I'm assuming this is working too loud sound good cool okay my name is todd blatt
I have a presentation about crowd-sourced 3d printing that I want to
show you I want to tell you a little bit about myself and what I do I run a
company called custom 3d stuff we are based in Baltimore so it was a easy trip
for me to get here I started it in 2011 I've been making 3d design since 97 I've
been doing 3d printing since 2004 and then I started my company in 2011
officially I make a lot of jewelry so a lot of these 3d printed earrings
and shapes that you couldn't make other ways outside of traditional outside of
3d printing I make a lot of Star Wars props movie prop replicas for collectors
and these aren't like just desktop FTM prints they're usually a high-end made
from at the actual metal or the real parts that they use when they made the
movie props so this is like the the ring that Rose Tico had in the last Jedi and
the you know all the way down to the disassembling the mechanical iris that
they used and casting the band in brass and chemical etching the the faceplate
so it really functions I do short runs of projects for
collectors so this is the ring from the Twin Peaks to TV show they commissioned
me to make rings for the new stuff for the new show so it was the actual
filming and then I made some of these for collectors this is a cast bronze
polished ring from Doctor Strange and I made a whole bunch of these Hodor
doorstop so a lot of like tongue-in-cheek jokes and then small
things and big things full Scott full size scale Han Solo in carbonite and
then silver rings in 2013 I started a a fun project it was just something that I
wanted to do people started getting these 3d printers and you know they they
figured I figured that they want to be a part of a fun project and work with
other people because in the past when you have you know blueprints or
something you're working on you're working by yourself and you can work on
in your own shop but now that we have you know the internet plus 3d printing
we're able to connect with other makers and say hey let's all work together on
one project so over the weekends Marty there who's on the Left built the
website we the builders com with the help of the rest of the team
Michael Raphael in the back right in the red shirt 3d scanned a sculpture and
I'll go through those steps here if you haven't heard yet it's called we the
builders calm you can download apart print it out and send it to us so if you
haven't signed up yet you can sign up for the next project and that's the URLs
we the builders calm so right now it's basically Marty and I aside from that
original weekend where we had you know this this team that's the sculptor of
there our third project is wearing the leather jacket on the right name Ryan
Kittleson so I'll show you his sculpture shortly so these are the first four
sculptures I have them here today from left to right we have the Georges
crowdsourcing ttan benjamin franklin stein rosie the riveter
and edgar allan print so these were all done by the community you know people
like you who have a 3d printer or access to one and then submitted the parts to
us after printing and mailed it to us you can see the original sculpture the
first one was it was sculpted in Italy about 185 years ago and then sent to
Baltimore it's of a young George Washington and it is 33 inches tall in
and it lives in the original Washington Monument in Baltimore so for a couple of
months while they were doing renovations we put it in the they put it in the
Walters Art Museum in Baltimore which is you know right down the street and we
were able to 3d scan it there and then use that for the project on the right is
a miniature of the hood on bust of George Washington of Ben Franklin and
that one's in the Metropolitan Museum of our 22 inches tall
we scan that like nine-inch sculpture and scaled it up to be the same size as
George then Ryan sculpted this one digitally Firpo and
this one we we separated it into two colors so for George and Ben it was you
know free for all and you can print any color you want just make sure the
outside surface stays the same for 4po it was our first time saying we want
either light or dark parts so we sorted those files separately so you could
choose to download a light one or a dark one and then print it in that color and
that that tone and then send it to us that way so we had the hair and the
jacket in the darker color and then there's a local artist in Baltimore
named Jen Schechter and she sculpted Rosie and clay about eight inches tall
and then again direct dimensions 3d scanned nylon with a the Faro arm a blue
laser and it picks up all the details and we scaled that up to the same 33
inch tall height as the first three and then chopping them into pieces
we used netfabb and meshmixer to do the slicing and each project was a little
bit different where we're cutting it for you know just cubes or rectangular
shapes and I was you know slicing so I didn't like have a line right between
the lips or or right through the eyeball trying to to move them so it made more
sense and then I deleted all of the solid cube blocks on the inside that way
no one had like a super boring print and there's no real need to have those
internal cubes the gorge project was a hundred and ten parts we did the whole
thing in three weeks including building the website doing the scanning printing
it assembling it and bringing up to the 3d printshow in New York which was I
think that the end of 2013 or 2014 Ben was a hundred and ninety eight parts
and he was sliced in netfabb we did the the George had all of the coordinates
engraved digitally so we have these XYZ coordinate systems so each block we get
we build one layer at a time and we can piece the parts together because even
even though you know that like X 4 y 3 Z 7 is right next to X 4 y4 z 7 it's hard
to tell which ways up and you have to rotate them and orient them properly and
there's like 24 different configurations in each block so it's it's complicated
even though you know the two parts are next to each other it turned out that it
was a whole lot of time to do this labeling for George a hundred and ten
parts and we had two people doing it and we were rotating the parts for best
arrangement for free nobility but once we scaled up to larger numbers of parts
it was too much work so we we just had people like labeling them with a marker
with a sharpie and they it's still really manual like I'm saving each block
from meshmixer or net fab as an STL and typing in its XYZ coordinates as the
filename one at a time manually but the the digitally carving each block was
just too much work so now you just once you print it out you you write it with a
sharpie and these are about half of the parts that users submitted for the Ben
Franklin project we made a little photo collage of them and people customized it
they write little jokes or notes or messages and send it in to us the first
one we received all the parts at my house the second one was at my
makerspace the third one was at a 3d scanning company the direct dimensions
one and then we had the fourth one also the fifth one which I'll get to in a
little bit was from was all sent to Santa Fe so we we did it a much larger
version of this and people are customizing it there's like a resin
print the Bronzeville the sharpie colors are swapping filament and the first four
sculptures we use e6000 to assemble it here's just some of the
pictures of the boxes being sent in and loaded up so we can move on I sorted
them into layers so this is Ben and it's sorted into the ten layers so we solved
the puzzle by putting them all in a ring or and arranging them based on like
where they go from its X x and y coordinates once you sort them by Z then
you have like all the all the first layer parts together and then you can
arrange them in a circle and and glue them together that way so here's at the
last Baltimore node our previous space is where I assembled this one so we did
each layer one at a time and then stacked up the layers and yeah I draw I
travelled him around so I have like George in the seat with a seat belt on
because that's kind of an easy way to bring him to different places and here's
the finished George Ben and Rosie and Poe this one actually is a photo from
the 2018 East Coast RepRap Festival I took it over there so the nation of
makers conference was in Santa Fe two weeks ago and we were contacted to build
a huge version and I thought these 33 inch tall like meter tall sculptures
were we're large you know each block takes hours to print and then there's
hundreds of them so I thought that was a big project but the conference said hey
we want a big one we're gonna have Adam Savage help and we want you to make at
least a six foot tall sculpture and it's in two months and I said that's crazy I
don't know if we can do it let's try and do it so I went and chopped up the same
model that we had I scaled it up I offset the outside surface inward six
inches so I have like a thick wall around the outside and then saving each
one of these parts was still one at a time because it's
you know I have to give it the XYZ coordinates we we didn't have an
automated process for it even though netfabb ultimate has this built-in it
doesn't like seal the mesh it only gives you the outside surface so I couldn't
use that because you can't print you know just the outside surface so but it
saves the files perfectly and it labels with XYZ coordinates and saves each STL
just it doesn't seal it so it wasn't useful so we put a call out adam savage
announced that on his blog lamar freed put it up on Adafruit and we had a lot
of people share it we had over 700 people help over the five or six weeks
that we were printing parts and we had them ship all the parts to the Santa Fe
makerspace make Santa Fe which is where they were hosting the nation of makers
conference at a conference center downtown so this had about four or five
hundred attendees from different maker spaces people who either organized a
maker space run a maker space own a maker space or want their makes her
space to improve so it was a really neat conference and just neat to meet all
these people there and now here's about six or seven hundred of the people who
printed parts and mailed them in so everyone on the website gets there like
Google logo from their gmail account sent over and then there's a little
number next to each picture of each person of how many parts they submitted
so make Santa Fe had a room they stored all these big boxes those are 4 foot by
4 foot by 1 foot boxes and they were all filled up with all these parts it just
it's so many parts each layer was like hundreds of parts so each layer of the
new sculpture was about the size of one of the ones that I brought here I made
these blueprints so each outline you could layout and it was 21 layers so we
had 21 different blueprints of each 3 foot by 5 foot sheet people went through
found the parts laid them out so these next pictures are all just of the
different blueprints and one neat trick that I did for this
project was I made sure that the components each were rectangular prisms
and not cubes they were like taller than they were longer and wider so that way
we knew automatically which way was up or down and then if you looked at the at
the paper it would tell you kind of which way was up or down most of the
time so that saved a lot of assembly a lot of a lot of work because of the size
and cost of glue and weight and number of parts we were applying it we used a
caulk gun and the Loctite there's like a block type power grab all part of a
tease of bought a few cases of these tubes the conference gave us about a 20
foot by 20 foot area and coated the floor with plastic and we went and laid
these all out and built it we started a little bit Friday night build it all day
Saturday and then six hours Sunday so all these parts all these layers we had
about 40 people helping over the weekend and it was just everything was working
we came across some problems but we were able to you know fix them as we went one
of them was interesting because any part that was a curved surface on the bottom
couldn't be assembled that way so it's not something I thought of before so we
had to flip it over upside down so like the bottom of her elbow we couldn't
build that way so we had to flip it upside down to glue it but that made our
blueprints kind of mirrored so we had to transpose them in one of the directions
we then started building we needed to be movable so we have it in a few different
sections so this is the bottom section and it was then mounted to a platform
we're putting on the caulk the glue spreading it around it was really neat
to work with Adam so he helps all all day sunday was gluing parts together
with us and they were documenting it so that should be up in about a week or two
up on untested he has a video that they're editing together so there's the
plinth there was like a 4 foot by 4 foot base or so
for this project all the colors were skin tones so we just did a call-out for
skin tone colors and I don't have too many of this part because I was in their
building and and stacking the layers but it ended up being over 6 foot tall I'm
estimating 450 pounds and it was it was just massive it's the the biggest thing
I've ever made so it's really neat so that's a normal print all the way on the
left like a six six inch tall miniature Rosie the Riveter the
full-color one you can see here which is the 33 inch wall and that's that I had
my booth behind me and then the finished one on the right which wit which was I
think like six foot one inch we then had the fellows from make Santa Fe move it
to the New Mexico Museum of History so it's set up there for the for the next
six months at least maybe a little longer depending on how it goes and then
there's there's me and Jen with the with the final sculpture yeah please help so
if you guys have a printer or access to a printer then you can sign up we the
builders comm if you don't please meet someone this weekend who has because I
feel like everyone has access to a 3d printer we've been doing one build a
year after this conference after this build where it was like so many people
helping we have had several groups reach out to us asking for us to do do this
kind of thing at their event so it's you know something that we're interested in
doing as long as we can get it also work out and you know we'd love your help we
we literally can't do the project without people like you so it would be
really neat to have you tell your friends and help out with future
projects and there's the contact information for me and we the builders
at the bottom there and I have I guess time for questions we have 10 minutes or
so if you guys have any yep thanks
who here helped on the project anybody we have some here that's really neat
yeah we had like over 750 people because there was teams and people building and
then all the parts
I have personal cards for for my business I don't have we the builder's
cards but just sign up go read the builders calm and there's like a sign-up
button we have a Facebook group also it's like at we the builders yeah thanks
the question was is the file available for the smaller version we do have them
but they're not easy to act yeah in one piece for the small version the little
pink one in the corner there we do have the files for all four sculptures so far
they're not like easily accessible on the website but it's something that I
need to put up you can get to it if you go to like the file preview on the
website but it's not like a hot link URL or anything like that
you have to like right click view source and grab them yes we we have heard that
feedback we just haven't uploaded them that way yet yeah if you email me and
ask for it then I'll be able to post it there they're there but you have to hit
the f12 view source and and go through and grab the Amazon link so it's not
like the websites not so we the builders is a totally nonprofit like not
registered nonprofit just like a a project that we do so there's it's just
me and Marty making the website and building the building the parts and
getting people to sculpt in print and with that without like funding so it's
it's a lot of work to do but right now it's up on the website as the preview
URL for the in browser SDL viewer yeah
yeah sure
well I'm estimating it's 10,000 hours of printing for the big Rosie because it's
2600 parts in approximately 4 hours per per part so it's around 10,000 or 11,000
and then around the same four dollars of shipping costs to get them to New Mexico
and then I guess my time was about 80 hours of prep and getting all the files
ready and then the building time so yeah a lot of hours went into it I don't have
a specific count of number of countries but I know we had parts from every
continent except for Austria for Antarctica and then a lot of parts from
Europe and we had Singapore and China and South America there's a few
different countries that submitted par Saudi Arabia Italy yeah a lot of places
for four the question was that the shapes not solid so how did we do it how
do we know how much the material I take out the first one for George there's no
inside George was sculpted from marble at that scale so the back of George has
kind of hollowed out as a as a post so there really is no no depth to George
beyond what you see because it was carved from marble and was thick and
they needed to make it lighter for Ben since we scaled it up we introduced this
extra internal area so I just deleted every block that was a solid block so
there's no there's no solid parts inside Ben it's just the blocks that were on
the surface so they're about three or so inches thick all the way around for
Rosie at the small scale there's some hollow parts but it was just again
wherever there was a solid block I deleted it once I scaled it up for the
big Rosie I you know made a judgment call and I said well I think if if this
sculpture is six inches thick on average so I'll offset the whole part in like so
I have two or three blocks going deep in any direction so it's it's got that six
inch offset and then we built an armature inside I'm not sure if I had a
picture up here of the armature but if you look at her her left arm there which
is in the bottom of the frame you can see a white rectangle and that's where a
2x4 was slid in so it was kind of built around dowel rot two inch dowel rods in
2x4 so we could build a internal armature
yeah Adam Savage is a cool guy you can see like the hole for the dowel rod and
the arm and the front bottom left of this photo so that that hole there is I
think two and a half inches because we had a two inch dowel rod in there with
some space so it's it's really massive this is some of the support to buy for
our beams inside there and the posts going up
but occasionally we had a part that we would reject because either the color
was was very wrong or the print was poor or but for the most part all the parts I
got sent in and got used we send out emails because you're supposed to print
the part and then send it to us and if we don't receive it or don't hear from
you or never got like hey that part shipped we need it then we will send you
some emails and if we don't hear back then we release the part back to the
pool and some other people can print it but a lot of those we end up receiving
the part anyway so we have duplicates so then we kind of just whichever one we we
grab first of the two is the one that gets included but I think it was about I
don't know less than 5% great I will be at the table until the end of
the day and then a little bit yesterday so if you have more questions you can
reach out to me then
you
For more infomation >> Todd Blatt - We The Builders - #ERRF2018 - Duration: 24:31.-------------------------------------------
The Happytime Murders | No Sesame. All Street.
