ANCHOR: This month's Research on EXID, I'm with Ahn Hee-Jin. Welcome. REPORTER: Good evening.
ANCHOR: So EXID will be only active for three weeks, do we know what will happen starting May? Has there been any news story?
REPORTER: A news of EXID's comeback on September 2017 has been circling around online media. As we researched, turns out that is not true.
A news article stated that EXID Hani mentioned of September comeback on SBS Radio Cultwo Show
but as our staff listened to the entire show, none of the EXID members mentioned about their next comeback.
NCHOR: I see, so a reporter assumed a lot. Can we guess when their next comeback will be?
REPORTER: That's correct. Most K-Leggos think either October or November for the next comeback
Probably because EXID Solji will return in this summer as solo.
If Solji only publishes her song and not go on to music shows, EXID could theoretically comeback by September.
Ah Yeah came out in April, and Hot Pink was released in November, so many Leggos thinks it will be similar in 2017 too.
ANCHOR: I see. What will EXID do before their next comeback?
REPORTER: Of course EXID will be on TV shows and go on live music stages in Korea as usual, but there will also be quite a bit of international concerts.
They already planned for Canada in May and for Japan in this summer.
According to several sources, EXID is planning a couple more international concerts as well.
In January 2016, Producer Shinsadong Tiger stated that "EXID will stay in Korea for 2016, but they will start going abroad in 2017,"
REPORTER: ...and it seems like that is quite likely. ANCHOR: This has been Reporter Ahn Hee-Jin. Thank you very much.
For more infomation >> [K/E/J/S/V/T] 2017년 4월 읷순탐구생활 (This Month's Research on EXID) - Duration: 1:28.-------------------------------------------
[K/E/J/S/V/T] EXID 활동기 3주로 줄어 (EXID's Comeback Reduced to Three Weeks) - Duration: 1:05.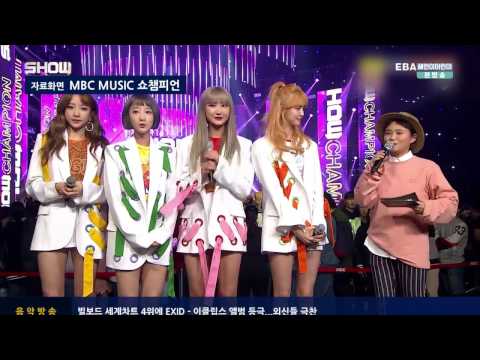
Good evening.
As the Presidential Election in Korea is only a couple of weeks away, EXID forces to stop their comeback a week earlier than planned.
None of the music shows will be aired on the first week of May, HYELINIKID's Ahn Hee-Jin has more.
It is anticipated that music shows will not be aired on the first week of May. Because the election is on May 9,
all TV stations will air special TV programs on the election instead of music shows.
KBS Music Bank, SNS Ingigayo, MBC MUSIC Show Champion, MNet MCountDown are officially postponed,
while MBC is still thinking about postponing Show! Music Core.
According to staff at TV stations, it is likely that music shows may not air on the second week of May too.
This may heat the competition for this week even more as many idols try to be on TV as much as they can. Some groups coming back on May are even postponing their comeback until early June.
Let's see what Banana Culture has planned as EXID unexpectedly stops performing.
This is HYELINIKID news, Ahn Hee-Jin.
-------------------------------------------
[K/E/J/S/V/T] EXID 1등 실패 졌잘싸 (EXID's Performance on 3rd Week of April) - Duration: 0:50.
It seems like winning the first place became even more difficult with shorter period of comeback.
K-Leggos, however, are still hopeful for this week. HYELINIKID's Ahn Hee-Jin has more.
It's only after the first week that the ranking is counted. EXID's ranking started on April 18
unfortunately, EXID had to remain 2nd place on the first day.
EXID was still on the 2nd place on the following day, and on the 3rd place on last Thursday.
Second or third places are not bad as Leggos have anticipated a tough battle,
but some of them can't help being disappointed as the score gap between EXID and the first place was little.
As APink's Jeong Eunji stops her comeback last Sunday, Leggos are hopeful to win the first place.
This is the last week for EXID, and the members need Leggo's help more than ever. This is HYELINIKID, Ahn Hee-Jin.
-------------------------------------------
Manteiga de Amendoim - Duration: 3:42.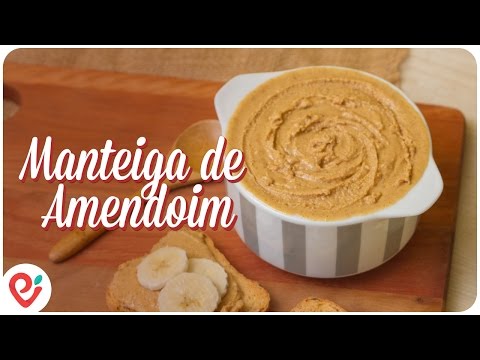
-------------------------------------------
Fantasy Myst Opens Advanced Capsules - Taked Entei, Orangurus and Misdreavus - Duration: 5:51.
Hello and welcome back video channeler
Today we will see how it goes together
opening the capsules advanced
purchased with gems gained
struggled in recent weeks
I hope that i can take some legendary pokemon
Here is ready ...
3 ....
2 ....
1 ....
Let's go
Awesome, I took Entei, one of the legendary monsters
and also a beautiful Oranguro
Here are all the prizes taken here
the extraction went very well
Entei is spectacular, I can not wait to try it
For my team it is great,
especially against electric
And 'one of the strongest fire pokemon
until now when I faced him I always feared
I am so glad now on my side
That's my team what it looks like now
Raikou already know,
you have seen in my previous video
I see that is a friend of Entei, we create the bond between them
For now it is not much, but it is already a little something
over time and the increase of Entei friendship,
the bonus will increase
Tyrantrum is still the best of the team
Then we Charizard, Raichu
Sceptile and so on.
Let's look for newcomers
Here, finally, Entei
Start to grow it,
because I want to use it as soon as possible
We create the link with Raikou
Again, for now the bonus is small,
but it will grow over time
Here we have another new pokemon
We can tie him to Golduck
It has no other changes, so it is already at the maximum level
evolution
But return back to Entei
Potentiated the friendship level to unlock his skills
and increase the stats
I speed video at this juncture
to do not it boring
That's unlocked the first three skills
for me the bulldoze is the best
of his skills
Give them also the equipment
We continue with the increase friendship
to unlock other abilities
Unlocked even the fiery abilities
with attack on all enemies
Now we improve the actual statistics
Lock those who believe that they should not change
I try to optimize the skills, although it is not easy
I might already be satisfied
But they're undecided whether to increase the attack and speed
I would say leave things at the moment
A few days later I tried again back luck
New opening of the capsules
I'll be lucky like the first time?
In a moment we'll know
Great I took a Misdreavus
a psychic pokemon
and a Onix
And this little guy, I'd still
already taken in the past and evolved
I would say that the first extraction was better
Psychic Pokemon can be useful
but no legendary
Let search for the new monster
Here's our new friend
Its evolution is often the meeting
and I have to say that it can be dangerous
And since there are I show you how
my team has grown in the meantime
Raikou has become my best pokemon
and Entei has risen in the fourth position and use it often
instead of Tyrantrum
If you enjoyed the video put the "Like" the video
and subscribe to the channel
Hello and the next video ....
