now all that promise is gone.
The country is a failed state, a hollowed-out shell of its former self.
Services like power and water are sporadic.
The most basic consumer goods, from bread to toilet paper, are in chronically short supply.
Crime has skyrocketed.
Freedom of the press is almost non-existent.
Democracy has been replaced by a virtual dictatorship.
The country is, I'm sorry to say, my beloved Venezuela, a place in which my family has deep roots.
I can tell you what happened to it in one word: socialism.
In 1999, then-candidate for president Hugo Chavez promised to lead the people of Venezuela
to a socialist paradise.
His theme was "Esperanza y Cambio" – "Hope and Change."
"Venezuela is a nation of great wealth," Chavez said, "but it's being stolen from
its citizens by the evil capitalists and the evil corporations."
This wrong would be righted, he assured the voters, if they elected him.
And they did.
To their everlasting regret.
Chavez drew inspiration from his mentor, Fidel Castro.
Like his mentor, he enjoyed giving speeches – some that lasted as many as seven hours!
He even gave himself his own weekly television show where he would spontaneously break into song.
Here's a rule: When your nation's leader starts singing on national television,
you're in trouble.
Under Chavez, the government of Venezuela took over industry after industry.
The government, he assured everyone, would run these businesses better than private enterprise,
and the profits would be "shared" by the people.
With great fanfare, he tore up contracts with multinational oil and gas companies and demanded
that they pay much higher royalties.
When they refused, he told them to leave.
They did.
His image was burnished by Hollywood celebrities who flocked to see the great work he was doing
– taking money from the rich and giving it to the poor.
Progressive politicians from the US and Europe also praised him lavishly.
Here's another rule: When Hollywood celebrities visit your country to praise your leader,
you're in trouble.
When the leader sings on national television and is praised by Hollywood celebrities,
you're doomed.
Socialism always works in the beginning, so people are fooled...in the beginning.
It's easy for governments to confiscate money, but eventually
there's no more money to confiscate.
In the case of Venezuela, I mean that literally: People who could get money out of the country, did.
Many left the country altogether – nearly 2 million, according to Venezuelan sociologist
Tomás Páez.
The wealth creators continued to create wealth, but they created it somewhere else
– Miami or Madrid and other places around the world.
When Chavez first ran for President in 1999, he said he would leave in two years
if people weren't happy with him.
But, like Castro, Chavez never had any intention of giving up power.
He died in office in 2013, replaced by his vice president, Nicolas Maduro.
Maduro is Chavez without the charisma or the voice.
The country is now a pariah, shunned by the world and isolated.
It's so bad that many international airlines refuse to fly there.
People stand in lines for hours just to get food.
Sometimes they walk away empty-handed.
A recent survey found that 75 percent of Venezuelan adults lost weight in 2016
– an average of 19 pounds.
This national weight-loss program is known cynically as "the Maduro diet."
Still, Maduro holds onto power.
Opposition leaders and journalists who report the truth are jailed.
Venezuela is a cautionary tale.
Once a country goes down a socialist path, there's no easy way back.
And the longer a country stays socialist, the harder it is to reform it.
Venezuela has been socialist for two decades.
If you don't think it can happen here, whether "here" is the United States or Europe
or anywhere else, you're fooling yourself.
When people get used to depending on the government – no matter how poor they remain
– that dependency is hard to break.
That's why you should never buy the socialist lie.
Socialism is a drug.
And like a drug, it feels great – at first.
But eventually it will ruin your country.
Just like it ruined Venezuela.
I'm Debbie D'Souza for Prager University.
-------------------------------------------
VatanımSensin / Wounded Love Trailer - Episode 13 (Eng & Tur Subs) - Duration: 0:53.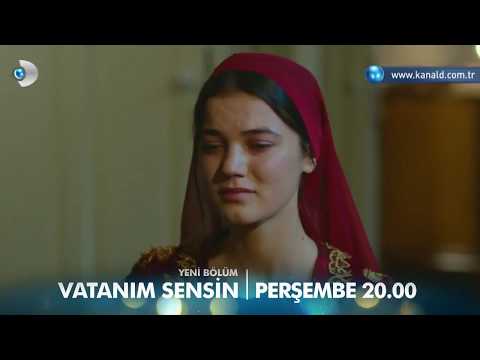
Who are you?
Cevdet?
This issue has become very interesting, Lieutenant.
Do you except Cevdet and Azize's daugther Yıldız as your wife?
Surround the house!
I said open the door!
Stop!
Is a Greek lieutenant that hates the Turks concerned about a Turkish girl's life?
Don't be decieved by the sweet words of the enemy, There might be poison inside the honey, Sadi said.