-------------------------------------------
DIYs KAWAII CANDIES 🍪💗 Cupcake Purse, Ice Cream Notebook and Cookie Keychain | DIY Amino - Duration: 7:25.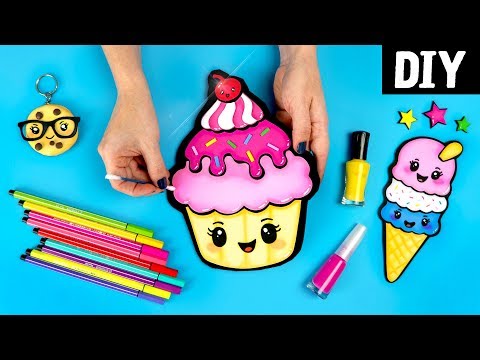
Hi, everyone, I am Dany Martines!
Today I want to show you an app have been using
and have been enjoying: DIY Amino.
The developer has asked me to check it out.
As I enjoyed it a lot, I am going to show it to you.
It is a community of people like us, who enjoy creating.
I am going to show you some cool stuff.
After you create an account, it displays the app's home,
where you will find lots of inspiring ideas and projects.
You will also find a chat to participate in discussions on many topics.
You will find lots of inspiring ideas in the DIY directory.
You may also post your own projects there.
You will be able to meet and follow a lot of people, including me.
Search the 'members' tab for Dany Martines and get closer to me.
Call me up for a quick chat.
I created a poll for you to help me choose the upcoming video's theme.
Choose between flamingo, diamond, or cactus.
Donwload the app.
The link is in the description box below.
It is available for Android and iOS. Best of all, it is for free.
Today's ideas are super, super cute. I loved the projects.
Let's roll!
How about customizing a notebook?
This one was really old. I covered it with double-sided paper.
I printed the background,
and stuck double-sided tape at the back, all around the edges.
Peel it off, and stick it to the cover.
Look at those charming ice-cream cones!
Cut out an ice-cream cone shape using black EVA.
Glue it right at the center.
Use EVA in different colors to cut out the other ice-cream shapes.
Glue them on the black background.
There are also some stars. I glued them on a black EVA shape,
then glued them on the cover, close to the ice-cream cone.
It already looks cute, but there is room for improvement.
Use felt-tip markers in darker shades to outline each shape.
Smudge the ink using cotton swabs. It is very easy to do it.
Trace and smudge diagonal lines on the cone to fake a real ice-cream cone.
Use the same technique to outline cheeks of a little-face-to-be.
Use the template to sketch the face on the shapes.
Drip a drop of black nail polish on any plastic or acrylic piece you find at home.
Use the point of a manicure stick to take some of the nailpolish
to outline and fill the eyes and the lips.
Take your time to do this part so it works well.
Use white nailpolish to add the eye sparkles,
use red for the tongue, then use other colors
to add candy sprinkles all over the white shape.
As soon as it dries,
your super kawaii notebook is good to go!
Use this same technique to create different cover designs for your notebooks.
If you have already enjoyed this first idea, leave your like below
because you will see lots of cute stuff today.
We are going to use beige EVA on the next idea.
Use the template to cut out a circle, then use hot iron to shape it.
Just place it on the bottom of the iron and the shape will come out.
Jerk the iron sideways to remove the EVA circle from it.
Make another shape like this one.
Apply hot glue at the back of one of the circles,
and stick a keychain ring to it.
Then stick one side to the other.
Use felt-tip pen along the edges, then smudge it to add a nice effect.
I used orange at some parts, then beige at others,
adding a shade effect to the whole piece.
Pick a front side, then glue a black EVA eyeglass shape to it.
To make the chocolate chips of this cookie,
I cut out brown cirles and moulded them using a hot iron.
Let's now draw the face.
I made the cheeks,
then made the eyes and the lips using black permanent marker.
Use white nailpolish to make nice eye sparkles.
A nice tip: use base coat to paint the chips and the glasses
and bring out the colors and add extra shine to the keychain.
This super cute keychain is good to go!
I just need to decide if I am going to use it on my keys or on my purse.
Which do you prefer? Tell me down below!
Let's start this DIY with black velboa. Flip it over, fluffy side down.
Use the pattern to cut out this shape on black EVA.
All the templates are available for download. You will find the links in the description box.
Place the EVA shape onto the cloth and cut slits all along the leftover strip.
Then just glue the slits on the EVA until the shape comes out.
I used hot glue because it dries on the spot.
Glue a smaller felt cutout to hide this messy side.
Make another alike shape and glue the cloth on the other side,
making a mirrored shape.
Set it aside and start making the edge of the purse.
Cut a strip measuring about 40cm lengthwise, measuring as wide as you want for your purse.
Cut a hollowcut slit right at the center to place a 15cm zipper.
Wrap this part in velboa.
Flip the zipper and glue it facing down.
It is really quick and it looks groovy.
Flip the cupcake shape with the felt side facing up
and stick the strip around it.
Notice that I placed the zipper at the top center of the shape,
instead of following the outline.
It should look rounded.
I overlapped one part with the other at the bottom.
The purse is taking shape.
A tip: cover the edges with matte satin ribbon to hide imperfections.
I chose this pink shoulder strap and glued it at the side, right at the center.
Bring the ends together and glue the strap until about the zipper line.
Do not forget to measure the strap using your body as a reference.
Place the other part with the felt side facing down.
Use corresponding EVA colors to cut out and glue the cupcake shapes.
Let's practice smudging with felt-tip pens technique.
Outline the shape with the pen and smudge using cotton swabs.
I think this smoke effect makes all the difference
and makes your handcraft pieces even more beautiful.
I smudged some of the creases at some places
such as at the cup and the marshmallow.
Place these white EVA shapes cut out from the template at the top,
then scatter EVA cutouts all over the pink shape to fake candy sprinkles.
Let's add a kawaii touch to it. Draw a face on the cherry,
then smudge cheeks on the cup, and add eyes and lips with black marker.
Do not forget the details.
Use white nail polish for the eye sparkles, and for the outline at some parts.
Tell me if this one does not look adorable!
After it dries, glue it to the purse.
Let me show you how the straps look after glued to the purse.
Apply glue all around the edge then place the cupcake on it.
Use satin ribbon to hide imperfections.
Now this super cute purse is good to go!
Add a coat of varnish to keep your purse extra protected from dust.
Use damp cloth to clean it.
I am in love with the final result! It looks as if bought from a store.
Adorable!
Do not forget to tell me below which was your today's favorite,
do not forget to download the app DIY Amino, the link is down below.
I am going to upload super cute GIFs of today's DIYs.
Follow me there, ok?
See you around! Kiss-kiss, bye-bye!
English Version and Subs: Laeticia Maris
-------------------------------------------
Albano e Romina: fiori e concerti, non senza disavventure. Intanto Loredana... - Duration: 7:31.
-------------------------------------------
Non doveva succedere. "Ma purtroppo è successo". Al Bano e Romina, la notizia choc - Duration: 4:50.
-------------------------------------------
3º Julho das Pretas promove luta e ações das mulheres negras - Duration: 2:32.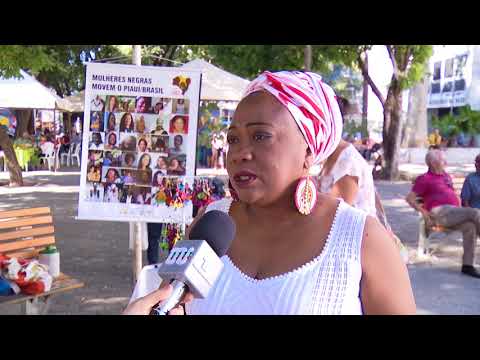
-------------------------------------------
CHORÃO SINGELO (Patativa Chorona) - Ótimo canto para ensinar e esquentar ! - Duration: 40:37.
-------------------------------------------
Come usare il bicarbonato per bruciare il grasso e perdere peso - Italy 365 - Duration: 3:09.
-------------------------------------------
Noticias Telemundo Mediodía, 27 de julio de 2018 - Duration: 21:38.
-------------------------------------------
Citroën C4 Cactus 1.2 e-VTi Shine - Duration: 1:07.
-------------------------------------------
Citroën C4 Cactus 1.2 e-VTi Shine - Duration: 1:07.
-------------------------------------------
A Certain Kind of Love - Duration: 3:07.
Glenda Elliott: Lauree knew how to tease me
without my being offended.
And there was something about the way she would smile that,
you know, I can still see very vividly.
She was the first person I really, truly loved.
But I grew up in the 40s, in a small, rural community.
There were certainly no role models of what it means
to love someone of the same sex.
So, I didn't know how to understand that.
My high school sweetheart, he proposed to me.
And I thought at that time, that's what a woman did,
she got married.
And it didn't take me very long to realize
that I'd made a mistake.
So he and I decided to get a divorce.
During all of this time Lauree and I had stayed in touch.
I knew that I loved her deeply.
She said, "Well I have very strong feelings for you too,
but most of all I want to have children."
She met a man who had asked her to marry him.
Then she got pregnant, and she said,
"If it's a little girl, I'm going to name her after you."
Well, it turned out it was a little boy, and I was relieved.
It really would have been excruciatingly painful
if she had had a little girl named after me.
Somewhere along the way she said,
"If I outlive my husband and you don't have a partner,
perhaps we can grow old together."
And somehow that made it alright.
But then, Lauree got cancer.
And she didn't live very long.
And I did not get to see her again.
It didn't hit me so much until I turned 60 and I began
to really think about old age.
And this was the time that Lauree and I were gonna have.
And it didn't happen.
There are certain kinds of love that never die.
But I don't regret at all our time together.
It is where I learned that I could love and I could be
loved in that complete sense of the word.
-------------------------------------------
Gossip, Paola Di Benedetto e Fede insieme a Santorini: i fan di lui non apprezzano - Duration: 5:21.
-------------------------------------------
Nuova casa per Harry e Meghan: la regina regala loro l'Adelaide Cottage - Duration: 5:10.