-------------------------------------------
GUARDIÕES DA GALÁXIA 2 | REVIEW (SEM SPOILERS) - Duration: 10:29.
-------------------------------------------
Produtos Licenciados - Novidades Hong Kong Electronics Fair - Duration: 3:50.
-------------------------------------------
N O O D L E S . E X E - Duration: 3:26.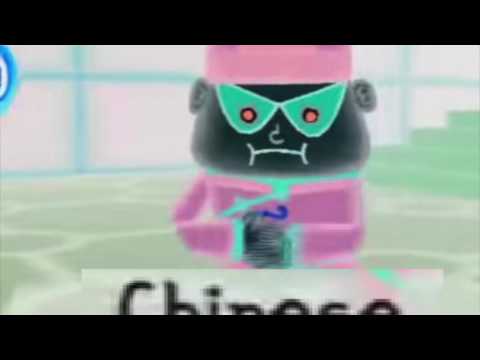
this took like 5 minutes to make why is it louder
-------------------------------------------
Joseph Smith the Younger Talent Show Performance - Duration: 4:00.
How does a young boy, farmer, son of the Smiths Joe and Lucy,
walk in the middle of an untrodden spot amongst a grove of trees
by kneeling and appealing as he saw fit, grow up to be a hero and a prophet?
The boy prophet, like his father was not a scholar Got a lot farther by pondering much harder
By questioning those smarter, by being a self-starter By fourteen. They placed him on track to become a martyr.
And every day while souls were being scattered abandoned to sway, They're tossed in waves, he knowingly kept his guard up.
Inside, he was longing for something to be a part of. The brother was ready to kneel, pray, ask God and ponder
Then a darkness overcame, as the devil tried to claim Our man saw his future drip, dripping down the drain.
But a new light gave him fight, two personas bright as flames, And one called out his name, a testimony gained.
Well, the word got around, they say, this kid is insane, man. Tells the other churches they got pieces, not the whole plan.
Preach out this glad message, and to everyone proclaim. And the world is gonna know your name. What's your name, man?
Joseph Smith the younger. My name is Joseph Smith the younger.
And I'm sent to share this book with you. This can't wait, this can't wait.
He gave us fruits that we can test, we needn't guess, the bible hinted. Few years later, see Joseph and the Book of Mormon's printed.
Instead, of just using the bible to end on. The Book of Mormon clarifies some doctrines we depend on.
Establishing the church, same church we had in ages past. Guided by the spirit, the Mormons start growing super-fast.
A voice saying Joseph, you can't do this by yourself. He started calling missionaries, crossing continental shelves.
This book is about a people who wanted to follow God. A compass showed them where to trod, hold tight to that iron rod.
Built a ship just to skip from the old world to the promised land. All while dealing with some brothers that would never lend a hand
Writing on all of the plates they could get their hands on. Telling of the future of the continent they stand on.
They're the other sheep who were not of that land. Passed along on golden plates from Mormon's hand.
Nephites Came to the promised land (This can't wait) They built up cities in the promised land (This can't wait)
The Savior came to this promised land This new book (Blue book) This can't wait.
Joseph Smith the Younger We are forever in debt to you.
You would never back down. Why did they take you in your prime?
Oh, Joseph Smith the younger, When the whole world sings for you,
Will they know what you sacrificed? Will they take Moroni's advice?
The world will never be the same. (oh)
The mob is in the Jailhouse now, That door is not gon' stop 'em.
With faces painted black they stop in just to pop 'im.
His enemies destroyed his rep but we have not forgot him.
We followed him Me, I died with him Me, I trusted him Me, I loved him
And them, They're the dumb fools that shot him.
But I came to share this book with you And it can't wait
What's your name, man? Joseph Smith the younger!
-------------------------------------------
CONTA ENCERRADA NO YOUTUBE - O QUE FAZER??? - Duration: 2:15.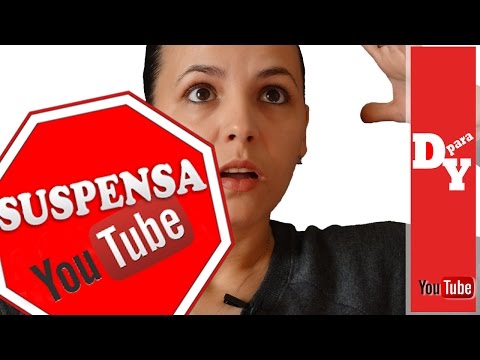
-------------------------------------------
Top 10 ANIMALS That Are No Longer ENDANGERED - Duration: 13:12.
Top 10 ANIMALS That Are No Longer ENDANGERED
These days, it's easy to feel like the world is a depressing place where nothing good ever
happens.
Bombs explode, wars trundle on, politics gets more polarized, and the future looks as black
as can be.
No wonder we wake up each morning reaching for the Xanax.
But not everything has to be a non-stop horror show of mind-numbing misery.
In the shadows of the natural world, far away from where headline writers' prying eyes
can glimpse them, a number of animals have been undergoing a remarkable resurgence.
Even as we devastate the environment in places like Indonesia and China, we humans have gradually
been helping select species tiptoe back from the edge of extinction.
Desperately need proof that not everything is doom and gloom?
Look no further.
10.
The Giant Panda (No Longer Endangered: 2016)
The giant panda is the poster boy for endangered animals.
Literally.
The World Wildlife Fund (WWF) use an image of a panda in their logo.
Know what else the giant panda is?
Not even close to going extinct.
As of September 2016, the most-famous endangered animal on the planet is no longer actually
endangered.
When the WWF first picked the panda for their logo in 1961, the species had nearly vanished.
Although a handful of wild pandas remained, they were so rare conservations had no idea
how many were actually left.
It took decades to reverse their decline.
First, poaching had to be cracked down on, before some douchenozzle hunter could blow
away the last panda in the hope of making a quick buck.
Second, a whole load of wildlife reserves had to be set up to protect their habitat.
China today has 67 panda reserves, protecting 14,000 square kilometers of habitat.
Thanks to all this effort, panda populations have been growing at an encouraging rate.
By 2004, there were around 1,500 living in the wild.
Fast forward to today, and that number is over 2,000.
While the giant panda is still on the 'vulnerable' list, it is thankfully no longer teetering
on the brink of extinction.
9.
Chatham Petrel (No Longer Endangered: 2015)
90 percent of you just saw the name 'Chatham Petrel' and said something along the lines
of "Whaaaaaa?"
The remaining ten percent are from New Zealand and know exactly what we're talking about.
A bird species native to the remote Chatham Islands, an archipelago some 650 kilometers
east of Wellington, the petrel is found nowhere else on Earth.
And that's a problem, because the Chatham Islands have a new kid on the block: the broad
billed prion.
If you don't know the prion already, it's the kind of hipster-bird that likes to rock
up in a neighborhood, scoop up all the affordable property, and probably open a craft beer joint
or two.
But while human hipsters doing this merely breed resentment, the prion leaves the petrel
nowhere else to go but the grave.
With its nesting sites stolen, the petrel dies.
It dies so hard that, in 1995, its population numbers dropped to a mere 600.