From the true antagonist illimitable courage is transmitted to you, Kafka said.
Mom, I swear I didn't know that this would happen.
Mom, stop!
Untie me!
-------------------------------------------
Vatanım Sensin / Wounded Love Trailer - Episode 12 (Eng & Tur Subs) - Duration: 1:03.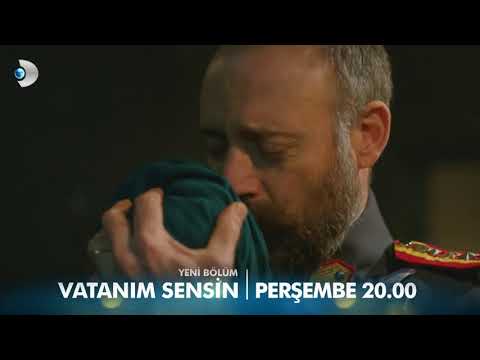
How does love begin in the heart?
When does it grow enough to long for the impossible?
When does this ache runs from the heart to the hands...
...from the knees to the eyes?
Without loving someone, one cannot know how to love a country.
We are not enemies. This is not our war.
The fate of so many periods changed because of a child. Many turned into servants while others became rulers, because of a child.
I will tell her who shot her husband behind his back in Thessalonike, who the real treator is.
Does a heart endure love the same way it endures an invasion and screams of an innocent person?
No!
-------------------------------------------
WHAT IN MY ISRAEL FRIEND POUCH ?! [ENG&한국어자막] - Duration: 5:32.
-------------------------------------------
Econo - C - Duration: 3:44.
-------------------------------------------
Fancy a BAC Mono but can't fit inside? There's good news - Duration: 2:55.
Fancy a BAC Mono but can't fit inside? There's good news
The BAC Mono: a futuristic single-seat supercar that looks like a formula racing car and goes like one too. What's not to like? Well, possibly its overly cosy interior, which some drivers might find a touch snug, even for one.
From summer 2016 on, however, the Liverpool-built machine has been redesigned with a new, slightly wider chassis to free up a little extra hip 'n' shoulder room.
Certain outer members of the tubular steel chassis have been moved outwards, and the body's side panels have been made a little slimmer.
In all, there's an extra 56mm of wriggle room; 25mm from each side of the chassis, and 3mm from the new panels.
The Mono's still the same size on the outside, those stunning exterior dimensions remaining the same overall. Kerbweight, a featherweight 580kg, hasn't changed either.
So the Mono's 305bhp 2.5-litre Mountune four-pot can still push it from 0-60mph in 2.8sec and on to 170mph flat-out.
The changes have been made as a result of feedback from customers, says BAC co-founder Ian Briggs: 'Every change we make to the Mono is aimed at improving it for our customers, and this upgrade is intended to make the most of the space for the driver.
Thanks to the close relationship we enjoy with our customers, we are in regular dialogue with them and this change has come as a result of this.'. Seems the rest of the world is catching on to the Mono's charms.
Since its original launch in 2011 the BAC has been steadily exported to multiple countries worldwide, and further new markets in America and the Far East are on the agenda for 2016.
Good news for thrill-seeking sports car fans the world over, then – even ones with big elbows.
-------------------------------------------
Explosm Presents:Channelate - Fight 快樂氰化物小禮物 決鬥 中文翻譯 - Duration: 1:28.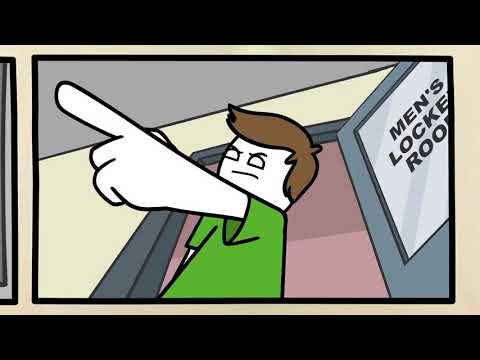
-------------------------------------------
ThatPoppy-Interweb(FULL SONG) - Duration: 4:21.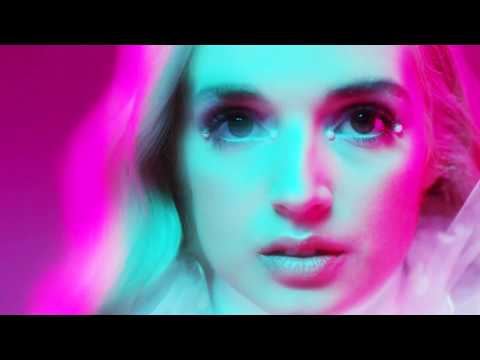
No comments:
Post a Comment