-------------------------------------------
Concierge Elements 3pc Down Alternative Comforter Set - Duration: 7:52.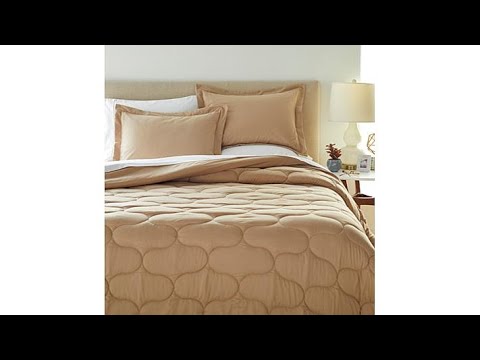
-------------------------------------------
Arsenal star sends clear transfer message to Barcelona and Manchester City ● News Now ● #AFC - Duration: 1:37.
Hector Bellerin insists he 'does not want to be anywhere else' than Arsenal.
The Spanish right-back joined Arsenal as a teenager from Barcelona and has gone on to
play over 150 games for the club.
Bellerin emerged as one of the most promising full-backs in Europe but struggled last season
in what was Arsene Wenger's final campaign in charge.
He will hope to revive his career under new manager Unai Emery and says it is 'crazy'
that there are question marks over his commitment to Arsenal.
Barcelona have expressed interest in signing Bellerin, while Pep Guardiola is believed
to have considered a move to bring the 23-year-old to Manchester City.
But asked directly about his future at the Emirates, Bellerin told the Evening Standard:
'It is crazy that people ask me these questions all the time.
Speaking to the media in Singapore, the former PSG manager said: 'I believe in these players.
'Now I am very happy with the players.
On Monday other players come with us after the World Cup.
'If there is a possibility to sign a player, it isn't very important now, but while the
window is open, we can.'
-------------------------------------------
Seattle aprueba derechos para empleadas domésticas | Noticiero | Telemundo - Duration: 3:29.
-------------------------------------------
SWAG IS A CSGO GENIUS! STEWIE2K CLUTCHING UP! CS:GO Twitch Clips - Duration: 10:06.
Swag
-------------------------------------------
28ª Regional da Pastoral é realizada em Teresina - Duration: 3:01.
-------------------------------------------
DR. LAIR RIBEIRO FALA SOBRE O OVO - Ovo de Codorna x Ovo de Galinha !!! - Duration: 4:55.
-------------------------------------------
You Are Love - Tu Sei Amore - sub.ita - Lee Harris energy - Duration: 15:01.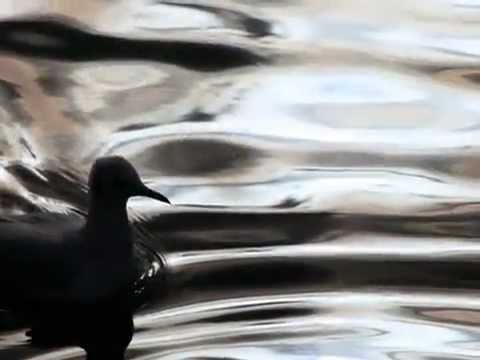
-------------------------------------------
BLOOD FLYING HAS STARTED 27 JULY 18 LIVE PUBLICATION - Duration: 38:09.
-------------------------------------------
I'm back (again(again)) | QNA#2 - Duration: 5:30.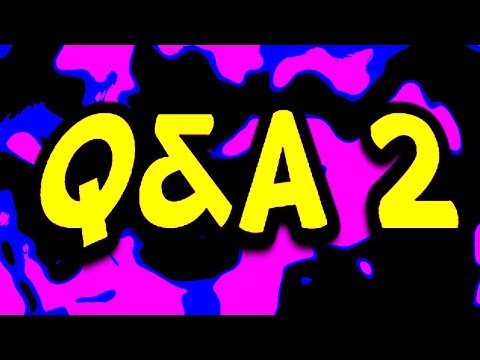
-------------------------------------------
Todd Blatt - We The Builders - #ERRF2018 - Duration: 24:31.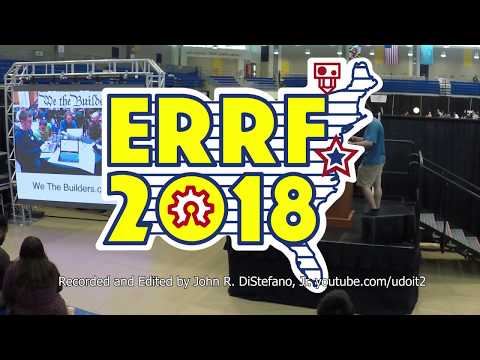
I'm assuming this is working too loud sound good cool okay my name is todd blatt
I have a presentation about crowd-sourced 3d printing that I want to
show you I want to tell you a little bit about myself and what I do I run a
company called custom 3d stuff we are based in Baltimore so it was a easy trip
for me to get here I started it in 2011 I've been making 3d design since 97 I've
been doing 3d printing since 2004 and then I started my company in 2011
officially I make a lot of jewelry so a lot of these 3d printed earrings
and shapes that you couldn't make other ways outside of traditional outside of
3d printing I make a lot of Star Wars props movie prop replicas for collectors
and these aren't like just desktop FTM prints they're usually a high-end made
from at the actual metal or the real parts that they use when they made the
movie props so this is like the the ring that Rose Tico had in the last Jedi and
the you know all the way down to the disassembling the mechanical iris that
they used and casting the band in brass and chemical etching the the faceplate
so it really functions I do short runs of projects for
collectors so this is the ring from the Twin Peaks to TV show they commissioned
me to make rings for the new stuff for the new show so it was the actual
filming and then I made some of these for collectors this is a cast bronze
polished ring from Doctor Strange and I made a whole bunch of these Hodor
doorstop so a lot of like tongue-in-cheek jokes and then small
things and big things full Scott full size scale Han Solo in carbonite and
then silver rings in 2013 I started a a fun project it was just something that I
wanted to do people started getting these 3d printers and you know they they
figured I figured that they want to be a part of a fun project and work with
other people because in the past when you have you know blueprints or
something you're working on you're working by yourself and you can work on
in your own shop but now that we have you know the internet plus 3d printing
we're able to connect with other makers and say hey let's all work together on
one project so over the weekends Marty there who's on the Left built the
website we the builders com with the help of the rest of the team
Michael Raphael in the back right in the red shirt 3d scanned a sculpture and
I'll go through those steps here if you haven't heard yet it's called we the
builders calm you can download apart print it out and send it to us so if you
haven't signed up yet you can sign up for the next project and that's the URLs
we the builders calm so right now it's basically Marty and I aside from that
original weekend where we had you know this this team that's the sculptor of
there our third project is wearing the leather jacket on the right name Ryan
Kittleson so I'll show you his sculpture shortly so these are the first four
sculptures I have them here today from left to right we have the Georges
crowdsourcing ttan benjamin franklin stein rosie the riveter
and edgar allan print so these were all done by the community you know people
like you who have a 3d printer or access to one and then submitted the parts to
us after printing and mailed it to us you can see the original sculpture the
first one was it was sculpted in Italy about 185 years ago and then sent to
Baltimore it's of a young George Washington and it is 33 inches tall in
and it lives in the original Washington Monument in Baltimore so for a couple of
months while they were doing renovations we put it in the they put it in the
Walters Art Museum in Baltimore which is you know right down the street and we
were able to 3d scan it there and then use that for the project on the right is
a miniature of the hood on bust of George Washington of Ben Franklin and
that one's in the Metropolitan Museum of our 22 inches tall
we scan that like nine-inch sculpture and scaled it up to be the same size as
George then Ryan sculpted this one digitally Firpo and
this one we we separated it into two colors so for George and Ben it was you
know free for all and you can print any color you want just make sure the
outside surface stays the same for 4po it was our first time saying we want
either light or dark parts so we sorted those files separately so you could
choose to download a light one or a dark one and then print it in that color and
that that tone and then send it to us that way so we had the hair and the
jacket in the darker color and then there's a local artist in Baltimore
named Jen Schechter and she sculpted Rosie and clay about eight inches tall
and then again direct dimensions 3d scanned nylon with a the Faro arm a blue
laser and it picks up all the details and we scaled that up to the same 33
inch tall height as the first three and then chopping them into pieces
we used netfabb and meshmixer to do the slicing and each project was a little
bit different where we're cutting it for you know just cubes or rectangular
shapes and I was you know slicing so I didn't like have a line right between
the lips or or right through the eyeball trying to to move them so it made more
sense and then I deleted all of the solid cube blocks on the inside that way
no one had like a super boring print and there's no real need to have those
internal cubes the gorge project was a hundred and ten parts we did the whole
thing in three weeks including building the website doing the scanning printing
it assembling it and bringing up to the 3d printshow in New York which was I
think that the end of 2013 or 2014 Ben was a hundred and ninety eight parts
and he was sliced in netfabb we did the the George had all of the coordinates
engraved digitally so we have these XYZ coordinate systems so each block we get
we build one layer at a time and we can piece the parts together because even
even though you know that like X 4 y 3 Z 7 is right next to X 4 y4 z 7 it's hard
to tell which ways up and you have to rotate them and orient them properly and
there's like 24 different configurations in each block so it's it's complicated
even though you know the two parts are next to each other it turned out that it
was a whole lot of time to do this labeling for George a hundred and ten
parts and we had two people doing it and we were rotating the parts for best
arrangement for free nobility but once we scaled up to larger numbers of parts
it was too much work so we we just had people like labeling them with a marker
with a sharpie and they it's still really manual like I'm saving each block
from meshmixer or net fab as an STL and typing in its XYZ coordinates as the
filename one at a time manually but the the digitally carving each block was
just too much work so now you just once you print it out you you write it with a
sharpie and these are about half of the parts that users submitted for the Ben
Franklin project we made a little photo collage of them and people customized it
they write little jokes or notes or messages and send it in to us the first
one we received all the parts at my house the second one was at my
makerspace the third one was at a 3d scanning company the direct dimensions
one and then we had the fourth one also the fifth one which I'll get to in a
little bit was from was all sent to Santa Fe so we we did it a much larger
version of this and people are customizing it there's like a resin
print the Bronzeville the sharpie colors are swapping filament and the first four
sculptures we use e6000 to assemble it here's just some of the
pictures of the boxes being sent in and loaded up so we can move on I sorted
them into layers so this is Ben and it's sorted into the ten layers so we solved
the puzzle by putting them all in a ring or and arranging them based on like
where they go from its X x and y coordinates once you sort them by Z then
you have like all the all the first layer parts together and then you can
arrange them in a circle and and glue them together that way so here's at the
last Baltimore node our previous space is where I assembled this one so we did
each layer one at a time and then stacked up the layers and yeah I draw I
travelled him around so I have like George in the seat with a seat belt on
because that's kind of an easy way to bring him to different places and here's
the finished George Ben and Rosie and Poe this one actually is a photo from
the 2018 East Coast RepRap Festival I took it over there so the nation of
makers conference was in Santa Fe two weeks ago and we were contacted to build
a huge version and I thought these 33 inch tall like meter tall sculptures
were we're large you know each block takes hours to print and then there's
hundreds of them so I thought that was a big project but the conference said hey
we want a big one we're gonna have Adam Savage help and we want you to make at
least a six foot tall sculpture and it's in two months and I said that's crazy I
don't know if we can do it let's try and do it so I went and chopped up the same
model that we had I scaled it up I offset the outside surface inward six
inches so I have like a thick wall around the outside and then saving each
one of these parts was still one at a time because it's
you know I have to give it the XYZ coordinates we we didn't have an
automated process for it even though netfabb ultimate has this built-in it
doesn't like seal the mesh it only gives you the outside surface so I couldn't
use that because you can't print you know just the outside surface so but it
saves the files perfectly and it labels with XYZ coordinates and saves each STL
just it doesn't seal it so it wasn't useful so we put a call out adam savage
announced that on his blog lamar freed put it up on Adafruit and we had a lot
of people share it we had over 700 people help over the five or six weeks
that we were printing parts and we had them ship all the parts to the Santa Fe
makerspace make Santa Fe which is where they were hosting the nation of makers
conference at a conference center downtown so this had about four or five
hundred attendees from different maker spaces people who either organized a
maker space run a maker space own a maker space or want their makes her
space to improve so it was a really neat conference and just neat to meet all
these people there and now here's about six or seven hundred of the people who
printed parts and mailed them in so everyone on the website gets there like
Google logo from their gmail account sent over and then there's a little
number next to each picture of each person of how many parts they submitted
so make Santa Fe had a room they stored all these big boxes those are 4 foot by
4 foot by 1 foot boxes and they were all filled up with all these parts it just
it's so many parts each layer was like hundreds of parts so each layer of the
new sculpture was about the size of one of the ones that I brought here I made
these blueprints so each outline you could layout and it was 21 layers so we
had 21 different blueprints of each 3 foot by 5 foot sheet people went through
found the parts laid them out so these next pictures are all just of the
different blueprints and one neat trick that I did for this
project was I made sure that the components each were rectangular prisms
and not cubes they were like taller than they were longer and wider so that way
we knew automatically which way was up or down and then if you looked at the at
the paper it would tell you kind of which way was up or down most of the
time so that saved a lot of assembly a lot of a lot of work because of the size