Thankfully, New Zealand's birders are nothing if not inventive.
Faced with this looming petrelgeddon, they simply gathered the birds up, took them to
a new island without prions, and left them there to get on with it.
As of 2015, the petrel's numbers were sufficiently restored to downgrade it from endangered to
vulnerable.
8.
Louisiana Black Bear (No Longer Endangered: 2015)
It's not often that we celebrate the survival of a murder machine that could tear us limb
from limb, but the Louisiana Black Bear is different.
For one thing, it's a unique subspecies that's celebrated as the state animal.
For another, it also gave us a template for children's plush toys for decades to come.
The Louisiana Black Bear is where we got the name "teddy bear" from.
This is thanks to a now largely-forgotten incident involving President Theodore Roosevelt.
In 1902, Roosevelt decided he was gonna shoot a black bear in rural Mississippi.
Roping in an expert bear killer named Holt Collier, who had killed over 3,000 bears,
the President set off on a hunt that lasted a stupid amount of time.
With Roosevelt unable to find a bear, his assistants eventually got hold of an injured
one, tied it to a tree, and invited the President to shoot it.
Roosevelt refused, saying it was unsportsmanlike.
When news of the incident reached the capitol, a cartoonist for the Washington Post drew
an image of the President refusing to shoot an adorable, fluffy little creature.
The public went nuts for the image, leading to sales of toys based on it.
The teddy bear was born.
Nonetheless, the Louisiana bear itself nearly went extinct.
In 1992, only 150 remained in the wild.
Two decades of conservation efforts have since boosted the population to over 700.
7.
Delmarva Peninsula Fox Squirrel (No Longer Endangered: 2015)
In 1967, the Federal Government passed something known as the Endangered Species Preservation
Act.
The first legislation of its kind in the US, the act required states to list animals in
danger of dying out and make some kind of effort to save them.
Consisting of 77 animals, the original list read like a roll call of the nearly-dead and
dying of America's fauna.
Near the very top of it sat the Delmarva Peninsula fox squirrel.
A large gray squirrel, the fox squirrel had been led to the brink of extinction by intense
logging and overhunting.
By the time it was protected in 1967, its range had dropped to 10 percent of what it
had once been.
Its survival chances weren't helped by the fact that its habitat was almost entirely
on private land, and stretched over 3 different states (Maryland, Delaware and Virginia).
If there's one thing harder than herding cats, it's getting home owners in three
different states to turn their lives upside down just to save a tree-based rodent.
Yet that's exactly what happened.
After nearly five decades of concerted effort, fox squirrel numbers had bloomed to over 20,000.
They now inhabit 28 percent of the peninsula, and are expanding all the time.
6.
Steller Sea Lion (No Longer Endangered: 2013)
On the cold, rocky shores of western Alaska, lives one of America's greatest native creatures.
The Steller Sea Lion is a huge beast, a gigantic mess of blubber and fur bigger and blubberier
than even yo momma.
Able to range down as far as central California – a distance we decided is best expressed
as a lot – it's a species that is impressive in every sense of the word.
Yet it wasn't always this way.
As recently as 1990, the National Ocean and Atmospheric Administration (NOAA) was convinced
the steller sea lion was about to go extinct.
At the time, the Steller Sea Lion population had been hit hard by centuries of hunting,
repeated environmental disasters, and crashes with trawler ships (which hit them hard enough
to turn them into mulch).
It also seemed unlikely they'd ever recover.
When an animal lands on the NOAA Fisheries endangered list, it generally only comes off
by actually going extinct.
Prior to 2013, only one species had ever recovered enough to be removed, when the North Pacific
gray whale unexpectedly bounced back in 1994.
Well, to that small list, we can now add the Steller Sea Lion.
In 1979, there were only 18,000 left.
By 2010, there were over 70,000.
With the population growing by over 4% each year, it seems likely that the Steller Sea
Lion has now been permanently saved from extinction.
5.
Arabian Oryx (No Longer Endangered: 2011)
The Arabian Oryx has the dubious distinction of being the only animal on our list to have
actually gone extinct.
In 1972, some nameless jerk took his rifle and shot the last one, killing the entire
species stone dead.
And that was it for the grand, stately beast that had once ruled the vast desert wastes
of the Arabian peninsula.
Or, at least, it should have been.
But, for once, fate was smiling on a dying species.
As the population dwindled, a few ultra-rich princes in Saudi Arabia, Qatar, and Abu Dhabi
had taken a handful of the beasts to keep as curiosities in their royal collections.
At the time, this probably seemed like a total douche move to those trying to preserve the
wild population.
But with all wild oryx dead, having a few spare in captivity no longer seemed such a
bad idea.
In 1982, Oman created a special reserve to get these oryx breeding again.
Fast forward to today, and there are now over 1,000 oryx living in the wild.
It probably helped that the oryx was a symbol of ancient significance on the Arabian peninsula.
Long used for their ability to smell water from several kilometers away, it was seen
as a matter of regional pride to revive the noble creature.
We doubt this would've been the case if it had been the Arabian Fartworm that wound
up going extinct.
4.
Lake Erie Water Snake (No Longer Endangered: 2011)
The turnaround in the fortunes of the Lake Erie Water Snake is nothing short of incredible.
In 1999, it was considered so endangered that the US Fish and Wildlife Service listed it
as on the brink of extinction.
By 2011, a mere 12 years later, its population had rebounded enough to remove it from the
list altogether.
That's such a crazy-quick recovery that we almost feel like a mistake must've been
made somewhere.
Native to Lake Erie (duh), the Lake Erie water snake has the double-misfortune of living
near wasteful humans, and looking like a nightmare monster that people instinctively want to
kill.
Honestly, the number one reason the FWS listed for its plummeting population was humans seeing
it, freaking out, and killing it with anything they had to hand.
Yet, despite looking like something that comes crawling out a newly-opened vault in the final
act of a horror film, the Lake Erie water snake is actually pretty harmless.
Just don't go putting anything dangling and sensitive in their mouths and you should
be fine.
3.
Gray Wolf (No Longer Endangered: 2011)
So now we come to probably the most-controversial cast member in our little eco-review, the
North American gray wolf.
A proud creature that roams the back forests of the USA, the gray wolf was placed on the
endangered list way back in the 1970s, and stayed there for the next 35 years.
In 2011, the US FWS announced that the wolf had rebounded, with over 5,500 now living
in the contiguous United States.
It was at this point that things really began to heat up.
The declassification of the gray wolf was contingent on the FWS reclassifying eastern
gray wolves as a separate species.
However, a scientific study claimed that there was no evidence to back this up.
Things grew quite heated; to the extent that an argument about species sub-classifications
can ever be said to get heated (like, we're pretty sure blows weren't exchanged).
This scientific spat aside, it's beyond doubt that the gray wolf has seen something
of a resurgence.
Once hunted almost to extinction, they are now finally creeping back into the forests
of the USA.
2.
Brown Pelican (No Longer Endangered: 2009)
From the point of view of the Brown Pelican, the entire mid-20th century was little more
than a protracted attempt by human beings to kill all its relatives off as quickly as
possible.
As pesticides became more and more common in the US, farmers and government workers
began spraying just about everything that moved with DDT.