and cost of glue and weight and number of parts we were applying it we used a
caulk gun and the Loctite there's like a block type power grab all part of a
tease of bought a few cases of these tubes the conference gave us about a 20
foot by 20 foot area and coated the floor with plastic and we went and laid
these all out and built it we started a little bit Friday night build it all day
Saturday and then six hours Sunday so all these parts all these layers we had
about 40 people helping over the weekend and it was just everything was working
we came across some problems but we were able to you know fix them as we went one
of them was interesting because any part that was a curved surface on the bottom
couldn't be assembled that way so it's not something I thought of before so we
had to flip it over upside down so like the bottom of her elbow we couldn't
build that way so we had to flip it upside down to glue it but that made our
blueprints kind of mirrored so we had to transpose them in one of the directions
we then started building we needed to be movable so we have it in a few different
sections so this is the bottom section and it was then mounted to a platform
we're putting on the caulk the glue spreading it around it was really neat
to work with Adam so he helps all all day sunday was gluing parts together
with us and they were documenting it so that should be up in about a week or two
up on untested he has a video that they're editing together so there's the
plinth there was like a 4 foot by 4 foot base or so
for this project all the colors were skin tones so we just did a call-out for
skin tone colors and I don't have too many of this part because I was in their
building and and stacking the layers but it ended up being over 6 foot tall I'm
estimating 450 pounds and it was it was just massive it's the the biggest thing
I've ever made so it's really neat so that's a normal print all the way on the
left like a six six inch tall miniature Rosie the Riveter the
full-color one you can see here which is the 33 inch wall and that's that I had
my booth behind me and then the finished one on the right which wit which was I
think like six foot one inch we then had the fellows from make Santa Fe move it
to the New Mexico Museum of History so it's set up there for the for the next
six months at least maybe a little longer depending on how it goes and then
there's there's me and Jen with the with the final sculpture yeah please help so
if you guys have a printer or access to a printer then you can sign up we the
builders comm if you don't please meet someone this weekend who has because I
feel like everyone has access to a 3d printer we've been doing one build a
year after this conference after this build where it was like so many people
helping we have had several groups reach out to us asking for us to do do this
kind of thing at their event so it's you know something that we're interested in
doing as long as we can get it also work out and you know we'd love your help we
we literally can't do the project without people like you so it would be
really neat to have you tell your friends and help out with future
projects and there's the contact information for me and we the builders
at the bottom there and I have I guess time for questions we have 10 minutes or
so if you guys have any yep thanks
who here helped on the project anybody we have some here that's really neat
yeah we had like over 750 people because there was teams and people building and
then all the parts
I have personal cards for for my business I don't have we the builder's
cards but just sign up go read the builders calm and there's like a sign-up
button we have a Facebook group also it's like at we the builders yeah thanks
the question was is the file available for the smaller version we do have them
but they're not easy to act yeah in one piece for the small version the little
pink one in the corner there we do have the files for all four sculptures so far
they're not like easily accessible on the website but it's something that I
need to put up you can get to it if you go to like the file preview on the
website but it's not like a hot link URL or anything like that
you have to like right click view source and grab them yes we we have heard that
feedback we just haven't uploaded them that way yet yeah if you email me and
ask for it then I'll be able to post it there they're there but you have to hit
the f12 view source and and go through and grab the Amazon link so it's not
like the websites not so we the builders is a totally nonprofit like not
registered nonprofit just like a a project that we do so there's it's just
me and Marty making the website and building the building the parts and
getting people to sculpt in print and with that without like funding so it's
it's a lot of work to do but right now it's up on the website as the preview
URL for the in browser SDL viewer yeah
yeah sure
well I'm estimating it's 10,000 hours of printing for the big Rosie because it's
2600 parts in approximately 4 hours per per part so it's around 10,000 or 11,000
and then around the same four dollars of shipping costs to get them to New Mexico
and then I guess my time was about 80 hours of prep and getting all the files
ready and then the building time so yeah a lot of hours went into it I don't have
a specific count of number of countries but I know we had parts from every
continent except for Austria for Antarctica and then a lot of parts from
Europe and we had Singapore and China and South America there's a few
different countries that submitted par Saudi Arabia Italy yeah a lot of places
for four the question was that the shapes not solid so how did we do it how
do we know how much the material I take out the first one for George there's no
inside George was sculpted from marble at that scale so the back of George has
kind of hollowed out as a as a post so there really is no no depth to George
beyond what you see because it was carved from marble and was thick and
they needed to make it lighter for Ben since we scaled it up we introduced this
extra internal area so I just deleted every block that was a solid block so
there's no there's no solid parts inside Ben it's just the blocks that were on
the surface so they're about three or so inches thick all the way around for
Rosie at the small scale there's some hollow parts but it was just again
wherever there was a solid block I deleted it once I scaled it up for the
big Rosie I you know made a judgment call and I said well I think if if this
sculpture is six inches thick on average so I'll offset the whole part in like so
I have two or three blocks going deep in any direction so it's it's got that six
inch offset and then we built an armature inside I'm not sure if I had a
picture up here of the armature but if you look at her her left arm there which
is in the bottom of the frame you can see a white rectangle and that's where a
2x4 was slid in so it was kind of built around dowel rot two inch dowel rods in
2x4 so we could build a internal armature
yeah Adam Savage is a cool guy you can see like the hole for the dowel rod and
the arm and the front bottom left of this photo so that that hole there is I
think two and a half inches because we had a two inch dowel rod in there with
some space so it's it's really massive this is some of the support to buy for
our beams inside there and the posts going up
but occasionally we had a part that we would reject because either the color
was was very wrong or the print was poor or but for the most part all the parts I
got sent in and got used we send out emails because you're supposed to print
the part and then send it to us and if we don't receive it or don't hear from
you or never got like hey that part shipped we need it then we will send you
some emails and if we don't hear back then we release the part back to the
pool and some other people can print it but a lot of those we end up receiving
the part anyway so we have duplicates so then we kind of just whichever one we we
grab first of the two is the one that gets included but I think it was about I
don't know less than 5% great I will be at the table until the end of
the day and then a little bit yesterday so if you have more questions you can
reach out to me then
you
-------------------------------------------
How I Make Money Online
-------------------------------------------
[Girls' Frontline] How I Personally Grind 0-2 to Level T-Dolls - Duration: 6:26.
0-2 is easily my favorite stage to level up my T-Dolls, and to farm cores in the process.
My grinding squad will have 3 carriers (2 DPS, 1 Main Tank) and 2 T-Dolls which I want to grind. (I suggest your carriers to be 2 ARs and 1 SMG)
In this case, 2 DPS will be G41, M4A1 and the Tank is going to be Suomi.
I highly suggest your carriers to be at max level and max link, their skills and equipments, the higher the better. (4-5 Stars T-Dolls are also recommended.)
It's optional, but recommended that you give one of the DPS X-Type Exoskeleton, I will explain why later.
Your Tank's equipments of course are going to give her as high Evasion as possible (or Armor in case of Shotguns)
I will now explain the Formation I use.
Enemies in 0-2, they can only hurt the T-Dolls standing in the front column (position [9], [6], [3]). If there's no T-Doll standing at [9], then the one standing at [8] will get hit.
But if there's no T-Doll standing at [3], the one standing at [2] won't get hit.
The current formation is Suomi at [6], G41 at [8] and M4A1 at [5].
Using this, the only T-Dolls who will get shot at are Suomi and G41 (G41 will receive MUCH less damage, but just to be safe, give her (or whoever standing at [8] X-Type Exoskeleton.
In my case, M4A1 will buff G41, G41 and Suomi will buff each other.
The more buffs they give each other the better of course, but you still have to stick with the Formation.
That's why I suggest you use ARs and SMGs.
Now I will pick 2 T-Dolls to level up.
I will use TAR-21 and SV-98 here as examples.
TIP: Pick whoever you like better/want to level faster and assign her as the Squad leader, it will give her a slight boost in EXP.
When you reach level 10, 30, 70, 90, you can dummy link your T-Dolls, giving her more EXP multiplier. And it will help shorten the time to clear stages later on.
They don't need to have anything, no equipments, skill level 1. (But if you can spare some later, it helps.)
Now to their positions.
The safezone in 0-2 are [7], [4], [1], [5], [2]. There's a mortar in this stage, however it will be taken out in 1 second.
With my Formation, I can put SV-98 and TAR-21 at [7], [4], [1], [2]. If you're grinding an AR, put her at [2], she can potentially get buffed from the Tank and vice-versa (depends on which T-Dolls you're using)
Optional: You can bring a second squad of your choice for an extra Action Point in Turn 1. If you don't have one, then it'll simply just change from a 2-Turn-Clear into 3.
Since enemies in 0-2 don't move around, you don't have to worry about the Command Post.
Let's get to the stage itself.
Deploy the Grinders at the Command Post, second squad at the Helipad.
Follow the route.
You can try another route starting from Helipad and see which route is better for you.
588 (for the leader) and 490 EXP per enemy, that's 2940 and 2450 EXP per stage.
There's the mortar, taken out in 1 second.
Retreat your second squad if you want to save some Rations.
You can even try out 1 DPS 1 Tank if you feel confident. For me, this works best for now.
As you can see, only Suomi and G41 got damaged. The others are untouched.
Thanks for watching.
-------------------------------------------
ASMR MOCHI┃MOCHI ROLLS, RED BEAN, TARO, LYCHEE, MILK..┃먹방 FRANCE - Duration: 7:43.
Today I'm going to eat mochi..
I have water
First I start with the small one
It's slimy
It's too good
Taste it
This one looks like a flower 🌸
It's the same
Imagine..
It means you have to close your eyes and imagine in your head
There is on my finger
On that finger
You see ? There is some on my finger
This one I do not like it
It's the same, I won't eat it, I don't like it
Have you ever eaten mochi ?
You said "yes".. Okay !
So, I'm going to eat this one right now
I bit my inner cheek
I don't like
I don't like, I'll put it on the side
This is the one I love the must
It's strawberry and milk 💛
It's this one
There's sugar on it
And in addition it's soft
It's like that inside
It's too good ♥
My belly is full
-------------------------------------------
Nissan QASHQAI Facelift 1.2 115pk DIG-T Tekna Glassroof - Duration: 1:14.
-------------------------------------------
What If Ant-Man Was Real? - Duration: 5:40.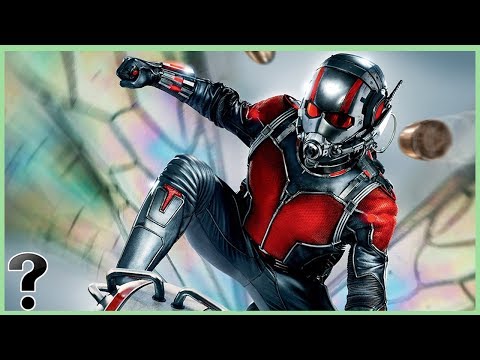
-------------------------------------------
murder mystery : 殺人の謎 → play.skytonia.com [ Live ] ● no. 5 - Duration: 56:43.
-------------------------------------------
Blood Moon Tonight To Bring END OF THE WORLD - Duration: 3:19.
Unless you live under a rock, you know that there's a super rare blood moon tonight,
also known as a lunar eclipse, and doomsday theorists think the blood moon is a sign that
the day of judgement is upon us.
So what else is new.
Welcome back to IO, I'm charlotte dobre.
Its been a while since we've done a doomsday video on this channel, whos excited, I'm
excited.
A blood moon is a celestial event where the moon turns a dark red color when it passes
behind the earth and into its shadow.
While sun is completely blocked, some of the light from it does pass through the earth's
atmosphere, and the result is this beautiful, but also kind of scary red moon.
The one that's happening tonight, July 27th is really special, its the longest blood moon
of the 21st century.
It will go on for about an hour and 45 minutes.
But whenever there's a special celestial event, doomsday theorists tend to come out
of the woodwark to warn that it's a sign that the day of judgement is coming and all
of humanity will be plunged into hell.