Harmful to humans, DDT was nothing short of an apocalypse for brown pelicans.
The poor birds ate poisoned fish, got sick, and died with alarming rapidity.
Those that survived started laying eggs with thin, useless shells.
These shells cracked at the slightest movement, killing the unborn chicks inside.
As a direct result of this global pesticide party, the brown pelican's population numbers
went into a tailspin.
By 1970, they were endangered.
Thankfully for humans and pelicans alike, the use of DDT became pretty taboo by the
mid-70s.
Eventually, the US banned it altogether, with the sole exception of using it to combat malaria.
Its habitat no longer coated with poisonous chemicals, the brown pelican was able to rebound.
Finally, in 2009, the FWS removed it from the endangered list altogether.
1.
Indian Rhino (No Longer Endangered: 2008)
A few centuries ago, life was looking pretty sweet for the Indian rhinoceros.
The great beast roamed the entire north of the subcontinent, from modern Pakistan to
Bangladesh, via Bhutan.
They numbered in the hundreds of thousands, if not the millions.
They were big, impressive, and seemingly unstoppable.
Then, in the early years of the 20th century, big game hunters decided they'd make perfect
trophies.
Within 70 years, this once-robust population had been reduced to a mere 600.
Come 1975, the rhino was extinct in Bangladesh and Bhutan, and going that way in India.
It was only by a phenomenal effort that the decline was stopped before they were wiped
out altogether.
Habitat protection and anti-hunting laws were beefed up, and heavy penalties brought in
for any poachers caught trying to bag themselves a rhino.
For a while, things were tough.
But, eventually, they began to improve.
By 2008, the rhino population was back at 3,000.
Not exactly staggering, but a heck of a lot better than 600.
-------------------------------------------
Audi Q2 - Duration: 1:09.
-------------------------------------------
Entrada da Noiva | Beethoven 9ª Sinfonia Ode à Alegria | Capela São Francisco de Assis - Duration: 1:47.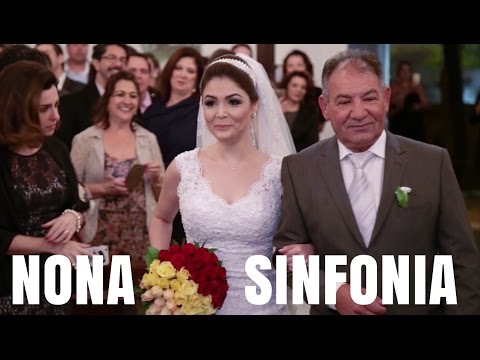
-------------------------------------------
Seat Ibiza - Duration: 1:07.
-------------------------------------------
VW Passat - Duration: 1:08.
-------------------------------------------
How to create transparent 3D prints! - Duration: 13:04.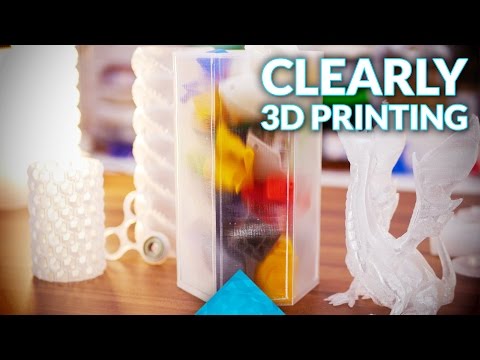
I wanted to make something clear, but the problem is that typical 3D prints, even if
you use clear filament, just come out milky white tone instead of being properly clear.
They diffract light too much, so while the light still passes though, it gets bounced
around inside the parts and scatters, which creates that translucent, but not quite transparent
look.
But Colorfabb have had this article online for a while where they are showing off incredibly,
impressively clear prints.
I've done a lot of printing and I think I'm ready to show you how to reproduce these
prints yourself.
Okay, let's see, Colorfabb were using their HT filament for this, which is Eastman's
Tritan, so I believe it's the same material that Taulman used to make, just plainly called
Tritan, too.
But the key here is that it's a copolyester, so a material that is very closely related
to the common PET and PETG materials.
In general, those are plastics that like to fuse together extremely well, so they turn
into one solid piece of material instead of keeping those layer marks when you look through
the print.
I do have the Colorfabb HT filament here, but I wanted to see how well just a standard
PETG would do, so I did all my experiments with the inexpensive DAS FILAMENT PETG, but
I'm sure any other clear polyester filament is going to work basically the same for this.
I had two different use cases here, the first one being these solid parts like Colorfabb
showed that just look like they are one single, solid block of plastic with basically invisible
layer lines on the inside and outside, at least that was the goal, the other one being
vase-like structures that have no infill, but only provide a shell, in my case, to scatter
light.
I was specifically looking into this for use as diffusers for lamps of various types.
And I think I pretty much achieved that.
But let's start with the solid parts.
My test subject here is a spur gear from Daniel Noree's OpenRC F1 design, it's got some
relatively complex surfaces on the side, large flat areas on the top and bottom and this
hub that is a bit of a smaller element where you'll be able to see the light shine through
from the top and the sides.
I know, it's not the most realistic design for something that's supposed to look good,
but I think it's a great object to tune in the process.
Plus, I've now clearly got plenty of spares for when I start building my first OpenRC
models!
I'll probably reprint these from ABS or Taulman 910, though.
So the first print was done with settings that I thought would make sense - I used 300
and 350µ layers, 100% infill and regular temperatures.
But if you look at the part printed with those settings, it is translucent, but it is not
transparent.
Yes, you can take a flashlight and shine it through and the part will glow, but it's not
nearly as transparent as the samples Colorfabb showed.
So the first idea was to increase flow, to close what looked like tiny gaps between the
extrusion lines, so I upped the extrusion rate to 105% first, and seeing that that improved
things a bit I tried again at 110%.
And if you compare the original part at 100% flow and the new one at 110% it is already
a lot more transparent, but we can also see that it's starting to show over extrusion
streaking on the top surface.
So at this point, the amount of material seems like its correctly filling every gap, but
the rest of the print settings could probably still use some work.
So I tried the other extreme, going with 50µ layers, and that immediately helped a lot.
I think because the hotend now passes over the same spots more often and sorta irons
down the tracks more, we're fusing the individual extrusion lines together more tightly to turn
them into an actual, single block of material.
In fact, if you look at this hub part that I accidentally broke in half, you can see
that both the surface where it broke and the inside of the part look like one single piece
of PETG, looking at just the crack, you'd be hard-pressed to tell this thing was 3D
printed at all.
So next up, I tried increasing the material flow on the 50µ prints and increasing the
layer height from 50µ to 100µ, and both improved transparency a bit.
The 100µ print was done with more perimeters, so you can see how those scatter light differently
than solid criss-cross infill, but overall it didn't look like that different from
the 50µ prints other than the top surface being a bit less smooth and now looking more
like it was overextruded..
The 50µ prints with more material I think were the best ones of the entire series, where
the one with a total of 15% extra material looks, I think, extremely good, while the
one with 20% extra is a bit too much and started to get quite messy on the top and side.
It also has these fuzzies between the gear teeth where the nozzle was scraping off the
extra material on each layer.
For some reason, at the time I thought the 100µ prints were pretty much just as good
as 50µ ones, so I kept on printing parts with that setting.