I mean…all of humanity?
Like even me?
What if I was really really good this year.
Just saying.
According to Christian ministers John Hagee and mark Blitz, the bible states in Acts 2:20
and Revelation 6:12 that four consecutive lunar eclipses will signal the end of the
world.
The first of these four eclipses took place in april of 2014, the next one was in October
of 2014, followed by a blood moon in april and September of 2014.
One passage in the book of joel states, the sun will turn into darkness, and the moon
into blood, before the great and terrible day of the lord comes.
And another passage in the book of revelations says ' and I beheld when he had opened the
sixth seal, and lo, there was a great earthquake and the sun became black as a sackcloth of
hair, and the moon became as blood.
so basically, while theres this pretty red moon, there will be devastating natural disasters
across planet earth.
But at least there's a pretty red moon.
Throughout history, people thought the blood moon meant that the gods were angry with them.
So, should you listen to these doomsday theorists?
Is the world really ending.
Well Minister Irvin Baxter has been saying the world is going to end since the 1980s.
last time I checked, its 2018, And we're still here.
But according to astronomers, the reason for the blood moon is not because the world is
ending.
It's a phenomenon created by the position of the bodies in our solar system.
Tonights lunar eclipse is literally a once in a lifetime celestial event and It will
be visible across the world.
To top everything off, mars is at the closest its ben to earth in 15 years, so make sure
you get out your telescope to look at them both.
Alright guys, I'm going to respond to some comments now.
Dani boss gamer – is there potatoes on mars.
Actually there are experiments going on right now where scientists are growing potatoes
in mars like conditions for future human settlements.
So there might not be right now, but there will be in the future.
John duran – ya'll think charlotte is single, im trying to slide into her dms.
You can slide all you want but I cant guarantee a reply.
Ygo enthusiast – if I get in an IO video I'll eat a whole door.
Pics or it didn't happen.
Super Toad Brandon – I love space.
I love space too Leave a like on this video if you love space,
and make sure you stay subscribed to IO and turn on those notifications.
This end screen means the video is over, don't worry, theres another great IO video right
over here, or what about this playlist.
Follow me on instagram at charlaychaplin, otherwise I'll see you in the next Io video.
-------------------------------------------
GODZILLA HAMBURGER CHALLENGE in San Antonio, Texas!! - Duration: 7:30.
Fifteen minutes is a long time! Long time for Randy Santel. Yeah
Hey everybody this is Randy Santel 'Atlas' with Atlas &
Zeus Promotions and proud owner of foodchallenges.com! Very very excited
tonight! I'm going for overall with number 563 I'm just outside of San
Antonio, Texas I'm in Helotes, Texas I am at Bobby J's Old-Fashioned Hamburgers
I'm taking on their Godzilla Burger Challenge! Now this thing is massive and
the challenge is that you only have 15 short minutes to finish this thing, but I
am here with my friend, introduce yourself! I'm John, all right he lives
here in the San Antonio area obviously with his giant muscles and Spurs
Jersey, but yeah we've got 15 minutes to finish this thing there is three pounds
of beef and then there are a whole bunch of healthy vegetables there is lettuce,
tomato, pickle, onion, and I think some mayonnaise on the top, but we got to
finish the bun too but luckily no fries or signs but we've got 15 minutes if we
win we're gonna get the about 35, 37 dollar meal for free,
we'll get sweet t-shirts to add to our collections and we'll be one of the few
elite people on the wall of fame, are you ready? Right, alright let's get this
challenge started!
All right we've been sizing this thing up thank you to Bobby J's here in Helotes
Texas for letting us take the challenge finally, eating with this big guy he's done
quite a few of the randy santel fast food $20 value menu challenges, and he's
dominated them! He's done most of the San Antonio ones too so we are both trying
to not only beat the 15 minutes but the record here is 13 minutes and 25 seconds
45 seconds. He may know because he has the record so he's going to try to
beat it and then obviously I am too but let's shut up and eat! 1, 2, 3. . . Boom!
Alright this is broken up into like five patties they said so let's eat some beef!
Dying over here! I keep thinking you are!
Seven and a half minutes in we're halfway through the time limit let's go
you got it!
Last few bites! I got murdered!
Destroyed! That's why he's professional.
With 2:30 remaining! They say time stops as soon as all the foods off your plate
so I swallowed at 12 minutes and 38 seconds but with their time the official
record for the Godzilla Burger Challenge is 12 minutes and 30 seconds, so he is
going to take the rest home as leftovers he will have to pay $35 for the meal but
what'd you think of it? It's delicious just like last time! Delicious burger
Thank you to Bobby J's.
Finally me we have for winning I am going to get be about 35, 37 dollar
burger for free, I will get a sweet t-shirt dad to my collection, and I'll be
I think the fifth person up on the wall of fame! It was overall win number 563 so
thank you to Bobby J's Old Fashioned hamburgers here in a Helotes, Texas which
is just outside of San Antonio, thank you guys all for coming and staying to watch
thank you guys for watching too!
-------------------------------------------
Top 10 Easter Eggs You Missed In Teen Titan GO! To The Movies - Duration: 5:06.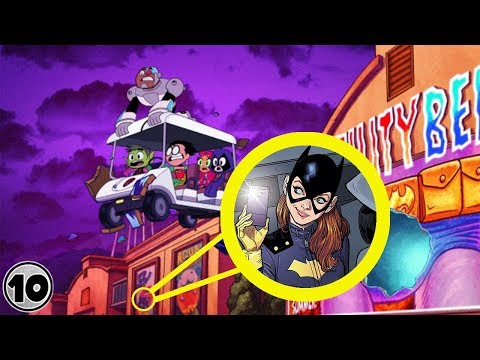
Welcome back nerd squad, my name is Roya Destroyaa and this is Top 10 Nerd.
Despite the fact that teen titans go is nobodyÕs favorite show, the movie is hitting some surprisingly
high notes.
Something that critics are especially enjoying is how self-aware the movieÑand how it is
unafraid to go ahead and make a little fun of itself.
Because they know if they donÕt, we would just do it for them realistically.
So letÕs take a look at the top 10 easter eggs you missed in teen titans go to the movies.
In the number 10 spot, THE JUSTICE LEAGUE ANiMaTED SERIES.
There are many nods in the film to works of DC in existence, and even some to things yet
to come.
Here, when the team walks into warner brothers studio they see a billboard thatÕs got a
familiar four faces on it- the major players of the justice league.
If this looks vaguely familiar, itÕs because this is a recreation of a shot from the opening
credits of Justice League the animated series.
Next, at number 9, THE MOUSTACHE.
The team spots a poster advertising for a movie called Detective Chimp and the Case
of the Missing Moustache.
Seems an innocent enough reference to a DC character, but did you stop to wonder why
the S in moustache is a superman symbol?
This is a subtle but hilarious prod at the cgi used to hide Henry CavillÕs moustache
in justice league, which he had grown out for mission Impossible Fallout.
If you ask me, they should;ve just left itÑa mustached superman wouldÕve been one of the
best things about that mess of a movie.
Coming in at number 8, THE 1989 FONT.
The words Òcoming this summerÓ opened up the teen titans go to the movies trailer.
If you were around back in the day of the 1989 Batman, the font of this trailer may
look familiar.
Indeed it is the same font that was used by what could be considered one of the very first
comic book adaptation movies.
So itÕs nice to see this superhero farce pay some tribute.
In the number 7 spot, THE GREEN LANTERN MOVIE.
At one point, Starfire innocently asks Green lantern if heÕs ever gotten his own movie.
Green lantern answers by saying, Òwe donÕt talk about thatÓ.
This is an obvious jab at the mess that was the 2011 Green lantern movie.
ItÕs nice that DC isnÕt afraid to admit where they messed up, because we all know
their cinematic features havenÕt been the greatest latelyÑcould that change with this
teen titans go movie?
Up at number 6, THE INCREDIBLES 2?
This isnÕt an easter egg so to speak, but if you were feeling a little dŽjˆ vu watching
the movie, youÕre not alone.
And if you missed this entirey, now you know!
But the parallels between ttg and incredibles 2 storyline are quite strongÑboth teams of
heros want want respect and to be recognized as heroes.
Both teams want to go into the public eye.
Both face off against a mind manipulating villains who isnÕt who they appear to be.
Are we sure this isnÕt a rerun?
Coming in at number 5, AQUA MANATEE.
A movie poster that I found particularly funny was the one called Aqua Manatee.
ItÕs very easy to miss this one on account of the titans breaking out in a golf cart,
but it is a poke at the upcoming Aquaman movie and how people arenÕt exactly expecting it
to be a thrilling superhero film, but still probably fun to watch.
Just like manatees, those guys are pretty cute.
Next up, at number 4, NEXT NEXT SUMMER.
This little treat is actually in the same picture as the aqua manatee one; you can see
the words on the wall stating Òholding up bat pants everywhere next next summerÓ.
This is extremely subtle but can be interpreted as a bit of fun making with the fact that
every time we are promised a superhero movie, itÕs promised in next summer.
No, wait, next next summer.
Actually next winter.
Actually forget about it, itÕs not happening.
Up next at number 3, OTHER HERO MOVIE FLOPS.
The filmmaker in the movie Jade Wilson tells Robin that she only makes movies based on
real superheroes.
This cuts to a scene with lesser known heroes Shazam, Steel, and Jonah Hex gigglingÑbecause
the latter 2 had pretty undesirable films.
But does this mean that DC isnÕt expecting much for the Shazam film thatÕs coming out?
Way to set the stage there, guys.
DonÕt care, still gonna go see it.
In the number 2 spot, BATMAN VS JOKER.
The movie posters are indeed something fun for the discerning eye, and this one went
a little bit deeper.
The movie advertised is called Batman vs Joker, Yawn of Justice.
Sounds a lot like Batman vs Superman Dawn of Justice right?
And trust me, the yawn was deliberate; we all know that movie had us half falling asleep,
half wondering what the hell was going on.
At least DC is owning up to it finally.
And finally, in the number 1 spot, STAN LEE.
This was hard to miss, but it was also one of the most brilliant little moments of the
film.
Despite the news reports stating that this was going to happen, a Stan Lee cameo in a
DC film really wasnÕt expected.
Yet there he was, poking obvious amusement at himself for needing to be in all superhero
movies.
And he played himself, despite all his health concerns and troubles going on in his life.
Once the king of cameos, always the king of cameos.
So those were the top 10 easter eggs from ttgttm.
Let me know in the comment section down below what you thought of the film.
My name is Roya Destroyaa, thanks for watching, and donÕt forget to subscribe so you never
miss another nerdy list!
-------------------------------------------
Whiffer Sniffers Series 5 Unboxing And Strawberry Smelling Toys - Duration: 3:40.
hey guys welcome back to another video today I'm going to be doing this whiffer
sniffers and it looks like it's a strawberry and on the back it says
strawberry twirl like a ballerina so let's get into it
hi I'm Kallissa from the channel KG toys and more and I let you know we do vlogs
toy reviews and other fun stuff like this one if you're new to the channel
consider subscribing and also while you're at it maybe like if you like this
video and also while you're at it hit that little bell so you get notified whenever we
post a new video and also check the description down below to know where to
get this and if I didn't say anything or missed it so let's just open this right
up so I have this whiffer sniffer the original it's series 5 and you can get
all five of these so right I have strawberry twirl as it says on the back
strawberry-scented and from the top it smells like real strawberries it smells
so good and then it says it's a backpack so it smells so good you no joke I wish
you could smell this right now so it basically it's like a strawberry
normal stem and then some arms and then it has this cute little to do with a bow
and then someone looks like ballet shoes and there's tons of different ones on
the back wow these are so detailed too there's like a birthday slice there's a
cherry there's a waffle there's a pear there's a root beer float there's the
one I have then there's two history ones which is looks like a
poptart and a ice cream sundae so I really like this it has a really cute
face and it like I say like a backpack or a purse clip this Slick's this is so
made really nice flip it's very cool I like this a lot hmm like right when you
take this out of the package you could smell like right away it smells so good
it smells like real strawberries too and I love this scent this is super cute
nice little backpack clip and there is just a close-up there
so overall so how cute this is and like this is like you'd be a clip I would
probably rate it a 7 because you can't really do anything with it
but it's really cute awesome dude and
this is very amazing little toy for like a little girl or something so I'll
definitely hang this on my backpack or like my bag or something so yeah that's
the final look so if you haven't already make sure you subscribe turn it from red
to grey and also hit the bells you can notified whenever we post a new video
and also if you give this video a thumbs up if you liked it so bye thanks for
watching
-------------------------------------------
top 10 animals vs technology (pets vs technology) - Duration: 2:39.