Looking back, I probably should have stuck with 50µ.
Anyways, these two benchies were printed with 110% flowrate, but this one got a bit of a
temperature boost, hoping that would help with everything fusing together.
But instead, it turned out that the higher temperature actually decreased the clarity
of the part and had a few other negative effects on quality.
It's a bit easier to see what exactly is happening when you look at the gears that
used different temperatures , and you can see that, with a higher temperature, the PETG
actually sorta starts cooking and bubbling, and we'll see that effect again in a second.
In the main section of the gears, the higher temperature is fine and slightly improves
clarity, but up here at the hub, where the printer slows down so that it doesn't pump
too much molten plastic onto one area in too short of a timeframe, up here you can see
the plastic getting extremely cloudy.
That's because when the printer slows down, the filaments is sitting in the heated zone
of the hotend longer and gets more time to heat up, cook and degrade.
So to avoid that, either disable the cooling slowdown in the slicer or just print at a
lower temperature overall.
I think this Benchy does look really good and shows off the transparency or translucency
really well, but it's most visible when you look at the top and bottom of the parts,
since it's almost like the low layer height makes the side surface somewhat milky.
Maybe I should try with an even lower layer height at some point, 10µ or something, but
I'm pretty sure the Prusa i3 MK2 is not up for that without dropping in a new extruder
and some lower-pitch Z-axis spindles.
The stock setup has a physical resolution of 20µ, considering that the half-step position
is the only microstepping angle you can really trust.
But let's get back to these parts.
I also tried to improve the surface by either flame polishing it with a hot air gun set
to 600°C or sanding it beforehand, but with the hot air gun, this unsanded spinner started
bubbling and softening up before it started getting more transparent, so that part's
gone, and when I tried to sand a part beforehand, yes, it did ultimately get a bit clearer,
I think, after I heated the surface that was sanded to 1200 grit, but again, it's really
hard to find that optimum spot where the plastic neither bubbles nor softens up too much.
But one nice thing you can do with heat, actually for any filament, is to melt off the little
hairs that PETG in particular likes to pull when the hotend moves from one area to the
next.
High heat and a single pass are usually enough to take care of them.
And one last approach that didn't really work with the Benchy was the thicker layers
at 300µ, even with the extrusion multiplier cranked up, it did not turn out transparent
at all.
Though print quality overall was a bit more consistent compared to the low-layer-height
parts.
So to recap for solid prints: With polyester filament, use a low layer height, 100% infill,
obviously, and tune the extrusion multiplier so that you're getting maybe a tiny bit
of overextrusion.
Higher temperatures can help, but it's really easy to cook your filament that way.
Post-processing prints to improve the surface is hard to do right, at least with heat.
Maybe those thick coatings can help here, I've played around with spray-on clearcoats
before, but they didn't improve things at all.
Awesome, let's check out how these parts were printed.
These are all single-wall parts, most of these you could print with vase mode, which is a
print mode that turns the entire print into one long extrusion line, instead of having
discrete layers, it just continuously keeps moving the hotend up as it lays down plastic,
so it's one long spiral.
However, this shroud does have a ridge up here, which usually can't be printed cleanly
with vase mode.
But that's not the point here.
Let's start out with what makes these parts look better or worse than others, and essentially
it's the same thing again.
It's refraction wherever light transitions from one medium into another, and here, that's
from the air into the plastic and back out.
The layers act as tiny lenses because they have that round section on their end.
That's why this part right here will blur things in the vertical direction, but not
as much horizontally.
For example with this shroud, I tried to use that effect and create tiny microlenses that
would also diffuse light horizontally because this is supposed to be a diffuser for a lamp.
You know, you have these individual LEDs and just seeing each one through a clear shroud
doesn't make for a very attractive lighting setup, so I have all these parts that create
different diffusion patterns.
Most of these were printed with 300µ layers, because if you compare it to the the one printed
at 100µ, they are so much clearer and crisper and less hazy white.
Of course, using thick layers and only a thin shell like this means that these parts print
incredibly quickly and use very little material.
This one was printed with just 25g of PETG in 45 minutes, that's hard to beat.
This little one I printed with a thicker extrusion width.
But I can tell you one thing that doesn't work, and that is leaving the printer at over
600% speed for the wrong file, I mean, it did get the print done super fast, but clearly,
it's not quite what I wanted.
So typically, with a .4mm nozzle, you're going to set it up to lay down like 0.42mm
wide tracks.
Here, I went with a full mm, so two and a half times as wide as the nozzle, and while
it's not the greatest thing to do if you want overhangs and details to come out great,
I mean, you should be using a thicker nozzle, this part still came out looking great.
It's not quite as clear, instead it's very glossy if that's the right word, but
that might be due to the structure, too.
It's definitely better than using two individual perimeters, which would introduce that second
interface where you'd potentially end up with more diffraction.
Also, it's very strong and stiff, as expected, but I did crack the bottom when I tried to
remove it from the PEI bed, PETG, as usual, likes to stick to PEI a bit too much, so usually,
I'd recommend using a liquid surface finish on top of the PEI that doesn't stick quite
as much, so something like Printafix, or Magigoo, or maybe Glue Stick if you can apply it evenly.
But this technique of just using a single wall isn't great for every model.
This Adalinda frog does come out really nice looking with those thick layers, but wherever
there's a slope on the surface, the extrusion lines just get super droopy, like on the back,
near the tail or on the wings.
I did configure this print with two solid layers on top and bottom and turned off any
features that backfill surfaces, which would avoid these exact issues, but would also create
these structures on the inside that just don't look great if you see the way they diffract
light shining through it.
Alternatively, you could print it with a solid infill and thin layers, but that would use
up a lot of material and take a long, long time to print.
So that's how I printed these transparent / translucent parts.
I think they turned out great, especially these single-wall prints, they are going to
look awesome installed somewhere with some light in them.
If you learned something, click that thumbs up, get subscribed if you aren't already
and whether you've freshly subscribed or have been for a year or two, check that you
have that bell toggled so that YouTube sends you notifications as soon as a new video gets
uploaded.
Kickbacks from affiliate links help me run this channel, so if you want to try printing
some clear stuff, too, there are is a link to ColorFabb's HT material that will take
you to the right shop for your region, also, to the DAS FILAMENT PETG, that's not an
affiliate link, I just like the material, it's cheap, it consistently prints well,
what more could you want.
If you're going to be shopping on Aliexpress, Matterhackers, Amazon, eBay or iGo3D, check
out the shop links to them from the video description.
Or if you want to directly support what I'm doing here, head over to Patreon to chip in
a dollar or two per month, or more, I'm not going to judge you, that is always appreciated
and you'll be invited to join an exclusive live Q&A hangout as well.
So thanks for watching, and I'll see you in the next one.
-------------------------------------------
VW T6 Multivan - Duration: 1:03.
-------------------------------------------
VW T6 Multivan - Duration: 1:07.
-------------------------------------------
Burst City (1982) Sogo Ishii [COMPLETO SUB ITA] - Duration: 1:56:29.
-------------------------------------------
Jaguar F-Pace 2.0d R-Sport Automaat AWD - Duration: 1:08.