-------------------------------------------
How Dinosaurs Took Over The World - Duration: 3:23.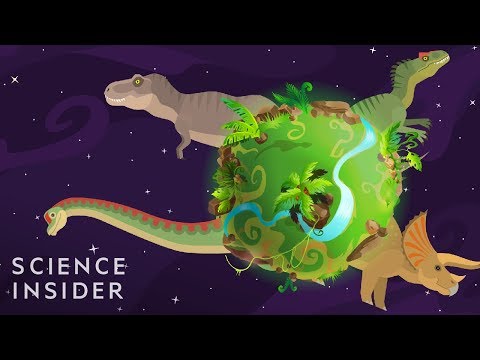
- [Narrator] Right now, paleontologists discover
a new species of dinosaur every week, and it's no wonder.
Dinosaurs dominated the planet for 135 million years,
but they didn't start out on top.
The first dinosaurs emerged around 230 million years ago,
during the Triassic Period.
Back then, Earth looked very different.
Instead of seven continents, there was just one, Pangaea.
Even early dinosaurs
were nothing like those Hollywood giants.
Eoraptor, possibly the first true dinosaur, was puny,
especially compared to top predators of the day,
like some of the giant Rauisuchians.
Over the next 30 million years,
new species of dinosaurs and amphibians developed,
along with the first mammals.
Life was flourishing.
Then, 201 million years ago, everything changed.
Pangaea began to tear apart.
The shifting tectonic plates sparked volcanic eruptions,
which, over tens of thousands of years,
tripled the amount of greenhouse gasses in the atmosphere,
and warmed the planet by three to four degrees Celsius.
It vanquished at least 30% of all life in the process.
But for some reason, maybe luck, or some helpful adaptation,
the dinosaurs sailed on through
to the dawn of the Jurassic Period,
and over the next 135 million years,
they continued to spread, diversify, and evolve
into some familiar faces.
For example, the first Tyrannosaurus
sprouted up some time around 170 million years ago.
But don't get your hopes up.
These guys were no T-Rex.
The real sovereign of the era was the Allosaurus.
It dined on sauropods with its meat cleaver teeth.
Meanwhile, Pangaea continued to pull apart.
By 145 million years ago,
it began to resemble what we see today,
forming isolated pockets
where dinosaurs grew increasingly different.
It was the heyday of dinosaur diversity,
and a new period, the Cretaceous.
In Argentina, giants like Petagotitan,
the biggest dinosaur on record,
turned up around 100 million years ago.
But the most frightening of all appeared in the western US,
around 68 million years ago.
T-Rex, the largest carnivore in history.
On its own, it was a formidable predator.
But it turns out the T-Rex likely hunted in packs,
and where T-Rex did not roam,
other pack hunters filled the niche.
In Asia, the small yet cunning Velociraptor roamed.
It was a bad time to be a mammal.
And then, 66 million years ago,
the Chicxulub asteroid wiped out all the dinosaurs.
Well, almost all of them.
One group remained.
Their descendants might be sitting outside your window
right now.
Birds.
That's right, modern birds are dinosaurs.
Turns out the legacy of these titans today is, well, dinner.
This video is made in large part
thanks to Steve Brusatte,
and the information in his new book,
The Rise and Fall of the Dinosaurs.
What interesting dinosaur facts do you want to know about?
Let us know in the comments.
-------------------------------------------
Here's What Beans From "Even Stevens" Is Up To Today - Duration: 3:03.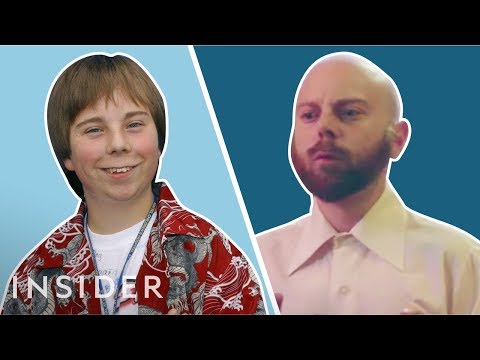
- Bacon?
Bacon?
- Hi guys, my name is Steven Anthony Lawrence
I was Beans on "Even Stevens."
Everybody has a Beans in their life
or they are the Beans.
If you can't think of one you are.
- That's one of the top three fake cries I've ever heard
and two of them belong to me.
- Thanks.
I've got skills.
- You know you work five days a week with people
for four years and it's a set like that,
you become very, very, very, very close to people.
You know, it was like a family.
There was not a dry eye
in the studio on the last finale.
Shia has a wacky side.
Maybe I like him because I kind of have
a wacky side too, I guess.
But, you know, he has a huge heart,
he'd literally give you the shirt off of his back.
I still lived in Fresno, actually,
when I was shooting the show.
My dad was driving me back and forth,
you know, putting a lot of miles on cars.
Shia one day just kind of surprised me with an Xbox
on Christmas.
- Well from now on,
your name is Beans.
- Why Beans?
- Kid, a nickname is not supposed to be logical,
see, it's supposed to be fun.
- The audition process was pretty cool, actually.
You know, you have pre-reads
and then you have your call backs.
My thing, my personal thing that I always did
as an actor, as a kid at least,
was I kind of feel out the room,
see if they were kind of in a rush or not,
if they were kind of connecting.
Then I'd ask if they wanted to hear a joke.
So, I told this pirate joke.
There was a pirate on a ship,
- And the ship was a rockin' and a rollin'
and I fell off me ship.
And a killer whale came and bit off me leg.
And I said to him "How'd you get the hook?"
It was the first kind of stunt thing I had to do,
they lowered me down like "Mission: Impossible"
while the girls were sleeping.
It was the most jerry-rigged stunt ever.
It was like one of those pulley systems.
All this grip needed to do
was for me to just piss him off one day or something,
and go (grunts).
I am still doing classes.
I do only charge 40 bucks a week.
I teach kids, I teach all ages.
Anybody that's hungry.
I think it's a big, big, big blessing
to get kids to start learning technique at an early age
instead of just making faces in front of the camera.
We underestimate kids.
Kids can be pretty darn smart at times.
Maybe.
Maybe, I can't actually say anything right now about that.
-------------------------------------------
Capuchin Monkey Learns How to Open Doors LL (#234z0 - Duration: 3:43.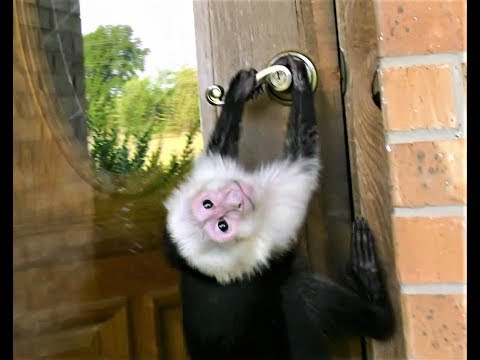
hi everyone we got our chairs all set up under this big tree
Lillian Louise is my two-year-old white-faced capuchin monkey she wants to play
outside today it is evening time and just cool enough for her to play so
here we go and there she goes.
There she is.
This is a black walnut tree
and Lillian loves to climb it
what are you doing she wants to go play at the house.
Lillian decided to come
over here where the water is she must be thirsty
are you gonna make a mess with that paper towel hmm she loves to play
outside and we try to let her play outside every day but sometimes it's hot
so we don't let her we let her play in the house yeah
yeah yeah
Lilian loves fruits and she loves vegetables and peanuts and she eats
really good yeah hi but she jumps and plays and runs and runs it all off
She's trying to open the door. are you trying to open the door so we can go in
Are you opening the door? Are you ready to go inside? Yeah. Are you ready to go in?
-------------------------------------------
Soy Luna 3 | Ámbar doesn't want Sharon to go ahead with her plan (ep.44) (Eng. subs) - Duration: 2:09.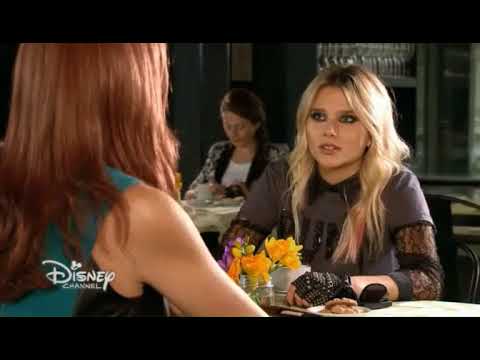
Now I understand who everyone is talking about when they said red haired woman.
What do you think?
Do you like how it fits?
That you're going too far.
That's what I think.
They will discover you if you go into the house like that.
The last thing I need is to listen to your warnings.
I know very well how to act.
Everyone figured out who Victoria Sureda was.
That's already solved, I switched identities now.
I'm Vanessa Fürst.
I have everything under control.
It's not long before I get my entire revenge.
Control, revenge.
I really can't believe you keep thinking like that.
What does it serve you?
I don't recognize you, what happened to you?
My revenge isn't as important as them anymore.
You know that's not true.
Don't you want to change?
Not change your hair, your clothes, you lipstick colour, but change for real.
You're not the one to tell me what I have to do.
How can you live with so much bitterness?
I really think it's time to change everything that you're doing.
What if I don't? You'll betray me?
I won't do that.
Your decision is entirely yours.
I think you can think about finding a better solution.
I don't know if the Valentes deserve this.
What are you saying?
The Valentes deserve that and much more.
-------------------------------------------
AOD Master Conversion Package | Monster Transmission - Duration: 11:20.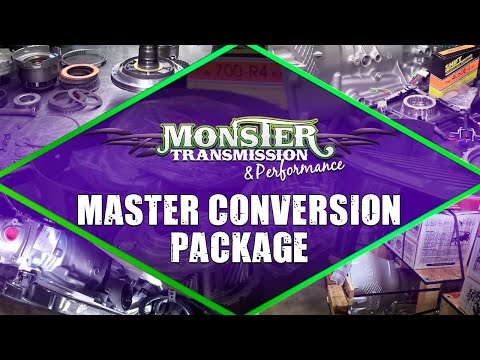
welcome them off the transmission sure Curt's corner today we're to go over an
eight oh D conversion package and you're like wow sounds pretty intense well it
is there's a lot of parts in a conversion package you know you get the
block plate inspection cover torque converter training mouth TV cable
brackets instructions yeah it's okay we got it under control okay we give you
all the bolts and screws that you need for this setup to make the conversion
from an older transmission let's say it's c4 or c6 transmission over to the
overdrive so it's a very very simple conversion we make it simple but giving
you everything you need to do this conversion now this is a condition you
should see it receive in in a nice big monster logo on the side of the box
before you sign the freight bill from the carrier you want to thoroughly
inspect the outside of this box to insure that it's in good condition you
don't want to get one in like this you know okay
there's a pretty good indication that there's a problem here okay if the boxes
have holes in it it's a it's obviously been opened before there may be parts
missing so in those situations you want to open the box unscrew the side of the
box slide it off to inspect the product before you sign the freight bill once
you've signed the freight bill from the carrier
you've now accepted the product and the condition they delivered it in so it's
very key step one when you receive a monster transmission check the condition
of the packaging before you sign it in another hand if you get a
transmission and it has no box there's obviously a problem that all of our
transmission shipped out come in a packaging like so so we're now going to
open this transmission up and the one worker opening today is specifically an
AO D conversion package so some additional components that come with
this package that don't normally come with just ordering a transmission so
we're going to open this up and we'll go over each item that comes in the monster
conversion package then we've done so there's not banding equipment to deal
with it's basically three to four screws that you unscrew from the power
getting at least one to two sometimes four screws on each side depending on
the unit so it's as simple as that slide the box off and guess what now you have
a nice table to check all your products out now on the first thing you're going
to notice is on the very top of your shipment will be your end voice the
warranty documentation paperwork as well as very detailed instructions the things
you need to check before you install the transmission and then accident thien's
installation procedure all the way up to how to adjust the TV cable on this
particular unit so all your instructions are in this package in this envelope as
well as your monster stickers and other information so that's step one step two
you'll notice you have a trans caller on top the trans cooler will come with its
own instructions cables brackets everything for the trans cooler kit is
inside this packaging so this is the cooler that comes in the conversion
package the next item because this is a OD they'll come with a multiple set of
brackets one set of brackets is actually for the carburetor or throttle body so
this will hold the cable on your intake for the TV cable the throttle valve
cable so this is the cable we do have separate video instructions on how to
set up the actual TV cable but it has its own printed instructions made by
Lokar and it shows you how to set up this TV cable and the critical operation
it does which sets the line pressure of the transmission so I highly suggest you
watch our monster AODA OD TV cable instructions I have a whole video just
dedicated to installing this cable next up you'll notice there is the fluid
which the customer ordered extra with this unit and then the torque converter
which was custom calibrated to his specific engine the size cubic in size
as well as the cam the lift and duration of cam and the tire size all those play
in the factors of determining the stall rate as a converter so this is a
converter that matches this particular application you also nose mouth alone
front is the actual transmission mount to go on the transmission itself also
attacks will be a whole bag of bolts and screws now we'll go over each set of
those because it's very important there's a whole bunch of bolts and
screws here okay first thing we're to start with is the actual speedometer
gear there's a nylon gear and you'll take this take their factory gear off
the speedo cable and you'll install the gear because this will be calibrated to
your vehicle tire size and rear-end gear ratio and the transmission so this is
the gear will come in the kit you'll also include four torque converter nuts
that match up for the four studs on the converter it'll include two transmission
mount bolts place this mount onto the bottom case of the transmission you'll
include two nuts which fit the two studs to go through the crossmember on your
application so these are nuts for the transmission mount it will also include
a smaller nut this nut actually goes on for your throttle cables the TV cable so
there's a rod that goes through the linkage and this nut fits that arm on
the transmission for the TV cable it'll come with two longer these are 3/8 16
thread bolts these are your starter bolts you'll include another bolt 3/8 16
a little shorter this actually is a bolt hole on the driver side of the casting
of the case to hold the TV cable or bracket to the transmission case then
you have the actual bolt for the speedometer housing these bolts go in
the front portion of the case that holds an inspection cover to make sure no
debris gets into the converter area of the transmission there's three bolts
there so it's a whole variety of bolts that come with the transmission so when
you do your conversion you pretty much everything except for the actual bell
housing bolts which you're reuse off the old transmission so that covers all
bolts and screws we also have on the transmission or in the bag or the two
coolant line fittings a lot of times because we just recently tested the unit
these coolant line fittings will be on the case of the transmission so the
coolant line fittings are here it also will come with the the multi-leveled
linkage arm so on the universal fits and that linkage arm it's adjustable so you
don't have to take the link it's out of the transmission and reinstall it in
different clock positions it comes with a universal linkage arm manual shift
lever arm on the transmission as well as a locking Dix dipstick tube so this here
has a locking mechanism so when this transmission builds up extra pressure it
will not pop the dipstick up and vent it onto your nice engine compartment we're
now going to remove the banding so we can show you the other brackets and
components that come in this kit it is the converter that came with this
particular unit you notice that the converter will have a hub cover okay to
prevent any debris from getting inside the converter as well as there are for
nylon caps which is protecting the threads of the converter so they're not
damaged in packaging or shipping so you can remove these covers before you
install a converter and talking about converters need to ensure that you watch
our video on how to install a torque converter because it's critical on
setting up these especially new transmissions that you pre-fill the
converter or at least one or two quarts of transmission fluid and that you
grease this hub prior to installing it on the transmission that's critical
there's also a whole list of tags all around the transmission reminding you
what to do during installation you make sure you tighten the coolant line
fittings that you install the speedo gears that you check the threads of the
starter bolts and you put the bolts in the case before you install the unit and
you ensured how you install the converter so there's a lot of tags
around the transmission that reviews the important areas to look for as you're
installing the transmission we now have the fluid it's 12 quarts but it exposes
two covers this is an actual engine block plate that will
come into conversion now this will go between the engine block and the front
of the transmission so you want to make sure that you if you don't have an
engine block plate then we provide you one in a conversion package you need to
ensure that you use this one even if you have a factory one it's a nice new plate
to install for the conversion package then there's this inspection cover I was
talking about this goes actually in the bottom part of this plate so you seal up
the whole front of the transmission so no debris rocks dirt mud can get up
inside the front of the transmission just like the factory unit so these are
out the last two components if you still have the transmission mount here what
we're going to do is we're going to remove the mount from the table now
you'll notice the actual transmission is strapped down to the table so I'm going
to cut that banding that kept it in place during transit and you notice that
that this actually went around a piece of wood and it's not actually clamping
down on the transmission case itself you remove these screws there's four legs
remove the top of this and then exposed to the transmission now the transmission
by removing the table you can simply lift it you can actually use this
converter bracket the bracket on the front of transmission this actually was
to secure the Box down as well as protect the front of the transmission
and the back legs actually core support and that's what the the packaging the
box was screwed to but you should be able to lift so make sure you have it
steamed lift your one person on the front can lift by this wood bracket
that's bolted to the case and then grab the tail housing and lift this up put
them on the transmission jack and then you install the torque over order after
you filled it with some fluid and you can go on by installing all your
apparatus onto the transmission case prior to installation there's a lot of
components in the AOD conversion package similar to the 700 other conversion
package that we offer but this is the most thorough one on the market there's
no extra there's no hidden parts everything comes in a conversion package
now if you have any questions on the conversion package are
team be more than happy to answer any questions that you have to give us a
call toll free
-------------------------------------------
Nikolai Could Save Blood of the Dead - Duration: 16:02.
*pre-roll ad*
No seriously.
Why the heck would Jason chose Nikolia as his favorite?
He doesn't appear to be the main character of the story, he hasn't done anything truly
heroic, and by the end of Revelations he still does trust Richtofen according
to his countless quotes.
So what gives?
Well let's explore Nikolia and Jason to figure out what could be in store for him
in Black Ops 4 and why it could mean everything.
What could Nikolia's big role be in blood of the dead.
At this point, Jason Blundell, the creator of the game has told us that his favorite
character in the game is nikolia.
He is the odd character out in Primis.
Not much has been done with him at this point in comparison to the other characters.
For instance, Richtofen has had a huge change going from evil scheming scientist, to god,
to a neutral individual looking to save himself, to caring about his friends and showing remorse
for his mistakes.
Dempsey has gone from a killing machine moron, to a soldier dedicated beyond his call of
duty, to an introspective individual who finds the hardest thing for him to do is to kill
another version of himself.
His remarks about what happens to himself since his innocent soul is in the house sheds
light on how Dempsey is starting to ask big questions about the world around himself.
The character that had no problem taking life is now struggling with the reality that his
own life will end.
Takeo has had the greatest change from annoying honor bound stereotype to a strong courageous
leader, to becoming an individual stepping outside the brainwashing of his very identity.
Takeo had the very core of his character shattered in Zetsubou No Shima.
Now experiencing a new-found independence for his own individuality.
No longer was Takeo doing the impossible for the emperor, but for himself.
Finally, Takeo was taking control of his own destiny in service to ideas of his own.
But what of Nikolia?
He went from bumbling drunk to extremely serious to depressed and finally mournful of all that
he has loss with a quiet undertone of absolute rage.
In his quotes from Der Eisendrache through revelations he never trusts richtofen.
He does not change in his stances and is still filled with the sadness of loss by the end
of Revelations.
He loss his family, his country, and himself.
Nikolia has become the forgotten and boring character of the crew when he was once the
funniest and arguably most entertaining character in the Ultimis group.
How could that Nikolia be Jason Blundell's favorite?
Well there is more to tell with Nikolia.
A quote that was said by Wesel way back in 2013 was the following:
"Nikolia nikolai, nikolia why do I keep hearing that name?"
A quote that has been dissected to death will probably become one of the greatest and most
obvious foreshadows of all time.
Jason even commented that Mob of the dead is his favorite map of all time, which probably
leads into the implications of the map.
It was the first map Jason headed.
It was where he decided to create a beginning, middle, and end with the help of his team
at Treyarch.
Mob of the Dead was a huge departure from what we knew in zombies.
Mob of the Dead is symbolic of the zombie ideal the team holds so dear, "Do not do
the same thing as before.
Do the unexpected.
Be better".
Mob of the Dead was the foundation for their success forward.
Now who is at the center of this storyline inside Mob of the Dead?
It is weasel or Arlington.
Al is the only character who seems to know that they are in a cycle.
He becomes the key to breaking the cycle.
So you would think Richtofen would have a huge influence on the map or Al because he
seems to be the protagonist of the series.
But we'd be wrong to say that because it isn't Richtofen's name that comes to Al's
mind in Mob of the Dead.
It is Nikolia's.
Could Nikolia be the key to end the cycle in the Aether storyline?
But why him?
What is so special about Nikolia?
Well to start, in Blood of the dead Nikolia is the only team member to still have his
soul.
He has not sacrificed himself yet because he has yet to visit Gorod Krovi.
This is a key attribute that could separate him in importance during the blood of the
dead map from the other characters.
During the lead up to the release of Gorod Krovi the ocmmunity expected some kind of
trouble in Nikolia's map.
Our characters were going map to map collecting souls facing almost no real changes in their
plan.
Ironically enough, we were sadly disappointed with the team's success.
One detail that sticks out from all the deaths is the bullet hole in Nikolai's armor.
The bullet hole is there when we first meet him in origins.
The very same bullet hole he receives from 2.0 Nikolia in Gorod Krovi.
This is one of the only physical signs of the cycle on our characters that I can think
of.
We have been using the blood vials to help us figure out where they are, but the bullet
hole leads directly into the paradox of the cycle.
He got the bullet from 2.0 Nikolia, but when he is sent back in the great war and eventually
to Origins we find him with
the same bullet hole.
It
could be a detail
that I have
put too much interest into, but this could be a sign that the crew we play as in Black
Ops 3 has been through those events many times.
That detail could be highlighted in blood of the dead when the cycle is broken.
Speculation about the ending of Mob of the dead has caused many to believe that drinking
the blood vials only works when the blood is from souls that are stuck in purgatory.
That's why Vicitis was put on ICE and why the mobsters are stuck in the cycle on the
timeline.
Their limbo status allows our characters to survive the destruction of fractures at the
end of Revelations for reason Treyarch has withheld from us.
Furthermore, nowhere on the timeline does it reference the ending of Mob of the dead
when the cycle is broken.
The only person to break the cycle is the weasel when he defeats the mobsters.
The very same person who calls out nikolia's name.
The character who remembers that they have been stuck in a cycle.
The character that could have been told by nikolia what to do.
Or possibly the only character who could sacrifice themselves to give weasel the ability to remember
how to break the cycle in order for everyone to be free.
Look at the ending of Mob of the Dead.
Look how the zombies are working to help Al.
Do the zombies want the cycle to end?
Are they suffering too?
What if the zombies are looking for an end too?
There
is going to be a huge responsibility or burden put onto nikolia in blood of the dead if things
continue the way we predict.
But there are other options.
Notice that the comic book loading screens have been changed.
We may be able to directly attribute their change to the breaking of the cycle.
This means blood of the dead wouldn't be the end of the aether storyline, but more
like the final stretch.
We can see the changes to the original kino loading screen undoing all of those maps.
The earth is saved from the events of Moon and Tranzit.
We are slowly seeing the world becoming zombie free on the changed loading screens.
An extremely important detail is the change of the die rise loading screen.
It now teleports our team, from what seems to be the ascension facility, to the house
in Britain!
But look at the crew, it is not Primis Richofen but instead Ultimis Richtofen with the rest
of the primis crew.
Is Richtofen sacrificed in blood of the dead?
What role will Nikolia play in this new path forward?
Does Nikolia become the new team leader making sure Ultimis richtofen doesn't derail their
heroic journey?
Nikolia's story is one of depression, grief, and abuse.
His abuse of Alchole created wild stories of made up lives away from the reality of
his loss.
In the Giant trailer we hear how he longs to go back to his family.
Where is Nikolia's resolution?
Where is his peace?
These questions are what we have in store for nikolia in the next few zombie maps or
at least blood of the dead.
I'd like to know your thoughts about Nikolia and where you think his character is headed
in the next map.
Do you think it is possible that Nikolia will be the key to saving the Aether universe?
Or will we be left with another disappointing performance by a once beloved character?
Thank you for watching!
Make sure to subscribe if you have any interest in hearing more from me.
I plan to be covering everything I can in Black Ops 4 zombies including guides, tutorials,
theories, and explanations.
Leave a rating if you have the time and have an absolutely wonderful day.
I will see you in the next video!
Bye!