-------------------------------------------
Fiat 500C 0.9 TwinAir Lounge - Duration: 1:02.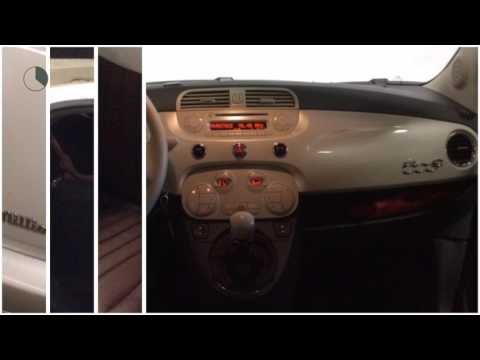
-------------------------------------------
[K/E/J/S/V/T] 2017년 4월 읷순탐구생활 (This Month's Research on EXID) - Duration: 1:28.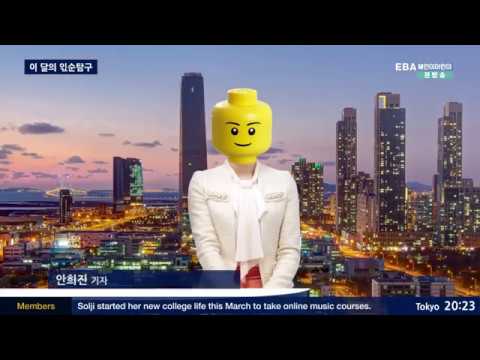
ANCHOR: This month's Research on EXID, I'm with Ahn Hee-Jin. Welcome. REPORTER: Good evening.
ANCHOR: So EXID will be only active for three weeks, do we know what will happen starting May? Has there been any news story?
REPORTER: A news of EXID's comeback on September 2017 has been circling around online media. As we researched, turns out that is not true.
A news article stated that EXID Hani mentioned of September comeback on SBS Radio Cultwo Show
but as our staff listened to the entire show, none of the EXID members mentioned about their next comeback.
NCHOR: I see, so a reporter assumed a lot. Can we guess when their next comeback will be?
REPORTER: That's correct. Most K-Leggos think either October or November for the next comeback
Probably because EXID Solji will return in this summer as solo.
If Solji only publishes her song and not go on to music shows, EXID could theoretically comeback by September.
Ah Yeah came out in April, and Hot Pink was released in November, so many Leggos thinks it will be similar in 2017 too.
ANCHOR: I see. What will EXID do before their next comeback?
REPORTER: Of course EXID will be on TV shows and go on live music stages in Korea as usual, but there will also be quite a bit of international concerts.
They already planned for Canada in May and for Japan in this summer.
According to several sources, EXID is planning a couple more international concerts as well.
In January 2016, Producer Shinsadong Tiger stated that "EXID will stay in Korea for 2016, but they will start going abroad in 2017,"
REPORTER: ...and it seems like that is quite likely. ANCHOR: This has been Reporter Ahn Hee-Jin. Thank you very much.
-------------------------------------------
[K/E/J/S/V/T] EXID 활동기 3주로 줄어 (EXID's Comeback Reduced to Three Weeks) - Duration: 1:05.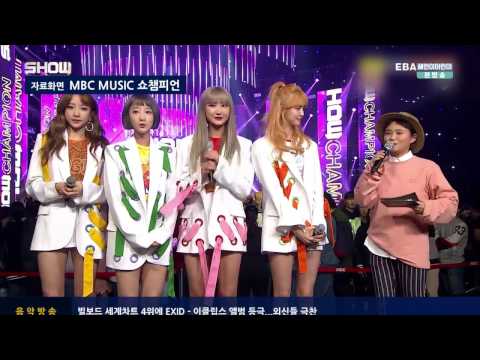
Good evening.
As the Presidential Election in Korea is only a couple of weeks away, EXID forces to stop their comeback a week earlier than planned.
None of the music shows will be aired on the first week of May, HYELINIKID's Ahn Hee-Jin has more.
It is anticipated that music shows will not be aired on the first week of May. Because the election is on May 9,
all TV stations will air special TV programs on the election instead of music shows.
KBS Music Bank, SNS Ingigayo, MBC MUSIC Show Champion, MNet MCountDown are officially postponed,
while MBC is still thinking about postponing Show! Music Core.
According to staff at TV stations, it is likely that music shows may not air on the second week of May too.
This may heat the competition for this week even more as many idols try to be on TV as much as they can. Some groups coming back on May are even postponing their comeback until early June.
Let's see what Banana Culture has planned as EXID unexpectedly stops performing.
This is HYELINIKID news, Ahn Hee-Jin.
-------------------------------------------
[K/E/J/S/V/T] EXID 1등 실패 졌잘싸 (EXID's Performance on 3rd Week of April) - Duration: 0:50.
It seems like winning the first place became even more difficult with shorter period of comeback.
K-Leggos, however, are still hopeful for this week. HYELINIKID's Ahn Hee-Jin has more.
It's only after the first week that the ranking is counted. EXID's ranking started on April 18
unfortunately, EXID had to remain 2nd place on the first day.
EXID was still on the 2nd place on the following day, and on the 3rd place on last Thursday.
Second or third places are not bad as Leggos have anticipated a tough battle,
but some of them can't help being disappointed as the score gap between EXID and the first place was little.
As APink's Jeong Eunji stops her comeback last Sunday, Leggos are hopeful to win the first place.
This is the last week for EXID, and the members need Leggo's help more than ever. This is HYELINIKID, Ahn Hee-Jin.
-------------------------------------------
Opel Insignia Sports Tourer 1.6 T Bns Edition - Duration: 1:02.
-------------------------------------------
Kia cee'd Sportswagon 1.0 T-GDi GT-Line NIEUW! - Duration: 0:59.
-------------------------------------------
5 Lamelo Ball MIXTAPE MOVES, Ankle Breakers & Crossover Combos! - Duration: 4:43.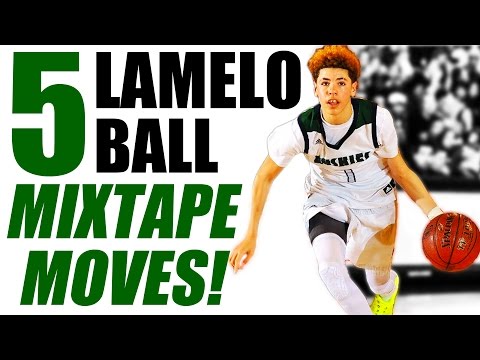