*credits*
-------------------------------------------
Why Highly Intelligent People Struggle to Find Love - Duration: 3:27.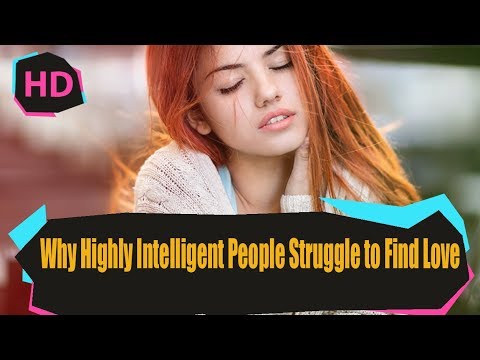
Why Highly Intelligent People Struggle to Find Love
http://iheartintelligence.com
Well, this is not just a story.
Highly intelligent people somehow find it really hard to be in relationship, they undergo
a lot of trouble and end up being alone again.
Sometimes they prefer to be alone, and some other time they just didn't have the will
to fall in love.
In a conversation the other day, a friend of mine implied that he was single because
he was too smart.
I didn't have the heart to tell him that it probably had more to do with the fact that
he looks like the secret love child of Rick Moranis and a woodland creature.
Now, I wondered to myself, "does being smart make it harder to find love?"
In the end, I think it really does.
I'm not saying that if you're in love that you are stupid.
I'm not saying that at all, so let's be clear.
I'm saying that highly intelligent people have a harder time falling in love, and here
is why:
1.
Intelligent People are More Analytical when it Comes to Love.
Intelligent people tend to have better foresight.
Foresight, in and of itself, is basically just the ability to analyze a situation, recall
relevant past experiences, and make an educated assessment of the future possibilities of
the situation.
Apply that mentality to a relationship and you get situations where smarter people are
quicker to duck out of a relationship at the first sign of trouble.
If experience is the best teacher, then the smartest people will rely on experience to
guide them.
Relying on experience to navigate a relationship can be tricky, though.
Every relationship has similar situations.
What ruined one relationship doesn't always have to ruin another, but for people who rely
heavily on their experiences, they can often walk away at the first signs of trouble.
2.
Intelligent People are Guarded
Another side-effect of relying on experience when it comes to love is that intelligent
people tend to be way more guarded.
They have a harder time opening up because that analytical brain never stops reflecting
back on past situations where they opened up to someone, and ultimately got hurt in
the process.
For this reason, other people assume the person is cold or distant, two characteristics no
one wants in a partner.
3.
Intelligent People are often Single by Choice
Highly intelligent people think analytically, even when it comes to things like relationships.
Therefore, intelligent people realize that being alone is better than being with the
wrong person.
It's a rational, thought-out decision.
So, in essence, most really smart people are single because they want to be.
It is a rational, thought out decision, not a circumstance of their situation.
So, what do you think guys?
that's the reason why highly intelligent people struggle to find love.
Really cool information isn't it?
Leave us a comment down below and let us know what your thought of this video.
Don't forget to give us account subs and watch other amazing videos on our channel.
Also, don't forget to check link on the description below to see our interesting offer that might
be useful for you.
Thanks for watching!
http://iheartintelligence.com
-------------------------------------------
When A Frantic Father's Baby Went Missing, First Responders Found A Nightmare In The Daycare - Duration: 5:12.
Cornelius Jones could hear his one-year-old daughter screaming but he
wasn't able to get to her it was dark and she was frantic so he dialed 911 and
the emergency services eventually got inside the building but how on earth did
all this happen
Cornelius Jones is a father from Chicago who one night back in 2015 got the
fright of his life at the time his one-year-old daughter journey was
enrolled in a daycare center called all things are possible for kids on the
evening in question Jones headed down to the facility to
pick up his daughter but what he arrived everything was not as it seemed there
was something strange about the daycare center and it immediately made Jones
very worried indeed Jones had arrived 15 minutes before the childcare facility
was due to shut for the day however when he got there the police
already looked totally closed up in fact all the lights were off inside and the
front door was locked and there was no sign of journey first Jones rang the
doorbell in the hope that someone would answer and bring him his daughter but no
one did then he called the daycare number but once again the worried dad
was left hanging by this stage Jones was getting very concerned about his
daughter he tried the center's number again but still no one picked up the
phone that's when the frantic father decided to take matters into his own
hands without a second thought he began kicking the front door however he still
wasn't able to get inside the locked center then Jones heard his daughter's
voice she was screaming and the sound was coming from inside the darkened
building that's when Jones knew that it was time to call 911 so he put the call
in then got in touch with Journeys mom Kitty shibaura forum' Jones's girlfriend
who was also a working professional immediately rushed over to the daycare
center and getting the horrifying call about
journey being stuck inside I was just trying to get over here as fast as I can
because that's the worst thing that could ever happen but I didn't want to
happen she told Fox 32 Chicago soon the fire
department arrived that all things are possible for kids the fireman then got
their tools and worked tirelessly to save the one-year-old trapped inside the
building some dramatic cell phone footage captured the crew trying their
best to prise open the door to get to journey happily the crew eventually
managed to break into the daycare center but once they got inside the ordeal for
Journeys parents wasn't quite over Jones were called not being able to find his
daughter in the moments after gaining entry to the building journey's dad told
Fox 32 Chicago that he was thinking where is she
where is she he remembered being able to hear his daughter screams but still
wasn't able to spot her in the darkness a video taken that night shows the
rescue crew searching the corridors for the stranded time but then thankfully
they finally found her one of the police officers flashed a light to the left and
flashed it back to the right and that's when I saw her crawling towards us
screaming Jones said and my heart just dropped a member of the rescue team then
scooped journey up into her arms finally putting an end to what must have been a
very scary experience for the baby as well as a worrying time for the infant's
parents needless to say Jones was relieved that his daughter was not in
any more danger but the concerned dad still had some questions about how the
upsetting incident had been allowed to happen I was glad that journey was okay
but I was like real mad I was mad because how could you leave a baby in a
daycare how could a child go unaccounted for Jones said to the local news station
boram chu was furious with the center staff for leaving her daughter behind at
the end of the day I come here and I sign her in and out
and so why wasn't the list checked before everybody left she wondered all
things are possible for kids meanwhile offered no comment to the media
although Jones reportedly spoke to the staff after the incident he said that
they claimed staff were still on premises when they came to pick up
journey Boram also spoke to the director of the daycare facility who reportedly
told the mom that staff had mistaken journey for a down but Boram was not
convinced by the explanation she's not that little to be a doubt she pointed
out it was only journeys sixth day and all things are possible for kids and her
parents said they wouldn't be sending her back what's more they pushed for the
daycare center to be closed down on account of its apparent oversight with
their daughter if anything it should be shut down I mean nobody leaves kids
behind toddlers I don't care how old you are that's dangerous
Jones argued Fox 32 Chicago reported that the Department of Children and
Family Services had launched an investigation following the incident
there's no doubt that what Jones and Boram went through his parents that
fateful night must have been horrifying but thankfully journey made it out of
the locked building unscathed the rest of the investigation remains unknown I
hope you liked this video if so please hit the subscribe button and click on
the Bell icon to make sure you never miss a video from our Channel
-------------------------------------------
Celebs Who Can't Stand The Olsen Twins - Duration: 5:36.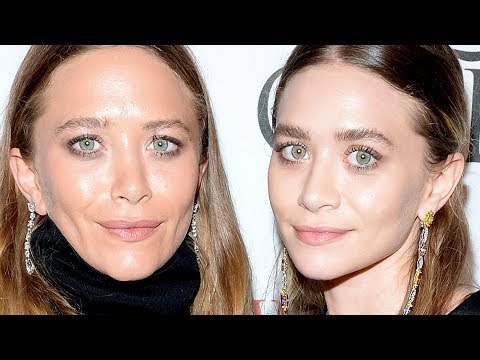
Claiming to hate fame and all of its trappings, Ashley and Mary-Kate Olsen like to live in
the shadows.
But the public's fascination with the twins has only escalated since the '80s, with tabloids
gleefully reporting their every breath.
Speculation continues to swirl as to whether they'll ever make a cameo on Netflix's Fuller
House.
Plenty of fans and former cast-mates want the sisters to return to the franchise that
made them famous, while some of their peers would prefer not to see them on TV - or anywhere
else.
From strained relationships with former Full House-ers, to soapy scandals involving socialites,
here are the celebs who can't stand the Olsen twins.
George R.R. Martin
You'd think Game of Thrones' master scribe, George R.R. Martin, would be too busy thinking
about White Walkers, to have an opinion about the twins.
But you'd be wrong.
This rather unbelievable beef stemmed from Martin's time scripting on CBS's Beauty and
the Beast, in the '80s.
The show was top in its time slot for its first season… but then a certain sitcom
came out of nowhere, trouncing Beauty and the Beast in the ratings.
Martin said, during the 2012 Toronto Film Festival,
"This g------ thing became a hit.
And suddenly, we were not winning our time slot anymore."
And he's hung on tight to those hard feelings, like Daenerys to her dragons, saying,
"That's why I've always hated the Olsen Twins and still do to this day."
Lindsay Lohan
In 2008, a certain Mean Girls star allegedly slugged down a soul-bending amount of Grey
Goose and terrorized revelers at celebrity hangout, The Beatrice Inn - setting her bleary
sights on a certain Ashley Olsen, according to the New York Post.
As the story goes, Ashley was just saying hello to DJ Samantha Ronson, who was dating
Lohan at the time.
And that caused LiLo to allegedly yell,
"Get your 15-year-old Full House ass away from my girlfriend!"
Three years later, sister Mary-Kate may have been feeling old resentments, when she allegedly
dissed Lohan during Fashion Week in 2011.
US Weekly reported Mary-Kate "flipped" when she wound up having to sit across from LiLo,
with a source claiming,
"She looked so upset about her seat and kept looking over at Lindsay."
John Stamos
The Olsen twins and John Stamos have a near-mythical feud that's spanned several decades.
In 2018, Radar Online reported that the 54-year-old actor had banned Mary-Kate and Ashley from
his wedding, allegedly to punish the sisters for passing up on Fuller House.
According to an insider:
"John says they're stuck-up and unappreciative.
He didn't want them around for his special 'I do' moment."
As far back as 1987, Stamos reportedly wanted the actresses fired from Full House because
they were big ol' crybabies.
Like, actual babies - who cried.
Stamos told People in 2015,
"It was very difficult to get the shot.
So I [said], 'Get them out!'
That is actually 100 percent accurate."
Even recently, when the Olsen twins alleged said they had no idea Fuller House was happening,
Stamos wrote in a since-deleted tweet:
"I call bulls---."
Ingrid Newkirk
When she dies, PETA President Ingrid Newkirk plans to send her liver to France to protest
pâté.
But until then, she'll happily troll celebrities who wear fur - and the Olsen twins are no
exception.
In 2007, Newkirk devoted an entire website to shaming the sisters.
An offshoot site by PETA introduced the world to "The Trollsen Twins", Hairy-Kate and Trashley,
and let shellshocked visitors venture into the, quote, "Full House of Horrors", which
revealed the fur in its previously living form.
Spencer Pratt
Here's a surefire way to tell whether someone hates you: They brag to Details about the
time they sold an embarrassing high school photo of you to the tabloids for $50,000.
And according to People, that's something Spencer Pratt is particularly proud of.
And that might be why Mary-Kate had nothing nice to say about Pratt during her 2008 appearance
on The Late Show.
Letterman called Pratt a "worm" and commented,
"He's not much older than you are.
Or maybe he is your age?
How does he get to be so oily at that age?
Hard to know, isn't it?"
"Yeah, it's a mystery to me."
The next morning, in retaliation, Pratt told Us Weekly,
"I know I've made it in Hollywood when a famous troll is talking about me on Letterman.
I forgive her, though.
[…] She's had to go through life as the less cute twin, which must be tough."
Lori Loughlin
In 2015, when word got out that Netflix was resurrecting Full House, most former cast-mates
were quick to sign on to the project and sing the show's praises.
But sources told Radar Online that Fuller House was marred from the start by behind-the-scenes
drama.
And a lot of it reportedly had to do with Mary-Kate and Ashley - who had yet to confirm
whether or not they'd be returning to the show.
The source claimed,
"Mary-Kate and Ashley are the only ones out of that entire cast that don't talk regularly.
The rest of them have remained a family since the show ended, but no one can really tolerate
Mary-Kate or Ashley."
Lori Loughlin, who played Aunt Becky on the show, told Access Online,
"It doesn't matter how much money they get paid.
They don't care.
I honestly don't know if they want to do it."
Meanwhile, a source told Radar Online that the Olsens told producers they wouldn't return
to the show because it wouldn't be good for their image.
Nevertheless, the source continued,
"No one really wants them to come back."
No comments:
Post a Comment