5 Lamelo Ball MIXTAPE MOVES, Ankle Breakers & CRAZY Crossover Combos!
want to learn how to do some of them LOL
balls craziest crossovers and ankle
breaking moves straight out of his
mixtapes I'm going to show you how to do
exactly that hey coach Jesse mincha with
get handle calm make sure you stay tuned
to the very end of the video I'm gonna
have a way for you to take your handles
to the next level very quickly okay the
first move is a behind-the-back snatch
back into a hesitation crossover so
basically what you want to do for this
is make sure you get some good momentum
going attack the basket hard and quick
and then stop on a dime with a behind
the back neither just stopped completely
and hesitate or you can step back a
little bit more I notice when Ramona
doesn't he does a little bit of a step
back just to create a little separation
and then kind of hesitation puts his
eyes of the rim or he'll just even just
scared up hesitate look at his defender
to kind of see what they're going to do
if you had that hesitation in and you
put that pause in there get your
defender to come out towards you a lot
of times on that hesitation and since
you had them flying this way they're
going to come back towards you this way
boom you come this way so they're going
that way as you go this way attack hard
next back behind the back little
hesitation crossover back forward second
move i see lamellas doing a ton it's
pretty common in the NBA for a lot of
the better ball handler reviews as well
Kyrie Steph Curry use this a lot LML
users in a lot of different ways between
the legs and behind the back couple key
point first of all the behind the back
should happen like the instant the
basketball touches the hand from the
between the legs so what soon as the
ball gets here boom you want to push it
almost right away from time to time you
might want to switch up the time and
kind of hesitate and go into it but most
of the time when I feel them LOL do it
it's real quick so the second such as
his hands boom he's pushing it across
right away again you can use this a lot
of different weight your defenders a
little close to you and you have the
angle to get past them you want to push
a little more forward but sometimes
they'll see him do it a little bit more
as a side steps to get a three-point
shot or he'll even do it more as a
complete step back do me a solid if
you're finding these breakdowns helpful
make sure you hit that like button for
me third move is the run of stutter step
hesitation cause I thought him do this
in one of his mixtapes he's coming up
the court pretty good speed going and
you know basically be going fast and
then kind of stutter steps to slow down
and add a little hesitation and then
cross with the hesitation you want to
kind of make it seem like you're about
to go up for a shot these are pretty
good
tutor soul defenders are going to bite
on that right you have to be at least
somewhat of a threat at shooting in
order to get the defender to freeze up
or jump out at you staying on the tips
of your toes moving those feet quick and
then from there kind of act like you're
setting up to the shot with a quick
freeze and then crossing over and if you
want you can even add a little extra
take out this way a little something
extra to it but really the key is a
ticket offender to either freeze up or
jump ball on that shot attempt crossover
and be no okay these next two movies are
pretty crazy this one is going to be a
double behind the back which you might
have seen like Kyrie or even Jamal
Crawford used before I think I like
about the way lamella does it so it
still mix up how he goes into the behind
the second behind the back so basically
it's just going to be behind the back
behind the back right couple key tip
it's going to be a lot like the between
the legs behind the back when it gets to
the hand from the first behind the back
you want to push it across right away
now again though he'll do this different
ways and there's a couple different ways
you can do your behind the back there's
more of the you know pound dribble
behind the back when you're more
stationary and then there's more of the
rap behind the back where you push it a
little more quote he'll make stuff what
he'll do for that second behind the back
again allow him to create different
angles much like he does but between the
legs behind the back he'll either come
inside stuff to get separation for a
shot or will even step back a little bit
with it or he'll do more of that rap
behind the back to push the ball forward
and beat his defender you got to read
the situation if you feel like they're
real tight to you and you can get past
them great opportunity to do that deal
if you can get them to bite on this fake
coming that way it might be a good
opportunity to create size separation
for a jump shot or two step back real
quick leave me a comment down below let
me know which one of these moves is your
favorite so far and let me know what
other players you want to see me break
down on this channel and this move is
extra crazy might not be something your
coach wants to see from you and you also
got to be careful with how you do is to
make sure you don't get called for a
travel it's inside out between the legs
and then hopping to the side as you're
going behind the back hand off so inside
out popping to the side and going up for
the shot hand comes over the top of the
ball push it between the legs keep
dipping give you the tap the inside of
your leg that will make sure the
basketball ends up in the same spot
every time you get a nice consistent
durable if you want to start hopping to
the side as it touches that hand and
pulling the ball behind the back so
click back angle try to get both free
throw in on the ground at the same time
will allow you to get up in that shot
right away
bonus video helpful make sure you click
that subscribe button and get on that
notification squats you catch the newest
tips tutorials and drills the second
they come out and the extra thing I told
you I was going to have you to help you
go next level it's a free workout click
this link right here pop in your email
and also let you right away for free
three health thousands of players and it
will definitely help you to also make
sure you check out this video file like
that one as well check out this playlist
thanks for watching stay tuned for more
make moves today
5 Lamelo Ball MIXTAPE MOVES, Ankle Breakers & CRAZY Crossover Combos!
-------------------------------------------
N O O D L E S . E X E - Duration: 3:26.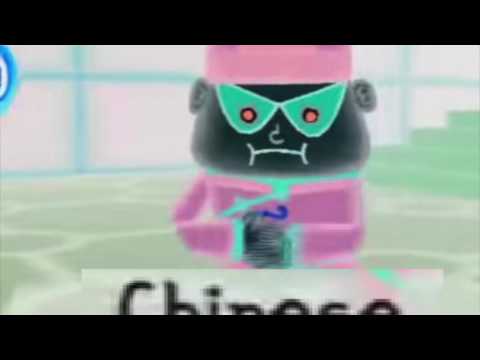
this took like 5 minutes to make why is it louder
-------------------------------------------
Elvis Presley (Captioned) Unchained Melody - Duration: 3:27.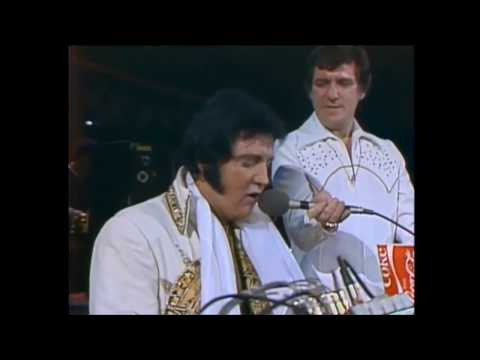
Oh, my love
my darling
I've hungered for your touch
A long, lonely time
Time goes by
so slowly
And time can do so much
Are you
still mine
I need your love oooohh
I need your love
God speed your love
to me
Lonely rivers flow
To the sea, to the sea
To the open arms
of the sea
Lonely rivers cry
"Wait for me, wait for me"
I'll be coming home
wait for me
My love
my darling
I've hungered for your touch
A long, lonely time
Time goes by
so slowly
And time can do so much
Are you still mine?
I need your love oohh
I need your love
God speed your love
to me
-------------------------------------------
It Bears Repeating - Duration: 1:19.
I got something to say.
Mafuckers
that call themselves Christians
a lot of time…
just use Christianity,
God and the Bible
to…
be bigoted,
And...
to pass judgment,
when they, themselves aren't even living up to
what they... profess to... be-
lieve,
and what they confess, PROFESS to have
as…
right and wrong.
And it's like my rhyme says:
You cannot put a number on a sin just cuz you paint.
Write the number on YOUR jail cell.
Jesus saved me just like you!
Why would i then let you tell me what EYE can and cannot do.
It always bears repeating. Really.. we
can't do nothing more than that.
-------------------------------------------
Ro School Killing Game (48) - Duration: 0:32.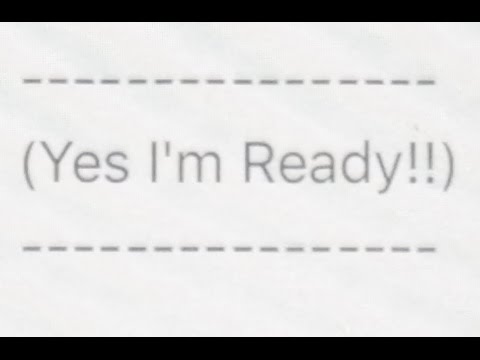
Remember do not make any mistakes otherwise you'll have to start over. Be careful of which character counters. They will support you but you have to help them!
-------------------------------------------
✅ SKULL JACK O'LANTERN makeup tutorial WOLFE FX body paint (Speed-painting) in 4k- Witte Artistry - Duration: 1:40.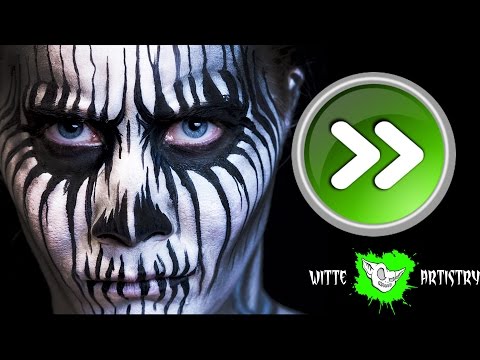
*Humming*
Da DUH!
Strawberries were a good choice.
-------------------------------------------
How To Increase Audience Engagement On YouTube - 6 Key Steps - Duration: 6:52.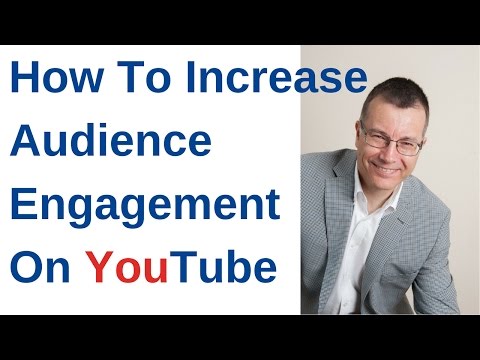
Ever wondered why engaging with your
YouTube audience is so important and
then once you've figured that out how you
actually engage with your YouTube
audience? If you stay to the end of this
video you will have an opportunity to
download a list of a free internet
marketing tools that you should find
of use to you in your own online
business. In the mean time if you'd like
more videos from Video Cashflow on video
marketing and business tips, tactics,
techniques and strategies, please hit the
Subscribe button now.
For now though, let's go back to
increasing audience engagement on
YouTube. Hi, it's Jeff Laming for Video Cashflow
here. So how do you increase
engagement with your audience on YouTube?
Before we answer that question,
let's look at why engagement with your
audience is so important. If you're
looking to use YouTube as a platform to
generate and divert traffic to your
website or onto your email list, for
example, then your videos need to be
ranked on page one for all of your main
keywords - or certainly, as many as
possible. Anything other than ranking on
page one is not necessarily a disaster,
but bear in mind that most people don't
look beyond page one. With that in
mind, to get your videos ranked on page one
you need to satisfy certain criteria
that YouTube use to measure the worth,
or the value, each video provides to its
viewers. Now, one overriding thing to
remember with YouTube is that it is as
much a social media platform as it is a
search engine and that's what makes
YouTube so unique and fascinating. That
means from the "social" perspective,
YouTube measures this value by noting
how "social" the videos are. In other words,
how engaging is the content within the
video? It follows, therefore, that for videos
to be engaging YouTube have to measure
this ie the "sociability" of a video, if
you like. And the one major way of
measuring "sociability" is the length of
time viewers watch a video before
leaving it. It's called the average watch
time, and so it follows, therefore, that to
increase the average watch time of a
video you need to improve the way that
the video engages
with its audience. There's six main ways
that you can increase engagement. Before
we go into these six ways I'd just like to
thank Jason LeDuc of Evil Genius
Leadership Consultants - his YouTube
channel is underneath this video - and
Nick Nimmin who has produced a great
video entitled "How To Increase YouTube
Engagement And Subscribers". Again, the
link is shown underneath this video. Okay
then, so the six ways to increase
audience engagement on YouTube are: Number one:
Plan and research the content
that you will provide in your video. Now, this
is basically determining your subject
matter and then researching the main
keywords.
I recommend up to 10 to use.
Using keywords that are likely to be
searched on YouTube (and Google) will
boost the ranking of your videos,
certainly improving the chances of ranking
those videos. Number 2: Providing good and/
or better quality content. Now, if you can
provide content that is of value to
the viewer,
whether that's answering specific
questions; or providing detailed
solutions; or just providing relevant
information that enables them to move on,
then that will help you in the following
ways: (1) firstly it will improve the watch
time of your videos, and as watch time is
a key performance indicator of social
integration, your video rankings will be
boosted; (2) secondly, it will help enhance
your reputation as a "go-to" person for
further information and help; and (3) thirdly,
increasing your Subscriber numbers enabling
YouTube to promote your new and
existing videos to viewers as a
"recommended to watch" video or
"recommended viewing". Number 3, the third
tip - when you upload a video always start
a conversation in the Comments section by
posting or posing a question - something
that invites viewers to respond to with
an answer. And then respond to their
answer with another question. This way
you're building momentum; you're helping
to keep viewers engaged; and more
engagement improves your video ranking.
Number 4. A -S - K. Yes, "ask" your audience to Like
Your videos; to Share your videos with
friends, family, business colleagues and
associates;
ask them to Comment on your video, in
particular invite your audience to pose
questions about the video subject matter
or a related subject matter; and lastly
invite them or ask them to Subscribe to
your channel so that they can access
further videos on your subject matter.
In addition, and this is something
highlighted by Nick Nimmin in his video,
you need to give your audience a reason
to Like, Share, Comment and Subscribe.
Number five (5) Show a Call To Action in
the early part of your video. You
need to balance this with keeping the
audience engaged with the video that
they're watching against sending them
elsewhere with the Call To Action. So why
is this an issue? Well, if you check your
YouTube analytics you will see that
virtually all videos show watch time
tailing off the longer the video plays,
so one way to counter this is to keep
those viewers who may otherwise leave
within the first 10 seconds or so to
continue watching. So one way to
do this is to advise the viewer that if
they continue watching the video until
the end they'll be able to access a free
download such as a guide, a cheat sheet
or top 10 tips or something like that. Again,
the purpose of this tactic is to improve
the average watch time of your video.
That brings us to item number 6. Organize your
YouTube channel into Playlists. The
purpose of Playlists is two-fold. The first thing is
that playlists themselves get ranked on
YouTube and, secondly, the videos within
the Playlists run into one another, so it
helps keep viewers engaged (and combats
the problem of another unrelated video
taking away their attention) and all of
this increases average watch time. So
there you have it. Now don't forget to
download the free checklist of internet
marketing tools. You'll find the URL link
underneath this video here. And if you
liked the video please click the Like
button, again, underneath this video; feel
free to Share this video with friends,
family, business colleagues and
associates; and please comment in the
Comments section below as well as asking a
question or just to say "hello" and I'll get
back to you as soon as possible. And then
finally, please click the Subscribe
button to get more videos from video
cash-flow on video marketing and
business tips, tactics, techniques, and
strategies that will help you with your
own online business journey. Iin the
meantime, thanks ever so much for watching
this video.
Let's catch up on the next one. Bye for
now.
No comments:
Post a Comment